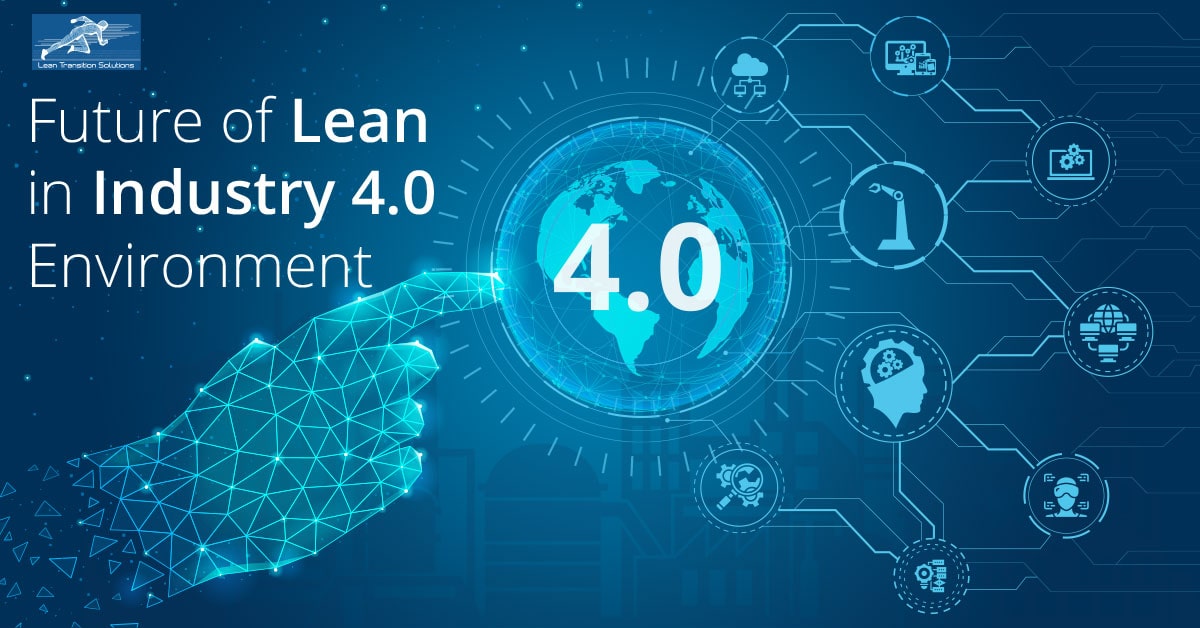
Originally known as Just-in-Time production, Toyota Production System is an integrated socio-technical system that is used to eliminate waste and improve processes. It organizes manufacturing, logistics, customer interaction, and production. It also drives continuous improvement and employee development. It is also the foundation for Lean Manufacturing. Toyota Production System has been applied to many manufacturing facilities in the United States and overseas.
Sakichi Tomoda, Toyota's founder, developed the Toyota Production System. Sakichi Toyoda analyzed each phase of his company's production, and removed all unnecessary parts. This led to a 20% decrease of build time. Toyota was able to make a vehicle in half as fast as GM. Toyota was at the brink of bankruptcy in the early 1950s.
In the mid-1940s, Toyota's executive Taiichi Ohno observed the shelf-stocking process at a supermarket. He realized that Just in Time production of vehicles could be time-saving. He collaborated with EijiToyoda, Toyota's president, to develop the Toyota Production System in 1948-1975.
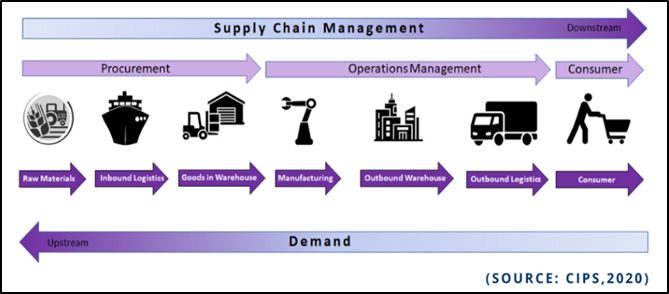
Toyota Production System was designed in order to eliminate waste. Kaizen, which means continuous improvement in Japanese, is the basis of the system's philosophy. Toyota Production System (TPS) is continually improving to meet the needs. It drives learning throughout the company and uses simple yet effective low-tech tools combined with advanced production techniques. It uses innovative information technology and unique management practices.
The Toyota Production System was built around six core principles. It has been adopted by many companies like Boeing, Porsche, Honda and others. These companies reengineered production processes to mimic Toyota's.
Toyota Production System also offers team building activities. These activities include weekly local leader safety rounds, which evaluate the performance of staff with key safety initiatives. Each member of the team is encouraged share their ideas and to find ways to improve. This has influenced the culture of the company.
Jidoka is another concept. It refers to automation with a human hand. Jidoka encourages workers inspect their work and stop production if they find any problems. Jidoka encourages workers to inspect their work and stop production when they find problems.
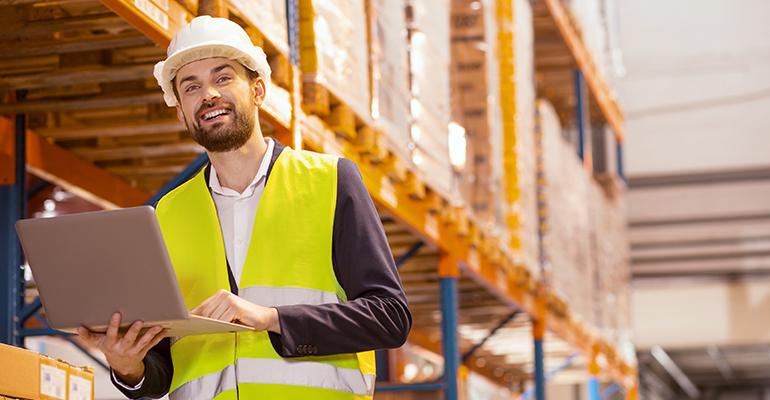
Visual control is another feature of the Toyota Production System. It allows for work instructions to be clearly visible on the factory floors. This helps workers follow instructions precisely. The company also uses poka-yoke devices to verify quality standards. These devices can also be used for identifying red rabbits.
The Toyota Production System is not only applicable to manufacturing plants, but also health care. It can be used to improve patient satisfaction. It can also be applied to critical care and the operating room.
Utilizing the Toyota Production System it is possible improve patient satisfaction, and to deliver better health care. A case study report published in 2003 by the EPA indicates that Toyota's advances in waste reduction caught the EPA's attention. This led the EPA to form a partnership in 2003 with several companies including the St. Bernard Project that employs military veterans.
FAQ
What are the differences between these four types?
Manufacturing is the process of transforming raw materials into useful products using machines and processes. It can involve many activities like designing, manufacturing, testing packaging, shipping, selling and servicing.
What is the difference between Production Planning, Scheduling and Production Planning?
Production Planning (PP) refers to the process of determining how much production is needed at any given moment. Forecasting demand is one way to do this.
Scheduling involves the assignment of dates and times to tasks in order to complete them within the timeframe.
What types of jobs can you find in logistics
There are many types of jobs in logistics. Some examples are:
-
Warehouse workers – They load and unload pallets and trucks.
-
Transport drivers - These are people who drive trucks and trailers to transport goods or perform pick-ups.
-
Freight handlers: They sort and package freight in warehouses.
-
Inventory managers – They manage the inventory in warehouses.
-
Sales reps - They sell products and services to customers.
-
Logistics coordinators: They plan and manage logistics operations.
-
Purchasing agents - They buy goods and services that are necessary for company operations.
-
Customer service representatives are available to answer customer calls and emails.
-
Ship clerks - They issue bills and process shipping orders.
-
Order fillers – They fill orders based upon what was ordered and shipped.
-
Quality control inspectors – They inspect incoming and outgoing products to ensure that there are no defects.
-
Others - There is a variety of other jobs in logistics. These include transportation supervisors and cargo specialists.
Statistics
- (2:04) MTO is a production technique wherein products are customized according to customer specifications, and production only starts after an order is received. (oracle.com)
- You can multiply the result by 100 to get the total percent of monthly overhead. (investopedia.com)
- Many factories witnessed a 30% increase in output due to the shift to electric motors. (en.wikipedia.org)
- In the United States, for example, manufacturing makes up 15% of the economic output. (twi-global.com)
- Job #1 is delivering the ordered product according to specifications: color, size, brand, and quantity. (netsuite.com)
External Links
How To
How to Use the Just In Time Method in Production
Just-intime (JIT), a method used to lower costs and improve efficiency in business processes, is called just-in-time. It allows you to get the right amount resources at the right time. This means you only pay what you use. Frederick Taylor first coined this term while working in the early 1900s as a foreman. He noticed that workers were often paid overtime when they had to work late. He decided to ensure workers have enough time to do their jobs before starting work to improve productivity.
JIT is an acronym that means you need to plan ahead so you don’t waste your money. You should also look at the entire project from start to finish and make sure that you have sufficient resources available to deal with any problems that arise during the course of your project. You will have the resources and people to solve any problems you anticipate. This will prevent you from spending extra money on unnecessary things.
There are many JIT methods.
-
Demand-driven JIT: This is a JIT that allows you to regularly order the parts/materials necessary for your project. This will allow to track how much material has been used up. This will allow you to calculate how long it will take to make more.
-
Inventory-based: This type allows you to stock the materials needed for your projects ahead of time. This allows you to forecast how much you will sell.
-
Project-driven: This approach involves setting aside sufficient funds to cover your project's costs. Knowing how much money you have available will help you purchase the correct amount of materials.
-
Resource-based JIT : This is probably the most popular type of JIT. Here, you allocate certain resources based on demand. For instance, if you have a lot of orders coming in, you'll assign more people to handle them. If there aren't many orders, you will assign fewer people.
-
Cost-based: This is similar to resource-based, except that here you're not just concerned about how many people you have but how much each person costs.
-
Price-based: This is a variant of cost-based. However, instead of focusing on the individual workers' costs, this looks at the total price of the company.
-
Material-based is an alternative to cost-based. Instead of looking at the total cost in the company, this method focuses on the average amount of raw materials that you consume.
-
Time-based: This is another variation of resource-based JIT. Instead of focusing solely on the amount each employee costs, focus on how long it takes for the project to be completed.
-
Quality-based JIT - This is another form of resource-based JIT. Instead of focusing on the cost of each worker or how long it takes, think about how high quality your product is.
-
Value-based JIT : This is the newest type of JIT. In this instance, you are not concerned about the product's performance or meeting customer expectations. Instead, your focus is on the value you bring to the market.
-
Stock-based: This is an inventory-based method that focuses on the actual number of items being produced at any given time. It's useful when you want maximum production and minimal inventory.
-
Just-in-time planning (JIT): This is a combination JIT and supply-chain management. It refers to the process of scheduling the delivery of components as soon as they are ordered. It is essential because it reduces lead-times and increases throughput.