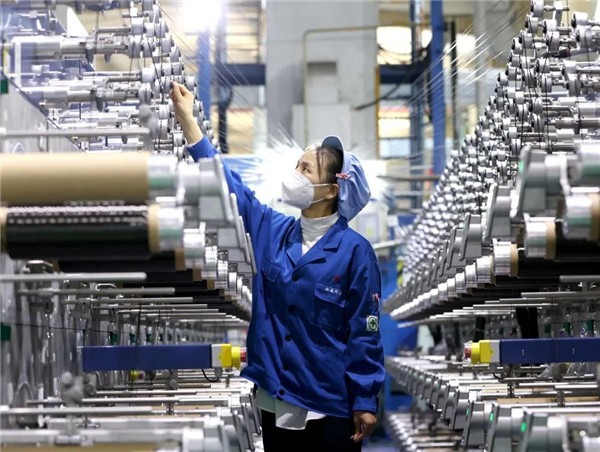
The foundation of continuous improvements is PDCA, or Plan, Do, Check, Act. This method of continuous improvement is very effective and can deliver significant results if implemented correctly. Employee involvement is key to continuous improvement, and a variety of resources are required to execute the process. Although measurement and costs are crucial to the process they are not the only benefits. Without customers and employees, the PDCA Cycle is incomplete.
PDCA cycle
Continuous improvement is possible by applying the PDCA cycle in every area of your business. This cycle is about improving process and continuing to improve on the previous ones. You may be able to see new trends in the data as the team tests a new process or you may uncover a new baseline, both of which reveal new areas for improvement. While the PDCA is a useful tool to identify improvement opportunities, it requires that you apply it with care and control.
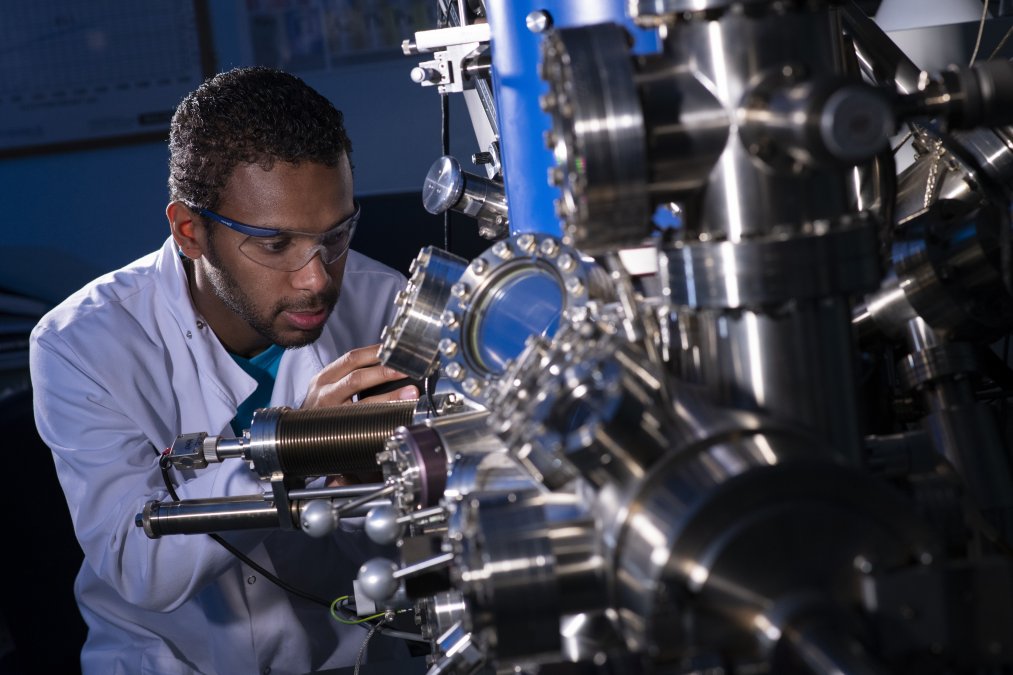
Employee participation
Although employee involvement is often called many things, it is a concept that all organizations recognize as important. Research has shown that employee engagement is directly linked to positive work outcomes. There are several types of employee involvement: direct communication, representative participation through unions and upward problem solving. These types of employee involvement can be reinforced by the culture, environment and leadership of the organization. Here are some examples.
Measurement
Many companies have begun to incorporate measurements in their continuous improvement plans. W. Edwards Deming introduced The Deming Cycle. This cycle includes a Check phase which assesses how well an improvement program is meeting its goals. If results are below expectations, changes are made to improve the process. Until satisfactory results are achieved, the cycle is repeated. Continuous improvement processes are an integral part of the process.
Costs
An enterprise-wide cost assessment of CI efforts is necessary to ensure that the benefits outweigh the costs. Cost-benefit analyses should be driven by the business imperative of increasing customer satisfaction and employee involvement scores. The ROI of CI initiatives should be included in the cost-benefit analysis, as well as fine-tuning budgets. This will ensure that the initiative is a success. It should examine the effectiveness of key business processes, and benchmark them against industry standards and other leading competitors.
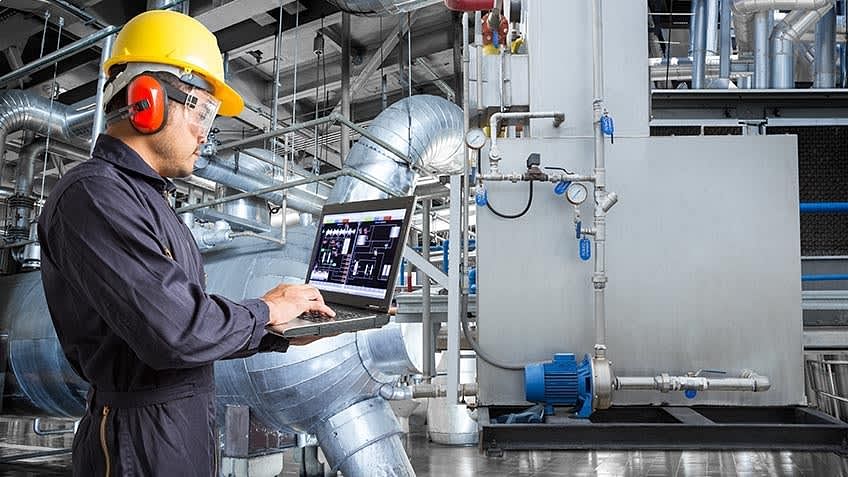
Benefits
Constant improvement offers clear benefits. Focusing on learning and failure will lead to more breakthroughs. If you encourage your employees to identify potential areas of improvement, it will help them take control of their work and make the company feel invested in them. The same goes for a team that works on new technology or tools testing. This can lead to empowered employees. Constant improvement can bring more benefits than simply saving money. Employee satisfaction is improved and work can be made easier by making positive changes.
FAQ
What does "warehouse" mean?
A warehouse is an area where goods are stored before being sold. It can be indoors or out. In some cases it could be both indoors and outdoors.
What is the responsibility for a logistics manager
Logistics managers ensure that goods arrive on time and are unharmed. This is done using his/her knowledge of the company's products. He/she also needs to ensure adequate stock to meet demand.
How can excess manufacturing production be reduced?
Improved inventory management is the key to reducing overproduction. This would reduce the time needed to manage inventory. We could use these resources to do other productive tasks.
Kanban systems are one way to achieve this. A Kanbanboard is a visual tool that allows you to keep track of the work being done. Kanban systems allow work items to move through different states until they reach their final destination. Each state represents a different priority level.
To illustrate, work can move from one stage or another when it is complete enough for it to be moved to a new stage. However, if a task is still at the beginning stages, it will remain so until it reaches the end of the process.
This helps to keep work moving forward while ensuring that no work is left behind. Managers can view the Kanban board to see how much work they have done. This information allows them to adjust their workflow based on real-time data.
Lean manufacturing, another method to control inventory levels, is also an option. Lean manufacturing focuses on eliminating waste throughout the entire production chain. Anything that doesn't add value to the product is considered waste. Some common types of waste include:
-
Overproduction
-
Inventory
-
Packaging not required
-
Excess materials
Manufacturers can increase efficiency and decrease costs by implementing these ideas.
What skills is required for a production planner?
To become a successful production planner, you need to be organized, flexible, and able to multitask. Effective communication with clients and colleagues is essential.
What are my options for learning more about manufacturing
Experience is the best way for you to learn about manufacturing. You can also read educational videos or take classes if this isn't possible.
What are the 7 Rs of logistics?
The acronym 7R's of Logistic is an acronym that stands for seven fundamental principles of logistics management. It was developed by the International Association of Business Logisticians (IABL) and published in 2004 as part of its "Seven Principles of Logistics Management" series.
The acronym consists of the following letters:
-
Responsive - ensure all actions are legal and not harmful to others.
-
Reliable - Have confidence in your ability to fulfill all of your commitments.
-
Reasonable - make sure you use your resources well and don't waste them.
-
Realistic - Consider all aspects of operations, including environmental impact and cost effectiveness.
-
Respectful - treat people fairly and equitably.
-
Resourceful - look for opportunities to save money and increase productivity.
-
Recognizable is a company that provides customers with value-added solutions.
What is production planning?
Production Planning is the creation of a plan to cover all aspects, such as scheduling, budgeting. Location, crew, equipment, props and other details. This document will ensure everything is in order and ready to go when you need it. You should also have information to ensure the best possible results on set. This includes shooting schedules, locations, cast lists, crew details, and equipment requirements.
The first step in filming is to define what you want. You may have already chosen the location you want, or there are locations or sets you prefer. Once you have identified your locations and scenes, you can start working out which elements you require for each scene. Perhaps you have decided that you need to buy a car but aren't sure which model. To narrow your options, you can search online for available models.
Once you have found the right vehicle, you can think about adding accessories. Are you looking for people to sit in the front seats? Maybe you need someone to move around in the back. Perhaps you would like to change the interior colour from black to white. These questions will help to determine the style and feel of your car. It is also worth considering the types of shots that you wish to take. Are you going to be shooting close-ups? Or wide angles? Maybe you want to show your engine or the steering wheel. These things will help you to identify the car that you are looking for.
Once you have made all the necessary decisions, you can start to create a schedule. You can use a schedule to determine when and where you need it to be shot. The schedule will show you when to get there, what time to leave, and when to return home. So everyone is clear about what they need to do. You can also make sure to book extra staff in advance if you have to hire them. You should not hire anyone who doesn't show up because of your inaction.
Also, consider how many days you will be filming your schedule. Some projects are quick and easy, while others take weeks. While creating your schedule, it is important to remember whether you will require more than one shot per day. Multiplying takes in the same area will result both in increased costs and a longer time. It is better to be cautious and take fewer shots than you risk losing money if you are not sure if multiple takes are necessary.
Budgeting is another important aspect of production planning. As it will allow you and your team to work within your financial means, setting a realistic budget is crucial. Remember that you can always reduce the budget later on if you run into unforeseen problems. You shouldn't underestimate the amount you'll spend. Underestimating the cost will result in less money after you have paid for other items.
Production planning can be a complex process. However, once you know how everything works together it will become easier to plan future projects.
Statistics
- Job #1 is delivering the ordered product according to specifications: color, size, brand, and quantity. (netsuite.com)
- According to a Statista study, U.S. businesses spent $1.63 trillion on logistics in 2019, moving goods from origin to end user through various supply chain network segments. (netsuite.com)
- In the United States, for example, manufacturing makes up 15% of the economic output. (twi-global.com)
- In 2021, an estimated 12.1 million Americans work in the manufacturing sector.6 (investopedia.com)
- (2:04) MTO is a production technique wherein products are customized according to customer specifications, and production only starts after an order is received. (oracle.com)
External Links
How To
Six Sigma: How to Use it in Manufacturing
Six Sigma is "the application statistical process control (SPC), techniques for continuous improvement." Motorola's Quality Improvement Department, Tokyo, Japan, developed it in 1986. Six Sigma's basic concept is to improve quality and eliminate defects through standardization. This method has been adopted by many companies in recent years as they believe there are no perfect products or services. Six Sigma's primary goal is to reduce variation from the average value of production. If you take a sample and compare it with the average, you will be able to determine how much of the production process is different from the norm. If there is a significant deviation from the norm, you will know that something needs to change.
Understanding how variability works in your company is the first step to Six Sigma. Once you understand this, you can then identify the causes of variation. Also, you will need to identify the sources of variation. Random variations occur when people do mistakes. Symmetrical variations are caused due to factors beyond the process. You could consider random variations if some widgets fall off the assembly lines. But if you notice that every widget you make falls apart at the exact same place each time, this would indicate that there is a problem.
Once you identify the problem areas, it is time to create solutions. You might need to change the way you work or completely redesign the process. To verify that the changes have worked, you need to test them again. If they don't work you need to rework them and come up a better plan.