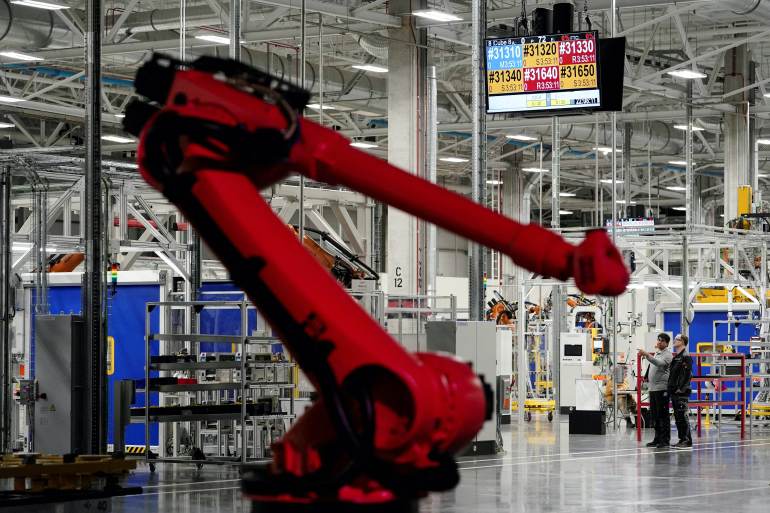
If you're looking to a career with chemistry, you might be curious as to what a salary for a chemical chemist. Below you will find the average salary for a chemist and information about how much each degree can pay. A bachelor's level chemistry degree can pay you $50,000 to over 100,000. Depending on the area you live, the degree you earn, and the employer you work for, you can expect to earn anywhere from fifty thousand to over a million dollars per year.
Average chemist salary
According to the Bureau of Labor Statistics the average starting salary in chemistry is $81,870 per annum. The highest-paid chemists make more than $130,000 per year. The lowest-paid chemical professionals earn $42,960 each year. Most chemist jobs can be found in the pharmaceutical and medicine manufacturing industries. The highest starting salary for chemistry comes from the oil and gaz industry. According to the Bureau of Labor Statistics there will be an increase of 7 percent in chemist employment over the next ten years. Higher salaries are available for graduates with lab experience than for those without.
The average chemistry salary will vary depending on your experience and where you are located. The salary of a chemical professional can vary depending on your education and experience. A California chemist with experience can earn $85,114 per annum. However, salaries in other states are higher. A PhD is a great way to increase your income if you are a chemist.
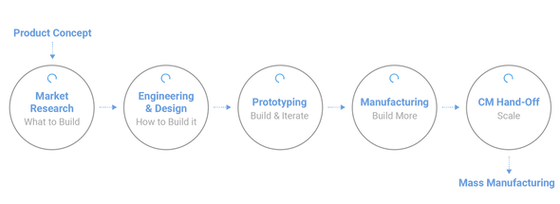
For chemists with a bachelor's, the salary range is
A chemistry degree could lead to a career in many different fields. According to the Bureau of Labor Statistics in 2010, there were 82,000 chemists living in the United States. A bachelor's degree in chemistry is sufficient to get a job in the field, but a graduate degree will allow you to earn more and take on more responsibility. According to the American Chemical Society (ACS), a chemist earns a median salary of $40,000 per year, but a Ph.D. starts at $85,000.
While a career in chemical engineering can be extremely lucrative, salary is not the only thing to consider. A Ph.D. (in chemistry) can pay upwards to $60,000 depending on experience and job type. Chemists with the highest salaries work in government research, teaching, and at universities.
The salary range for chemists who have a master's degree
A chemistry master’s degree can make a person earn as much as 128,000 USD each year. Salary ranges differ greatly for this profession, though they are often close to the median. An experienced graduate can earn around forty thousand euros with just two years' experience. An experienced chemist with over ten years' experience can earn up 239,000 USD per annum.
Many chemistry positions require a master's degree or Ph.D., though they can be obtained with a bachelor's degree. Graduates often specialize in a subfield. According to the American Chemical Society the median starting salary of a chemist who has a bachelor's in chemical engineering was $43,000. For those who worked in companies with over 25,000 employees, the salary was $50,000.
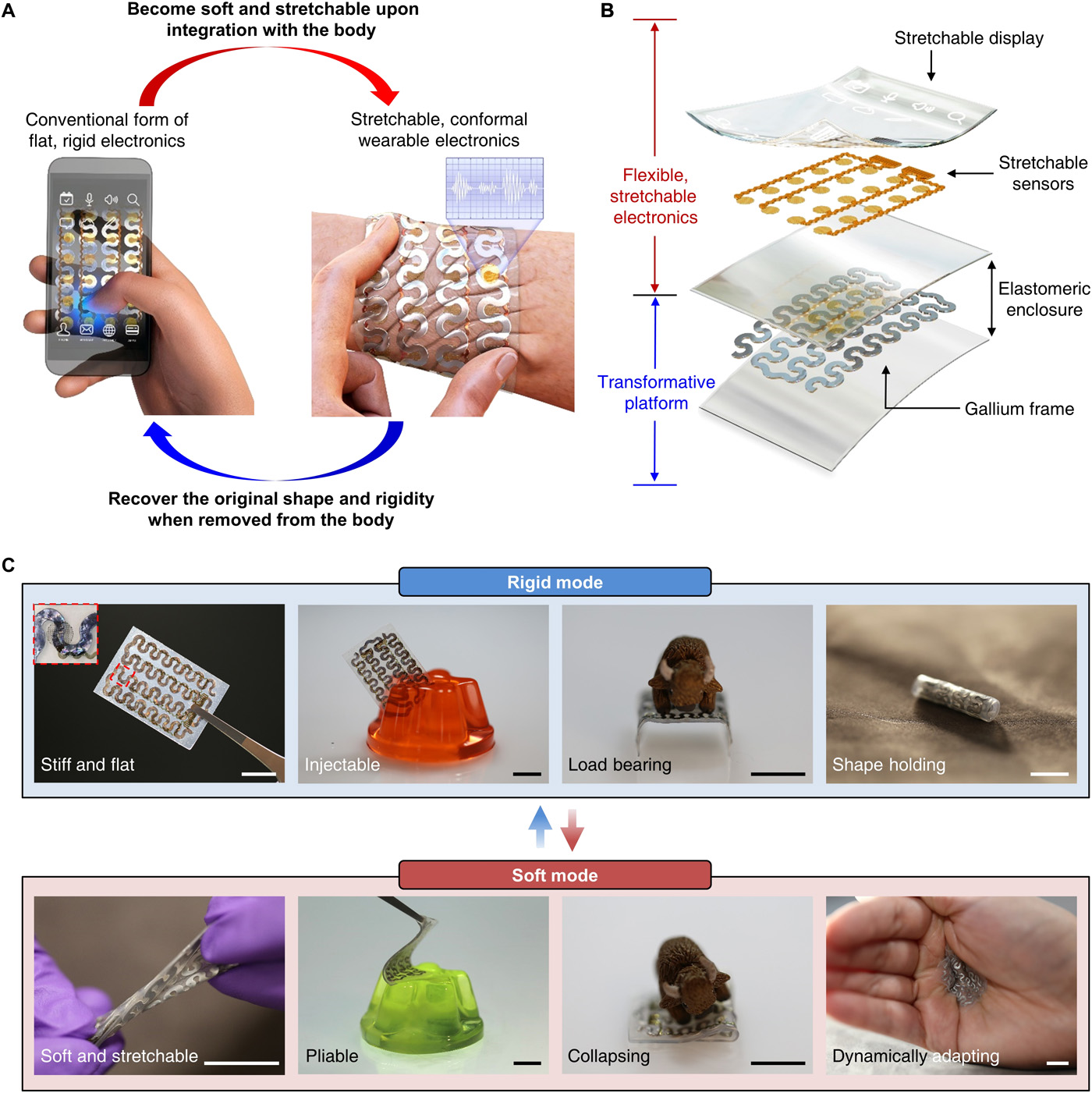
For chemists with Ph.D., the salary range is as follows:
The salary for a PhD chemist depends on their work experience as well as the location and job that they apply for. For example, in Germany, scientists get salaries of 40,400 euros each year in small businesses. Salaries in large companies can reach up to 50,000 euros. However, scientists will typically be paid according to the collective wages agreements within the company.
The U.S. has a lot of chemists, and they make a great living. However, they also have responsibilities in education or research. University professors typically work on government-funded and private-industry-funded projects. Secondary school teachers can also find openings in the field. The American Chemical Society estimates that a chemist earning a bachelor's in chemistry earns $46,000 per year and a chemist earning a masters in chemistry earns $40,000 per year. A Ph.D. in Chemistry earned an average salary of $85,000 in 2011.
FAQ
How does a production planner differ from a project manager?
The major difference between a Production Planner and a Project Manager is that a Project Manager is often the person responsible for organizing and planning the entire project. While a Production Planner is involved mainly in the planning stage,
How can excess manufacturing production be reduced?
In order to reduce excess production, you need to develop better inventory management methods. This would decrease the time that is spent on inefficient activities like purchasing, storing, or maintaining excess stock. This will allow us to free up resources for more productive tasks.
Kanban systems are one way to achieve this. A Kanbanboard is a visual tool that allows you to keep track of the work being done. Kanban systems are where work items travel through a series of states until reaching their final destination. Each state represents an individual priority level.
For instance, when work moves from one stage to another, the current task is complete enough to be moved to the next stage. If a task is still in its beginning stages, it will continue to be so until it reaches the end.
This helps to keep work moving forward while ensuring that no work is left behind. A Kanban board allows managers to monitor how much work is being completed at any given moment. This allows them to adjust their workflows based on real-time information.
Lean manufacturing is another option to control inventory levels. Lean manufacturing focuses on eliminating waste throughout the entire production chain. Waste includes anything that does not add value to the product. Some common types of waste include:
-
Overproduction
-
Inventory
-
Packaging that is not necessary
-
Materials in excess
These ideas can help manufacturers improve efficiency and reduce costs.
What is production planning?
Production planning is the process of creating a plan that covers all aspects of production. This includes scheduling, budgeting and crew, location, equipment, props, and more. This document will ensure everything is in order and ready to go when you need it. This document should include information about how to achieve the best results on-set. This information includes locations, crew details and equipment requirements.
The first step in filming is to define what you want. You may have already decided where you would like to shoot, or maybe there are specific locations or sets that you want to use. Once you have identified your locations and scenes, you can start working out which elements you require for each scene. Perhaps you have decided that you need to buy a car but aren't sure which model. This is where you can look up car models online and narrow down your options by choosing from different makes and models.
Once you have found the right car, you can start thinking about extras. What about additional seating? Maybe you need someone to move around in the back. Maybe you'd like to change the interior from black to a white color. These questions will help you determine the exact look and feel of your car. The type of shots that you are looking for is another thing to consider. Do you want to film close-ups, or wider angles? Maybe you want to show your engine or the steering wheel. All of these things will help you identify the exact style of car you want to film.
Once you have all the information, you are ready to create a plan. You can create a schedule that will outline when you must start and finish your shoots. You will need to know when you have to be there, what time you have to leave and when your return home. It will help everyone know exactly what they have to do and when. It is possible to make arrangements in advance for additional staff if you are looking to hire. You don't want to hire someone who won't show up because he didn't know.
You will need to factor in the days that you have to film when creating your schedule. Some projects are quick and easy, while others take weeks. You should consider whether you will need more than one shot per week when creating your schedule. Shooting multiple takes over the same location will increase costs and take longer to complete. You can't be certain if you will need multiple takes so it is better not to shoot too many.
Budget setting is another important aspect in production planning. As it will allow you and your team to work within your financial means, setting a realistic budget is crucial. Keep in mind that you can always reduce your budget if you face unexpected difficulties. But, don't underestimate how much money you'll spend. If you underestimate how much something costs, you'll have less money to pay for other items.
Planning production is a tedious process. Once you have a good understanding of how everything works together, planning future projects becomes easy.
How can I find out more about manufacturing?
The best way to learn about manufacturing is through hands-on experience. You can also read educational videos or take classes if this isn't possible.
How can manufacturing prevent production bottlenecks?
You can avoid bottlenecks in production by making sure that everything runs smoothly throughout the production cycle, from the moment you receive an order to the moment the product is shipped.
This includes both quality control and capacity planning.
The best way to do this is to use continuous improvement techniques such as Six Sigma.
Six Sigma is a management method that helps to improve quality and reduce waste.
It's all about eliminating variation and creating consistency in work.
Statistics
- [54][55] These are the top 50 countries by the total value of manufacturing output in US dollars for its noted year according to World Bank.[56] (en.wikipedia.org)
- Job #1 is delivering the ordered product according to specifications: color, size, brand, and quantity. (netsuite.com)
- Many factories witnessed a 30% increase in output due to the shift to electric motors. (en.wikipedia.org)
- According to the United Nations Industrial Development Organization (UNIDO), China is the top manufacturer worldwide by 2019 output, producing 28.7% of the total global manufacturing output, followed by the United States, Japan, Germany, and India.[52][53] (en.wikipedia.org)
- (2:04) MTO is a production technique wherein products are customized according to customer specifications, and production only starts after an order is received. (oracle.com)
External Links
How To
How to Use Just-In-Time Production
Just-intime (JIT), which is a method to minimize costs and maximize efficiency in business process, is one way. This is where you have the right resources at the right time. This means that only what you use is charged to your account. The term was first coined by Frederick Taylor, who developed his theory while working as a foreman in the early 1900s. Taylor observed that overtime was paid to workers if they were late in working. He decided that workers would be more productive if they had enough time to complete their work before they started to work.
JIT is about planning ahead. You should have all the necessary resources ready to go so that you don’t waste money. Look at your entire project, from start to end. Make sure you have enough resources in place to deal with any unexpected problems. You'll be prepared to handle any potential problems if you know in advance. You won't have to pay more for unnecessary items.
There are many JIT methods.
-
Demand-driven: This type of JIT allows you to order the parts/materials required for your project on a regular basis. This will allow to track how much material has been used up. This will allow to you estimate the time it will take for more to be produced.
-
Inventory-based: This is a type where you stock the materials required for your projects in advance. This allows you to forecast how much you will sell.
-
Project-driven: This method allows you to set aside enough funds for your project. You will be able to purchase the right amount of materials if you know what you need.
-
Resource-based JIT : This is probably the most popular type of JIT. Here, you allocate certain resources based on demand. For instance, if you have a lot of orders coming in, you'll assign more people to handle them. If you don’t have many orders you will assign less people to the work.
-
Cost-based: This is similar to resource-based, except that here you're not just concerned about how many people you have but how much each person costs.
-
Price-based: This is a variant of cost-based. However, instead of focusing on the individual workers' costs, this looks at the total price of the company.
-
Material-based: This approach is similar to cost-based. However, instead of looking at the total cost for the company, you look at how much you spend on average on raw materials.
-
Time-based JIT is another form of resource-based JIT. Instead of worrying about how much each worker costs, you can focus on how long the project takes.
-
Quality-based JIT - This is another form of resource-based JIT. Instead of focusing on the cost of each worker or how long it takes, think about how high quality your product is.
-
Value-based: This is one of the newest forms of JIT. You don't worry about whether the products work or if they meet customer expectations. Instead, you are focused on adding value to the marketplace.
-
Stock-based is an inventory-based system that measures the number of items produced at any given moment. It's useful when you want maximum production and minimal inventory.
-
Just-in-time planning (JIT): This is a combination JIT and supply-chain management. It's the process of scheduling delivery of components immediately after they are ordered. It's important as it reduces leadtimes and increases throughput.