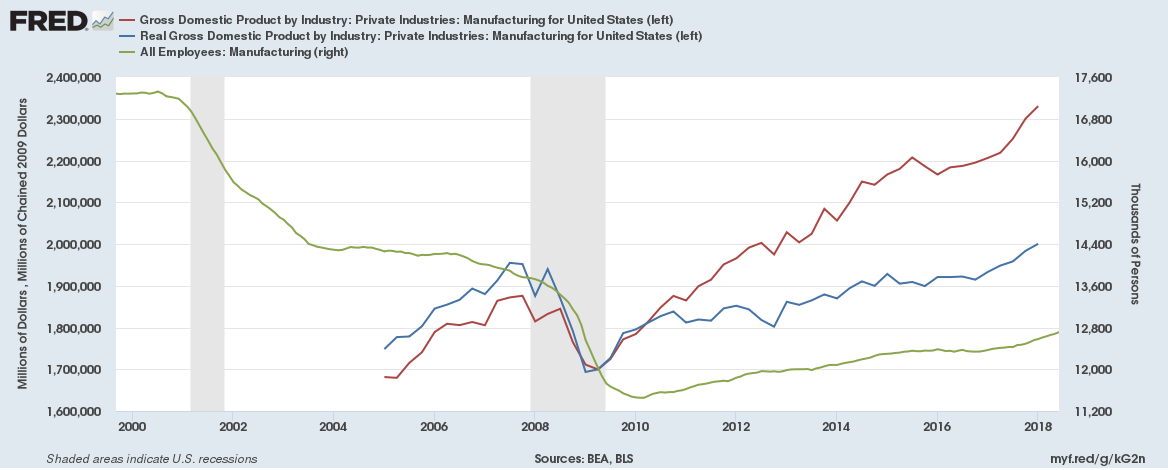
An industrial engineer uses his or her expertise to improve products and processes through engineering and testing. Industrial engineers use shake tables to test products at different temperatures, humidity, vibrations, and in product development. Failure data is collected and used to improve manufacturing processes and engineering. Simple changes, like mold-resistant paint, can greatly improve the quality and service life of a product. Even small changes like a lock-washed product placement can make a difference in a product's life expectancy.
Job description
It is important to carefully craft your job description if industrial engineers are something you want to pursue. A job description that is clear and concise will make you stand out from the rest. You can get some inspiration for a job description by checking out engineering job listings on Monster. Your introduction should include a compelling paragraph that highlights the company's advantages to applicants. Your employer must be attractive, regardless of whether you're interested in joining a global brand, an innovative startup, or an open-minded young company that fosters creativity and innovation.
Along with excellent technical skills and communication skills, industrial engineers should also be able to communicate well. Because industrial processes often involve several different departments and personnel, an industrial engineer must know how to work effectively with each of them. A successful industrial engineer must know how to persuade managers and employees that his orher proposed methods will increase efficiency. The best relationship management results in higher productivity. But it is not just technical skills that are important in an industrial engineer job description.
Education requirements
A degree in industrial engineering is required for a job that requires a lot of math and analysis skills. Because they will be communicating their findings to others in the future, industrial engineers need to have great communication skills. This is in addition to the ability to design and implement processes that will reduce labor costs and increase productivity. Education in this field will also enable you to succeed in this field. Here are some of the essential educational requirements for this position.
Industrial engineers need to have a college degree. They also need excellent interpersonal and communication skills. To effectively communicate with business leaders as well as employees, industrial engineers must have strong communication skills and analytical abilities. This profession requires excellent leadership and problem-solving skills. Additionally, industrial engineers should have excellent mechanical skills and technical knowledge.
There are many career options
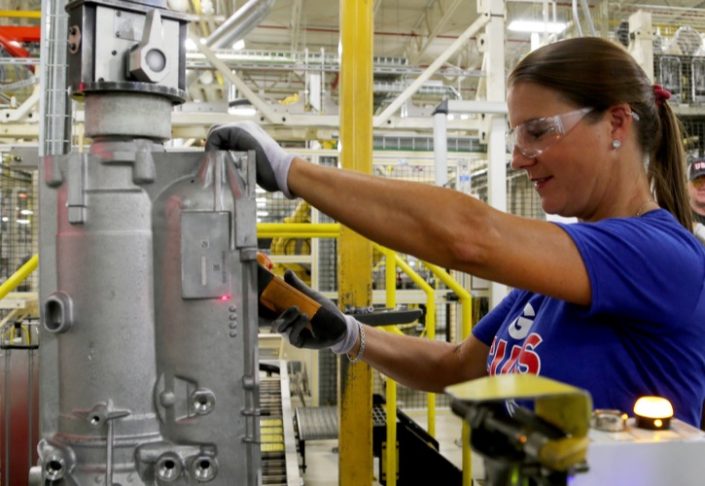
You have many career options if you are interested in industrial engineering. Although most industrial engineers start in manufacturing, other options include hospitals or government agencies. Other possible careers for industrial engineers include the food industry as well as retail trade, professional trade organizations, education agencies, and computer service centres. There are many different jobs that industrial engineers could be employed in, but here are some examples. Find out if this is the right profession for you.
An industrial engineer focuses on getting work done efficiently. Their job involves balancing many factors like time, availability of technology, worker safety, and workers' actions. They also have to consider worker safety and environmental issues. Many industrial engineers work in quality assurance or supply chain management. This is especially important as industries constantly look for ways to lower costs while increasing productivity. They can also help with product development and work flow optimization.
Salary
In 2004, the average salary for an Industrial Engineer was $87 513 USD. That figure is projected to rise to $114 146 by 2020. The salary depends on which industry you work in. Higher salaries are common in industries that are thriving. Industrial Engineers' bonus figures change regularly and are often modest. Most bonus recipients are involved in the revenue generation cycle. For this job to be considered for the highest salary, you will need to have an industrial engineering degree.
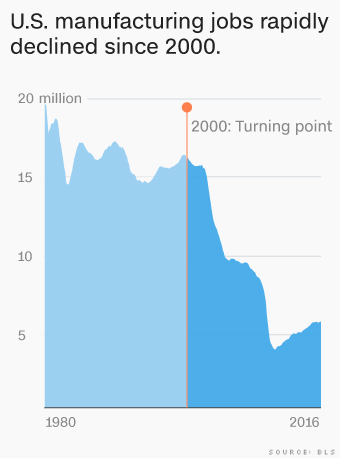
A bachelor's degree is required to be an industrial engineer. Some employers, however, prefer PhDs. In the U.S., an industrial engineer's salary ranges from $56,000 to $121,000, but that number can vary a great deal. While an industrial engineer can work in an office setting, many jobs require overtime and protective attire. You need to have a lot of flexibility.
FAQ
What does it take to run a logistics business?
To run a successful logistics company, you need a lot knowledge and skills. Good communication skills are essential to effectively communicate with your suppliers and clients. You will need to know how to interpret data and draw conclusions. You will need to be able handle pressure well and work in stressful situations. In order to innovate and create new ways to improve efficiency, creativity is essential. You will need strong leadership skills to motivate and direct your team members towards achieving their organizational goals.
It is important to be organized and efficient in order to meet tight deadlines.
What is the difference between manufacturing and logistics
Manufacturing is the process of creating goods from raw materials by using machines and processes. Logistics covers all aspects involved in managing supply chains, including procurement and production planning. As a broad term, manufacturing and logistics often refer to both the creation and delivery of products.
What kind of jobs are there in logistics?
Logistics can offer many different jobs. These are some of the jobs available in logistics:
-
Warehouse workers: They load and unload trucks, pallets, and other cargo.
-
Transportation drivers - They drive trucks and trailers to deliver goods and carry out pick-ups.
-
Freight handlers: They sort and package freight in warehouses.
-
Inventory managers – They manage the inventory in warehouses.
-
Sales reps - They sell products and services to customers.
-
Logistics coordinators - They organize and plan logistics operations.
-
Purchasing agents – They buy goods or services necessary to run a company.
-
Customer service representatives are available to answer customer calls and emails.
-
Ship clerks - They issue bills and process shipping orders.
-
Order fillers are people who fill orders based only on what was ordered.
-
Quality control inspectors - They check incoming and outgoing products for defects.
-
Others - There are many types of jobs in logistics such as transport supervisors and cargo specialists.
Statistics
- It's estimated that 10.8% of the U.S. GDP in 2020 was contributed to manufacturing. (investopedia.com)
- In the United States, for example, manufacturing makes up 15% of the economic output. (twi-global.com)
- You can multiply the result by 100 to get the total percent of monthly overhead. (investopedia.com)
- According to the United Nations Industrial Development Organization (UNIDO), China is the top manufacturer worldwide by 2019 output, producing 28.7% of the total global manufacturing output, followed by the United States, Japan, Germany, and India.[52][53] (en.wikipedia.org)
- According to a Statista study, U.S. businesses spent $1.63 trillion on logistics in 2019, moving goods from origin to end user through various supply chain network segments. (netsuite.com)
External Links
How To
How to Use Six Sigma in Manufacturing
Six Sigma is "the application statistical process control (SPC), techniques for continuous improvement." It was developed by Motorola's Quality Improvement Department at their plant in Tokyo, Japan, in 1986. Six Sigma's main goal is to improve process quality by standardizing processes and eliminating defects. Many companies have adopted this method in recent years. They believe there is no such thing a perfect product or service. Six Sigma seeks to reduce variation between the mean production value. It is possible to measure the performance of your product against an average and find the percentage of time that it differs from the norm. If this deviation is too big, you know something needs fixing.
Understanding how your business' variability is a key step towards Six Sigma implementation is the first. Once you understand that, it is time to identify the sources of variation. These variations can also be classified as random or systematic. Random variations are caused by human errors. Systematic variations can be caused by outside factors. If you make widgets and some of them end up on the assembly line, then those are considered random variations. If however, you notice that each time you assemble a widget it falls apart in exactly the same spot, that is a problem.
Once you've identified where the problems lie, you'll want to design solutions to eliminate those problems. It might mean changing the way you do business or redesigning it entirely. Test them again once you've implemented the changes. If they don't work, you will need to go back to the drawing boards and create a new plan.