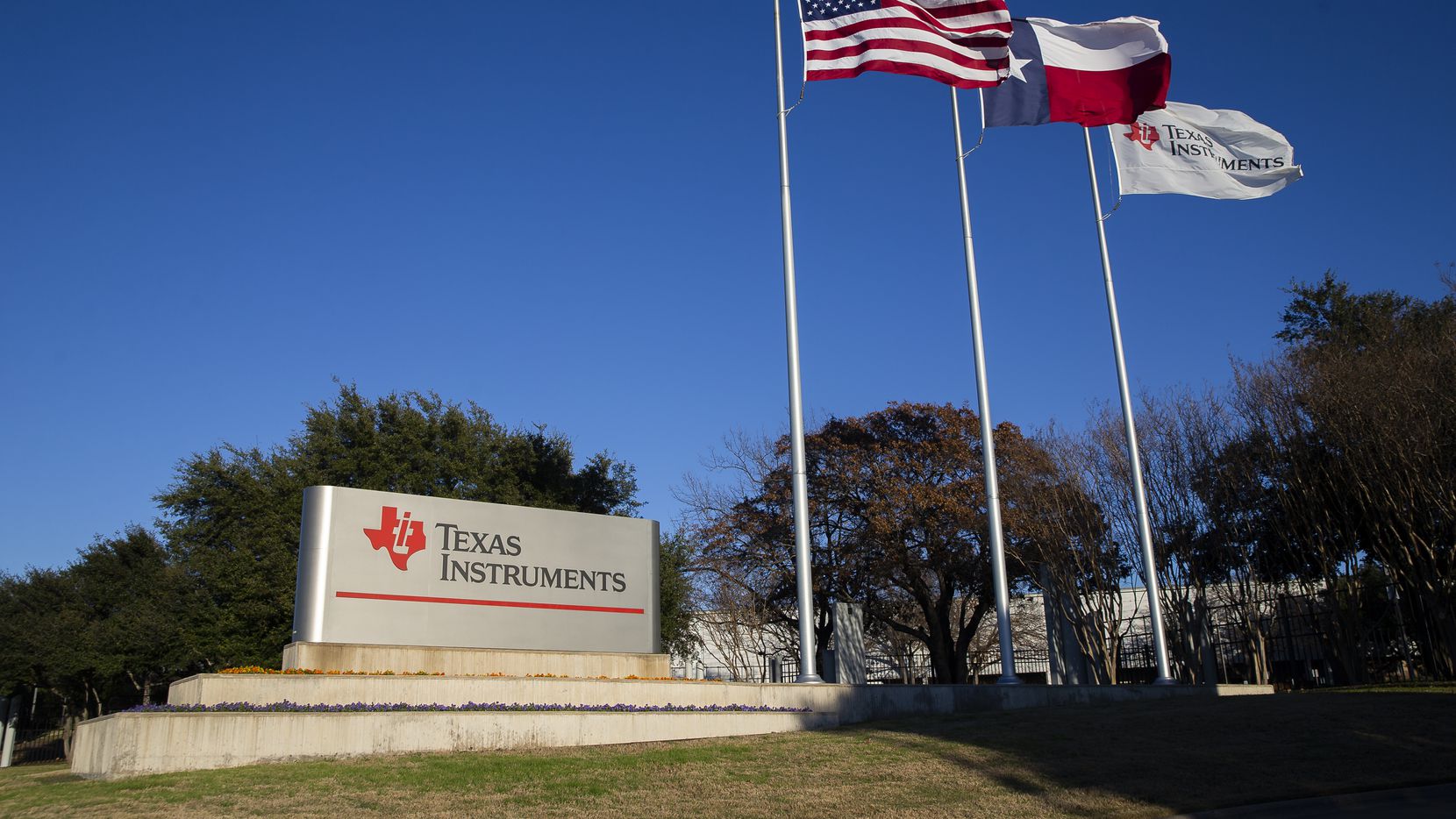
Opportunities in the manufacturing of wind turbines
Many tasks in the manufacturing of wind turbines require specialist knowledge and skills. These jobs may include blade epoxies, gears, and tower assembly. Some wind turbine manufacturing businesses also use third-party vendors to manufacture components. Wind turbine components are huge and must be transported efficiently and quickly. Companies need teams of logisticians as well as rail freight drivers to accomplish this task.
Jobs in wind turbine manufacturing typically require a bachelor's degree, though some require master's degrees. Wind turbine manufacturing jobs require both engineering and environmental engineering specializations. In addition to a degree, entry-level engineers must have advanced computer skills and experience. They work closely with more experienced staff to ensure quality control. They may also be asked to work on more complex projects.
Manufacturing of wind turbines: Processes
The main part of a windturbine is its blades. Each blade has two faces connected by integral shear Webs. The support for the blades is provided by a shell fairing and a spar. These structures are strong enough to withstand edgewise and flipwise loads. The spar resists the effects of wind pressure and gravitational forces on edgewise bending. The blades are shaped to withstand these forces.
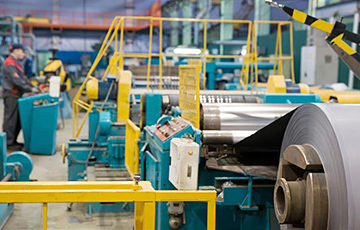
A variety of materials are used to create the blades. The most common material for commercial wind turbine blades is fiberglass, but aluminum and lightweight woods can also be used. The blades are then covered in airtight foil and connected to tubes that pump resin.
Competitors within the wind turbine manufacturing sector
While Chinese manufacturers are a growing force in the global wind industry, they are not yet the dominant player. In fact, Chinese turbine manufacturers have had trouble dethroning incumbent manufacturers in developed markets. Despite this, they may be poised to eventually increase their overseas activities if they invest in local manufacturing capabilities.
Many are opting to build their components themselves, even though large turbine companies are outsourcing increasingly many parts. This comes with both benefits and disadvantages. Companies such as Vestas in Pueblo, Colorado, have embraced this strategy, manufacturing wind turbine towers for third-party US projects. The agreement allows the tower facility to use up to 25 percent its production capacity and creates 100 local jobs. The downside to this approach is the weak quality control. There have been instances in the past when components that were outsourced failed, such as gearbox failures and blade cracking. Some offshore foundations are even made of poor quality steel.
Wind turbine manufacturing poses safety and health risks
In wind turbine manufacturing, safety and health is an important concern. The hazards faced by workers can result in long-term injuries or even fatalities. There are many ways to reduce this risk. This includes proper training and routine inspections. These tips will help you keep your employees safe at work in a windturbine manufacturing plant.
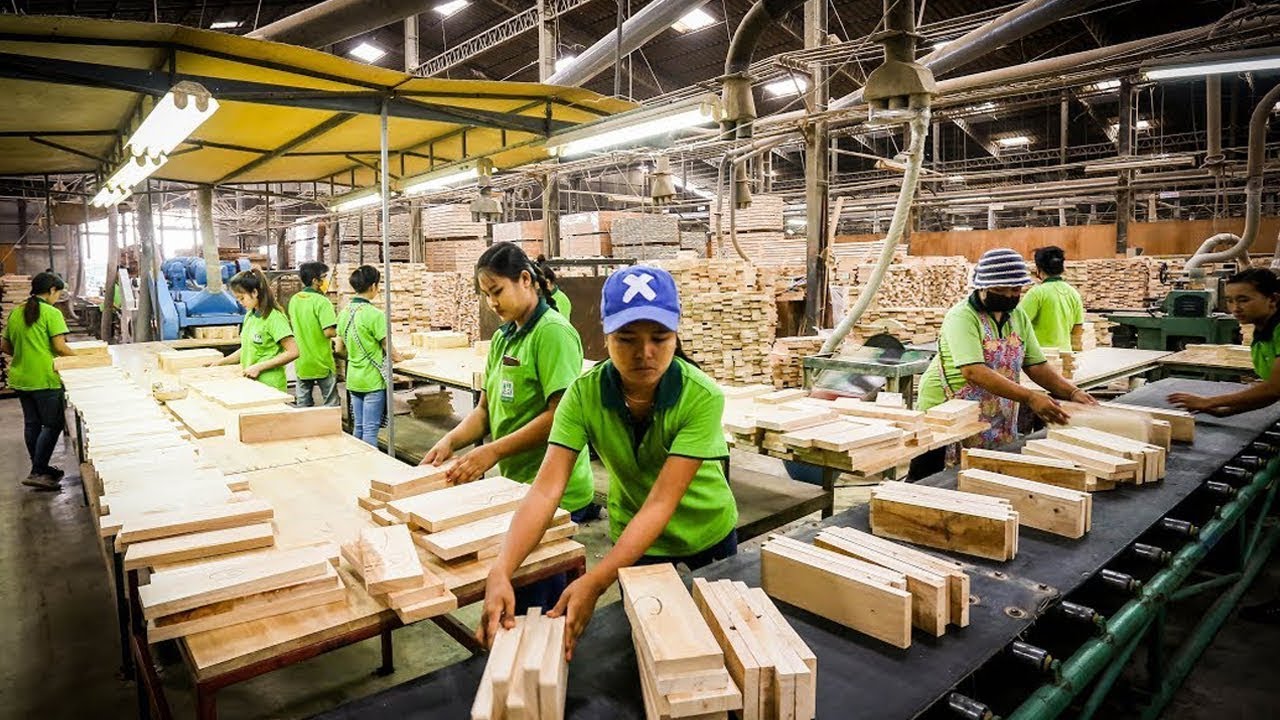
The exposure to toxic gases, vapors, or dust is one the most serious hazards of manufacturing wind turbine blades. To reduce the risk of exposure, workers should wear respirators and must be properly trained in using them. Ear protection is essential and requires good training.
FAQ
What does manufacturing mean?
Manufacturing Industries are companies that manufacture products. Consumers are those who purchase these products. To accomplish this goal, these companies employ a range of processes including distribution, sales, management, and production. They create goods from raw materials, using machines and various other equipment. This includes all types and varieties of manufactured goods, such as food items, clothings, building supplies, furnitures, toys, electronics tools, machinery vehicles, pharmaceuticals medical devices, chemicals, among others.
What makes a production planner different from a project manger?
The main difference between a production planner and a project manager is that a project manager is usually the person who plans and organizes the entire project, whereas a production planner is mainly involved in the planning stage of the project.
Is it necessary to be familiar with Manufacturing Processes before we learn about Logistics.
No. No. But, being familiar with manufacturing processes will give you a better understanding about how logistics works.
Why should you automate your warehouse?
Modern warehouses have become more dependent on automation. E-commerce has brought increased demand for more efficient and quicker delivery times.
Warehouses should be able adapt quickly to new needs. Technology investment is necessary to enable warehouses to respond quickly to changing demands. Automation of warehouses offers many benefits. These are some of the benefits that automation can bring to warehouses:
-
Increases throughput/productivity
-
Reduces errors
-
Improves accuracy
-
Boosts safety
-
Eliminates bottlenecks
-
Allows companies scale more easily
-
Workers are more productive
-
It gives visibility to everything that happens inside the warehouse
-
Enhances customer experience
-
Improves employee satisfaction
-
It reduces downtime, and increases uptime
-
This ensures that quality products are delivered promptly
-
Eliminates human error
-
Assure compliance with regulations
What is production management?
Production planning is the process of creating a plan that covers all aspects of production. This includes scheduling, budgeting and crew, location, equipment, props, and more. It is important to have everything ready and planned before you start shooting. It should also contain information on achieving the best results on set. This includes information on shooting times, locations, cast lists and crew details.
The first step is to decide what you want. You may have already chosen the location you want, or there are locations or sets you prefer. Once you have identified your locations and scenes it's time to begin figuring out what elements you will need for each one. Perhaps you have decided that you need to buy a car but aren't sure which model. If this is the case, you might start searching online for car models and then narrow your options by selecting from different makes.
Once you have found the right vehicle, you can think about adding accessories. Are you looking for people to sit in the front seats? Perhaps you have someone who needs to be able to walk around the back of your car. You may want to change the interior's color from black or white. These questions will help determine the look and feel you want for your car. Another thing you can do is think about what type of shots are desired. Do you want to film close-ups, or wider angles? Maybe you want to show the engine and the steering wheel. These details will help identify the exact car you wish to film.
Once you have made all the necessary decisions, you can start to create a schedule. You will know when you should start and when you should finish shooting. The schedule will show you when to get there, what time to leave, and when to return home. So everyone is clear about what they need to do. If you need to hire extra staff, you can make sure you book them in advance. You don't want to hire someone who won't show up because he didn't know.
It is important to calculate the amount of filming days when you are creating your schedule. Some projects only take one or two days, while others may last weeks. When you are creating your schedule, you should always keep in mind whether you need more than one shot per day or not. Multiple shots at the same location can increase costs and make it more difficult to complete. It is better to be cautious and take fewer shots than you risk losing money if you are not sure if multiple takes are necessary.
Budget setting is another important aspect in production planning. As it will allow you and your team to work within your financial means, setting a realistic budget is crucial. Keep in mind that you can always reduce your budget if you face unexpected difficulties. But, don't underestimate how much money you'll spend. If you underestimate the cost of something, you will have less money left after paying for other items.
Production planning can be a complex process. However, once you know how everything works together it will become easier to plan future projects.
What is the importance of automation in manufacturing?
Automating is not just important for manufacturers, but also for service providers. They can provide services more quickly and efficiently thanks to automation. It reduces human errors and improves productivity, which in turn helps them lower their costs.
What does it take for a logistics enterprise to succeed?
To be a successful businessman in logistics, you will need many skills and knowledge. Effective communication skills are necessary to work with suppliers and clients. You need to understand how to analyze data and draw conclusions from it. You must be able to work well under pressure and handle stressful situations. You need to be innovative and creative to come up with new ways to increase efficiency. You must be a strong leader to motivate others and direct them to achieve organizational goals.
You must be organized to meet tight deadlines.
Statistics
- It's estimated that 10.8% of the U.S. GDP in 2020 was contributed to manufacturing. (investopedia.com)
- [54][55] These are the top 50 countries by the total value of manufacturing output in US dollars for its noted year according to World Bank.[56] (en.wikipedia.org)
- (2:04) MTO is a production technique wherein products are customized according to customer specifications, and production only starts after an order is received. (oracle.com)
- In the United States, for example, manufacturing makes up 15% of the economic output. (twi-global.com)
- Job #1 is delivering the ordered product according to specifications: color, size, brand, and quantity. (netsuite.com)
External Links
How To
How to use 5S to increase Productivity in Manufacturing
5S stands to stand for "Sort", “Set In Order", “Standardize", and "Store". Toyota Motor Corporation created the 5S methodology in 1954. It allows companies to improve their work environment, thereby achieving greater efficiency.
The idea behind standardizing production processes is to make them repeatable and measurable. This means that daily tasks such as cleaning and sorting, storage, packing, labeling, and packaging are possible. Through these actions, workers can perform their jobs more efficiently because they know what to expect from them.
Five steps are required to implement 5S: Sort, Set In Order, Standardize. Separate. Each step involves a different action which leads to increased efficiency. If you sort items, it makes them easier to find later. When you arrange items, you place them together. After you have divided your inventory into groups you can store them in easy-to-reach containers. Make sure everything is correctly labeled when you label your containers.
Employees need to reflect on how they do their jobs. Employees need to be able understand their motivations and discover alternative ways to do them. In order to use the 5S system effectively, they must be able to learn new skills.
The 5S Method not only improves efficiency, but it also helps employees to be more productive and happier. Once they start to notice improvements, they are motivated to keep working towards their goal of increasing efficiency.