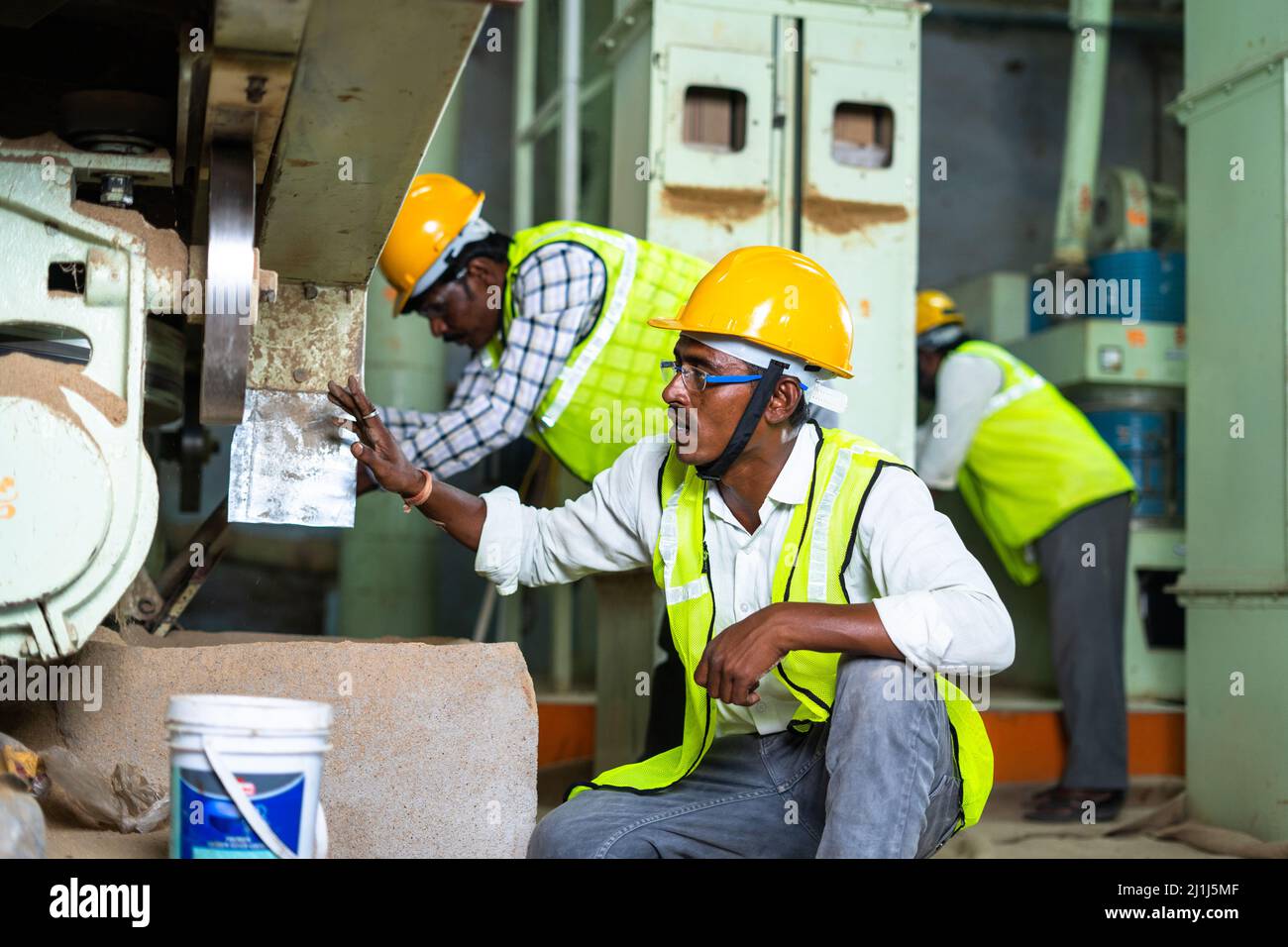
General managers are responsible in formulating strategies, hiring functional leaders and communicating with stakeholders. This article will discuss the responsibilities and skills required to excel in this position. For a complete overview of the general manager duties, read on. To be a successful general manager, you'll need strong communication and presentation skills. Also, you must be proficient at financial management. Ultimately, your success depends on your persistence and ability to manage your company's performance and processes within a budget. You must be a great leader and build trust with customers.
GMs are responsible for strategy formulation
The process of strategy formulation is a responsibility for GMs, but there are some risks. One example is a GM that is motivated by self or a member of a team, and may overplay their part in strategy formulation. This is because managers are subject to their own personal motivations and biases, and their decisions may not be based on objective data, but rather on personal interpretations and assumptions.
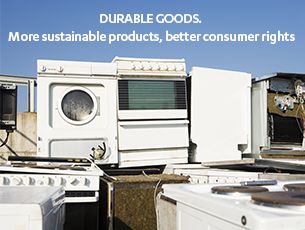
They employ functional leaders
General managers have broad responsibilities for the organization as well as its business units. This requires them to manage all aspects of the company, including budgets, strategy, structure and people. They are also responsible in the day to day operations of the business unit. They must be fluent in finance, sales and human resource management to effectively execute the strategy. In addition to ensuring the success of the entire organisation, the role of a general manager is highly complex.
They are close to their subordinates
The general manager's role requires them understand the organizational structure and communicate with all departments. They must also have strong analytical skills in order to recognize problems and come up with appropriate solutions. The role of the general manager is to manage tasks and ensure employees do their best. It is also important for general managers to communicate clearly with subordinates and work in close collaboration with other departments.
They communicate with each other
Communication skills are crucial in many general manager roles. General managers can train employees and host training sessions to help them improve their communication skills. To foster better communication, they can host more team meetings or social events. Here are some suggestions to improve communication skills among managers. Good managers should be open to their employees and help them succeed. This is a crucial part of their job description. They should be available to answer your questions and give guidance whenever necessary.
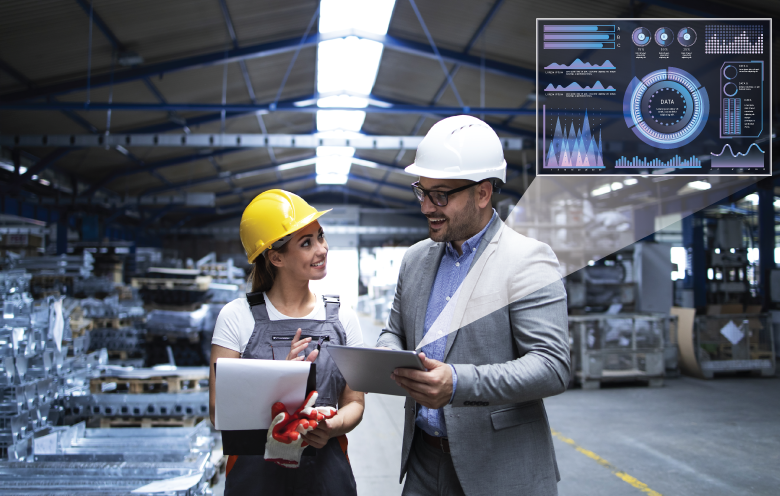
They are motivating
Top GMs have the ability to motivate employees. They are willing to work long hours, show a dedication to the business and set an example for their subordinates. They also reinforce their high standards in small ways. Here are some examples of how top managers motivate staff.
FAQ
What does warehouse mean?
A warehouse, or storage facility, is where goods are stored prior to being sold. It can be an outdoor or indoor area. It may also be an indoor space or an outdoor area.
Can certain manufacturing steps be automated?
Yes! Since ancient times, automation has been in existence. The Egyptians invent the wheel thousands of year ago. Nowadays, we use robots for assembly lines.
There are many applications for robotics in manufacturing today. These include:
-
Automated assembly line robots
-
Robot welding
-
Robot painting
-
Robotics inspection
-
Robots that make products
Automation could also be used to improve manufacturing. 3D printing is a way to make custom products quickly and without waiting weeks or months for them to be manufactured.
How can manufacturing prevent production bottlenecks?
Avoiding production bottlenecks is as simple as keeping all processes running smoothly, from the time an order is received until the product ships.
This includes planning for both capacity requirements and quality control measures.
Continuous improvement techniques such Six Sigma can help you achieve this.
Six Sigma can be used to improve the quality and decrease waste in all areas of your company.
It is focused on creating consistency and eliminating variation in your work.
Statistics
- In 2021, an estimated 12.1 million Americans work in the manufacturing sector.6 (investopedia.com)
- According to the United Nations Industrial Development Organization (UNIDO), China is the top manufacturer worldwide by 2019 output, producing 28.7% of the total global manufacturing output, followed by the United States, Japan, Germany, and India.[52][53] (en.wikipedia.org)
- You can multiply the result by 100 to get the total percent of monthly overhead. (investopedia.com)
- (2:04) MTO is a production technique wherein products are customized according to customer specifications, and production only starts after an order is received. (oracle.com)
- Job #1 is delivering the ordered product according to specifications: color, size, brand, and quantity. (netsuite.com)
External Links
How To
How to Use the Just-In-Time Method in Production
Just-intime (JIT), a method used to lower costs and improve efficiency in business processes, is called just-in-time. It is a process where you get the right amount of resources at the right moment when they are needed. This means that you only pay the amount you actually use. Frederick Taylor developed the concept while working as foreman in early 1900s. Taylor observed that overtime was paid to workers if they were late in working. He realized that workers should have enough time to complete their jobs before they begin work. This would help increase productivity.
JIT is about planning ahead. You should have all the necessary resources ready to go so that you don’t waste money. The entire project should be looked at from start to finish. You need to ensure you have enough resources to tackle any issues that might arise. If you anticipate that there might be problems, you'll have enough people and equipment to fix them. This way, you won't end up paying extra money for things that weren't really necessary.
There are several types of JIT techniques:
-
Demand-driven: This JIT is where you place regular orders for the parts/materials that are needed for your project. This will let you track the amount of material left over after you've used it. This will allow to you estimate the time it will take for more to be produced.
-
Inventory-based: You stock materials in advance to make your projects easier. This allows one to predict how much they will sell.
-
Project-driven : This is a method where you make sure that enough money is set aside to pay the project's cost. Knowing how much money you have available will help you purchase the correct amount of materials.
-
Resource-based JIT: This is the most popular form of JIT. You assign certain resources based off demand. You might assign more people to help with orders if there are many. If you don't have many orders, you'll assign fewer people to handle the workload.
-
Cost-based: This is a similar approach to resource-based but you are not only concerned with how many people you have, but also how much each one costs.
-
Price-based: This approach is very similar to the cost-based method except that you don't look at individual workers costs but the total cost of the company.
-
Material-based: This is quite similar to cost-based, but instead of looking at the total cost of the company, you're concerned with how much raw materials you spend on average.
-
Time-based JIT: A variation on resource-based JIT. Instead of worrying about how much each worker costs, you can focus on how long the project takes.
-
Quality-based JIT - This is another form of resource-based JIT. Instead of worrying about the costs of each employee or how long it takes for something to be made, you should think about how quality your product is.
-
Value-based JIT: This is the latest form of JIT. This is where you don't care about how the products perform or whether they meet customers' expectations. Instead, you are focused on adding value to the marketplace.
-
Stock-based. This method is inventory-based and focuses only on the actual production at any given point. This is used to increase production and minimize inventory.
-
Just-in-time planning (JIT): This is a combination JIT and supply-chain management. It is the process of scheduling components' delivery as soon as they have been ordered. This is important as it reduces lead time and increases throughput.