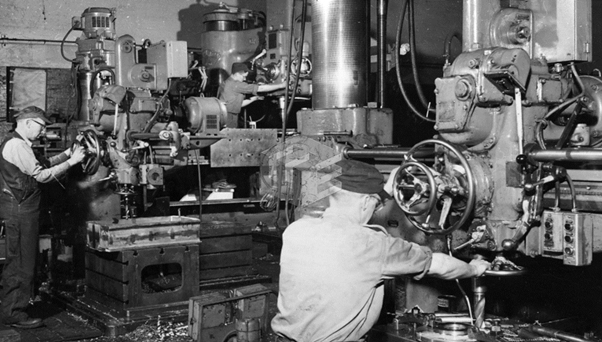
Getting the best value for your money is critical when choosing a course for your business. This course will help you to understand the importance of a procurement process and the role of procurement management within a business. These are some of the key factors you should consider when making your purchasing decision. Learn more about Cost-based pricing, Contracting and Negotiating to help you make the best deal for your business. Here are some of the key points to consider when selecting a course provider:
Pricing is based on costs
Future Procurement is a Cost Based pricing course designed for production and purchasing professionals. It's designed to assist both beginners and more experienced Procurement Professionals in understanding and using Cost-Based pricing in their everyday work. The online course can be downloaded for free and it is easy to learn about CBP. It can also be used to apply to other types of courses. CBP implementation in course procurement strategies is important.
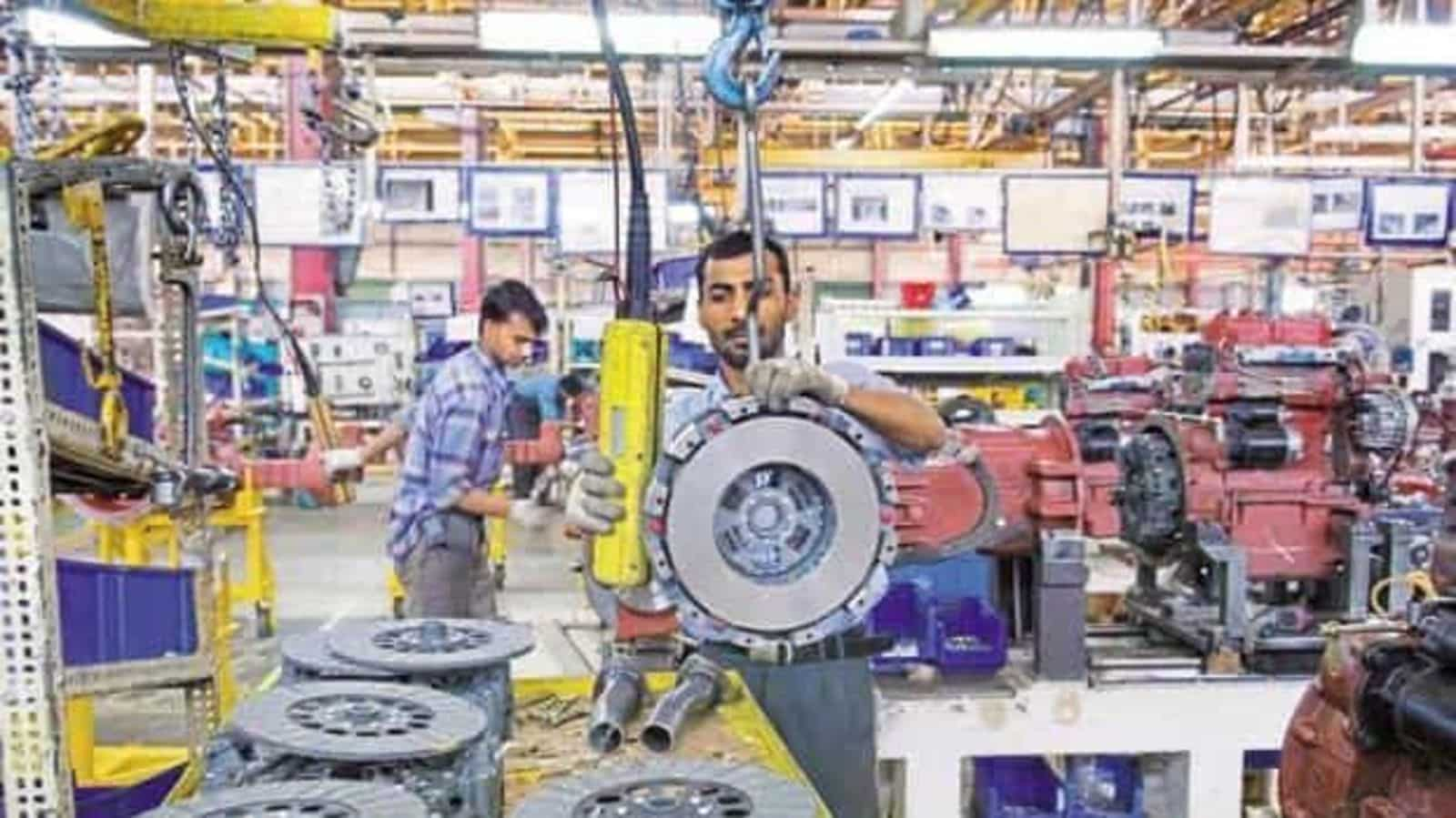
Negotiating
You can learn negotiation skills by taking a course. Negotiating courses come in many forms, from classroom to online. This course teaches you how to communicate effectively and build mutually beneficial relationships. You can also use this course to get a job as a negotiator. For more information about this course, read on. Here are some tips to make the most of this course.
Contracting
This workshop will be beneficial to students who want to pursue careers in contracting. The workshop will explain the various activities involved with the sourcing process. This workshop will benefit anyone involved with the procurement process, regardless of whether they are new to it or need to refresh their knowledge. Here are the different purposes of the workshop:
Collaboration with external partners
In a facilitated classroom setting, this course focuses on six sessions, each using case studies, workbooks, and real-world course procurement experiences. At the end of the course, participants will participate in a role-play exercise, gathering their learning and assessing their understanding of the training. Participants will be able to recognize and apply sales techniques and tactics. This article will discuss the benefits of this workshop as well as what you can anticipate from it.
Certification
You will learn all about supply chain management and the different processes involved with a Certificate in Course Procurement. The course also provides valuable insight into current trends and issues in the field. This course will enhance your negotiation and outcomes skills, giving your company an edge. The program should be completed in three years with a 2.5 grade point average. This course will also teach you about legal and regulatory considerations that affect the procurement process.
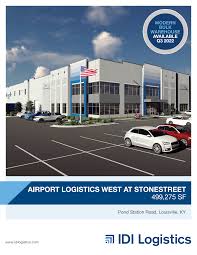
Course platforms
There are many platforms for course purchase. Each has its strengths as well as weaknesses. Some are premium, offering social learning tools and high interactivity. Others offer a simpler interface, with fewer features, and are simpler. Teachable remains the best option, as it was the first platform to offer online courses. You might want to consider other options if you are looking for a course that can easily be promoted to the general public.
FAQ
What is the distinction between Production Planning or Scheduling?
Production Planning (PP), or production planning, is the process by which you determine what products are needed at any given time. This can be done by forecasting demand and identifying production capabilities.
Scheduling is the process of assigning specific dates to tasks so they can be completed within the specified timeframe.
Are there any Manufacturing Processes that we should know before we can learn about Logistics?
No. No. However, knowing about manufacturing processes will definitely give you a better understanding of how logistics works.
How does a production planner differ from a project manager?
The main difference between a production planner and a project manager is that a project manager is usually the person who plans and organizes the entire project, whereas a production planner is mainly involved in the planning stage of the project.
Statistics
- (2:04) MTO is a production technique wherein products are customized according to customer specifications, and production only starts after an order is received. (oracle.com)
- [54][55] These are the top 50 countries by the total value of manufacturing output in US dollars for its noted year according to World Bank.[56] (en.wikipedia.org)
- It's estimated that 10.8% of the U.S. GDP in 2020 was contributed to manufacturing. (investopedia.com)
- Many factories witnessed a 30% increase in output due to the shift to electric motors. (en.wikipedia.org)
- According to the United Nations Industrial Development Organization (UNIDO), China is the top manufacturer worldwide by 2019 output, producing 28.7% of the total global manufacturing output, followed by the United States, Japan, Germany, and India.[52][53] (en.wikipedia.org)
External Links
How To
How to Use 5S for Increasing Productivity in Manufacturing
5S stands in for "Sort", the "Set In Order", "Standardize", or "Separate". Toyota Motor Corporation developed the 5S method in 1954. It allows companies to improve their work environment, thereby achieving greater efficiency.
This method aims to standardize production processes so that they are repeatable, measurable and predictable. This means that daily tasks such as cleaning and sorting, storage, packing, labeling, and packaging are possible. Because workers know what they can expect, this helps them perform their jobs more efficiently.
Implementing 5S involves five steps: Sort, Set in Order, Standardize Separate, Store, and Each step is a different action that leads to greater efficiency. You can make it easy for people to find things later by sorting them. When you set items in an order, you put items together. You then organize your inventory in groups. Labeling your containers will ensure that everything is correctly labeled.
Employees will need to be more critical about their work. Employees need to understand the reasons they do certain jobs and determine if there is a better way. They must learn new skills and techniques in order to implement the 5S system.
The 5S Method not only improves efficiency, but it also helps employees to be more productive and happier. Once they start to notice improvements, they are motivated to keep working towards their goal of increasing efficiency.