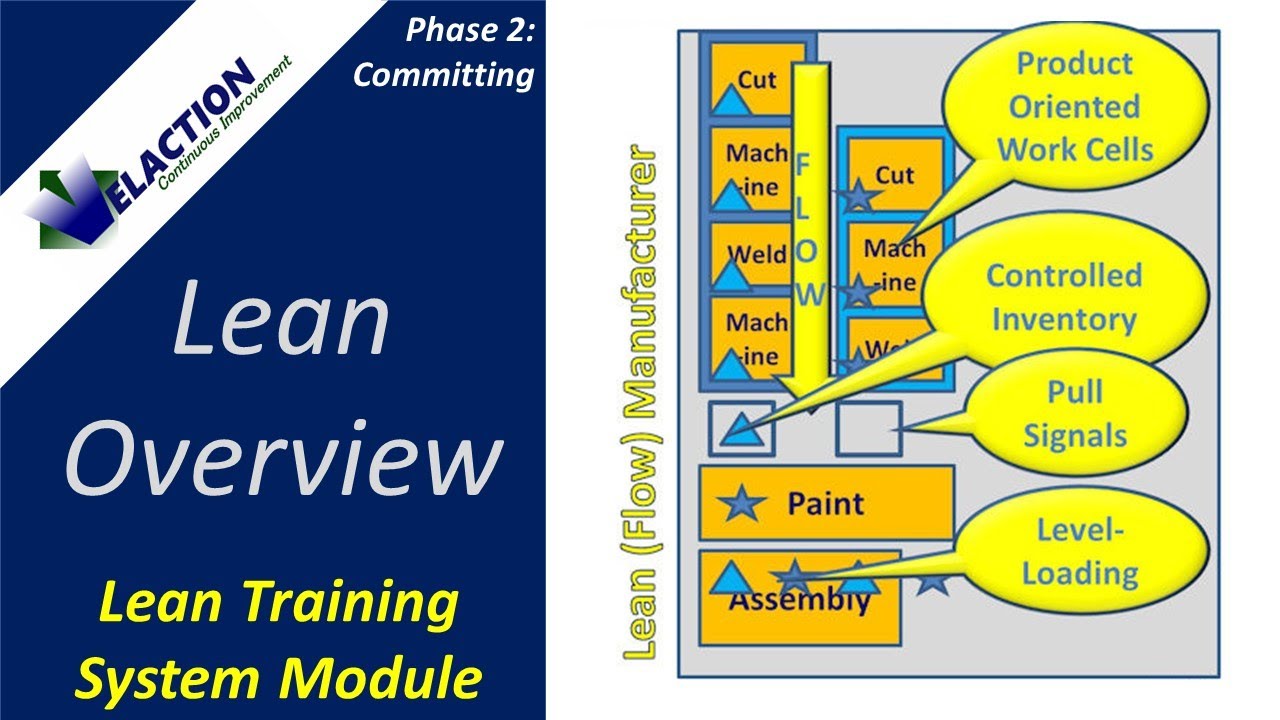
Amazon is seeking Supply Chain Managers who have a track record of success and senior leadership experience to manage strategic cross-functional operations. These roles will manage projects that support new products and operations, while working closely with business departments around the globe. They will develop cross-functional project teams and manage large-scale projects across multiple organizations.
Manager of purchasing and supply chains
Amazon Purchasing and Supply Chain managers are charged with a wide range of responsibilities. This includes driving cost savings, optimizing processes and mitigating risk. These responsibilities require strong communication skills and strong analytical and negotiation skills.
The ideal candidate for this position is a self-starter who has strong communication and attention to detail. She or he should also be able to work autonomously, meet tight deadlines, and manage her workload effectively.
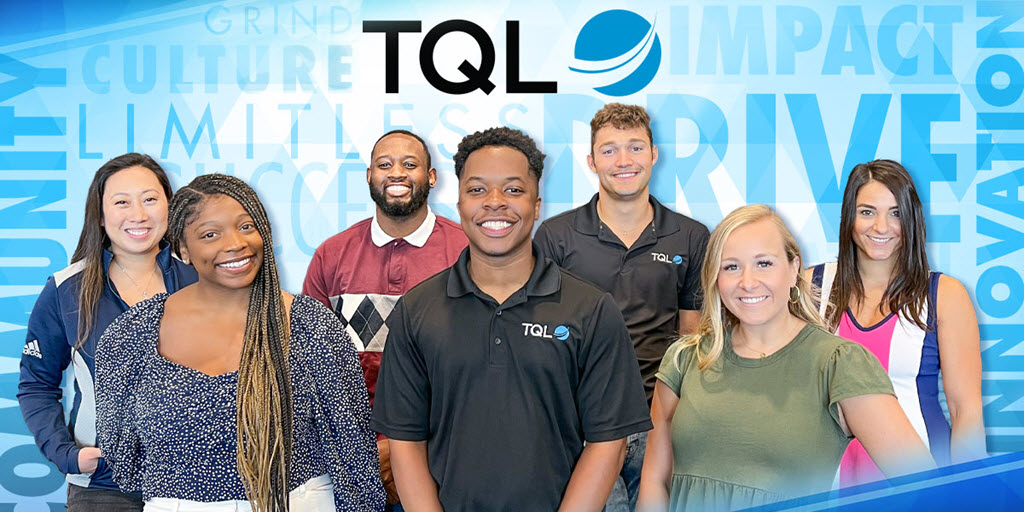
Cost analyst
Amazon's supply network is an integral component of its success. It includes all aspects of fulfillment and transportation as well as forecasting. It requires a highly analytical person with a passion for details. The data analyst will make sense the company's operations using data analytics. Global stakeholders will collaborate with the analyst to interpret data and draw conclusions. For their analysis they might use MS Excel or SQL.
Amazon's supply chains are some of the most innovative worldwide. Amazon invests in warehouse technology, trucking capabilities and many other areas. Amazon is also expanding its investments in drones, cargo planes, and other technologies.
Program manager
Amazon program manager supply chain jobs require extensive knowledge in areas such as supply chain planning, manufacturing and logistics. In addition, a successful applicant will be able to integrate across a team and make data-driven decisions. Additionally, the successful applicant will be required to manage and build systems and processes for quality control, scale, and risk management.
The salary of a Supply Chain Program Manager varies depending on where it is located. Some managers earn more than $168,000 annually, while others only earn $52,500. Program managers typically earn between $87500 and $127,000. But, the salary of Program managers can vary greatly depending on where they live and how much experience they have.
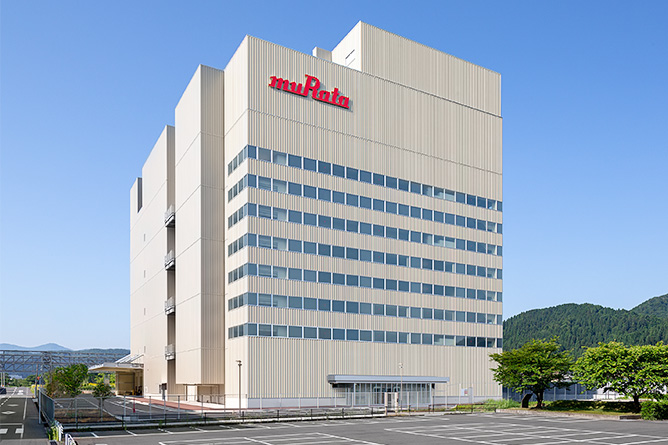
Warehouse manager
Warehouse management positions are in high demand and they are growing in demand. Although there is no requirement for a warehouse manager to have a degree, employers will prefer someone with some experience. You do not need a bachelor's to be able to apply for this position. However, it will help increase your chances of being hired.
Warehouse managers have a broad range of tasks to perform, including inventory management and customer service. They also have a huge impact on the experience for shippers and operators. These people manage the performance of the entire supply chains and devise strategies to improve efficiency. Additionally, they can work with multiple Amazon teams and gain broad exposure to their operations.
FAQ
What does manufacturing industry mean?
Manufacturing Industries are companies that manufacture products. Consumers are people who purchase these goods. This is accomplished by using a variety of processes, including production, distribution and retailing. They create goods from raw materials, using machines and various other equipment. This includes all types manufactured goods such as clothing, building materials, furniture, electronics, tools and machinery.
What skills should a production planner have?
Production planners must be flexible, organized, and able handle multiple tasks. Effective communication with clients and colleagues is essential.
What is the role and responsibility of a Production Planner?
A production planner makes sure all project elements are delivered on schedule, within budget, as well as within the agreed scope. They make sure that the product and services meet client expectations.
Why is logistics important in manufacturing
Logistics are an integral part any business. They enable you to achieve outstanding results by helping manage product flow from raw materials through to finished goods.
Logistics also play a major role in reducing costs and increasing efficiency.
What can I do to learn more about manufacturing?
The best way to learn about manufacturing is through hands-on experience. However, if that's not possible, you can always read books or watch educational videos.
What are the 7 R's of logistics?
The 7R's of Logistics is an acronym for the seven basic principles of logistics management. It was developed and published by the International Association of Business Logisticians in 2004 as part of the "Seven Principles of Logistics Management".
The following letters make up the acronym:
-
Responsible – ensure that all actions are legal and don't cause harm to anyone else.
-
Reliable: Have faith in your ability or the ability to honor any promises made.
-
Reasonable - use resources efficiently and don't waste them.
-
Realistic – Consider all aspects, including cost-effectiveness as well as environmental impact.
-
Respectful: Treat others with fairness and equity
-
Responsive - Look for ways to save time and increase productivity.
-
Recognizable provides value-added products and services to customers
What kind of jobs are there in logistics?
There are many types of jobs in logistics. These are some of the jobs available in logistics:
-
Warehouse workers – They load and unload pallets and trucks.
-
Transportation drivers - They drive trucks and trailers to deliver goods and carry out pick-ups.
-
Freight handlers - They sort and pack freight in warehouses.
-
Inventory managers – They manage the inventory in warehouses.
-
Sales reps - They sell products and services to customers.
-
Logistics coordinators – They plan and coordinate logistics operations.
-
Purchasing agents - They buy goods and services that are necessary for company operations.
-
Customer service representatives - They answer calls and emails from customers.
-
Shipping clerks - They process shipping orders and issue bills.
-
Order fillers: They fill orders based off what has been ordered and shipped.
-
Quality control inspectors (QCI) - They inspect all incoming and departing products for potential defects.
-
Others - There is a variety of other jobs in logistics. These include transportation supervisors and cargo specialists.
Statistics
- According to a Statista study, U.S. businesses spent $1.63 trillion on logistics in 2019, moving goods from origin to end user through various supply chain network segments. (netsuite.com)
- In the United States, for example, manufacturing makes up 15% of the economic output. (twi-global.com)
- You can multiply the result by 100 to get the total percent of monthly overhead. (investopedia.com)
- Job #1 is delivering the ordered product according to specifications: color, size, brand, and quantity. (netsuite.com)
- In 2021, an estimated 12.1 million Americans work in the manufacturing sector.6 (investopedia.com)
External Links
How To
How to Use Just-In-Time Production
Just-intime (JIT), which is a method to minimize costs and maximize efficiency in business process, is one way. It's a way to ensure that you get the right resources at just the right time. This means that only what you use is charged to your account. Frederick Taylor developed the concept while working as foreman in early 1900s. He saw how overtime was paid to workers for work that was delayed. He decided that workers would be more productive if they had enough time to complete their work before they started to work.
JIT is a way to plan ahead and make sure you don't waste any money. Also, you should look at the whole project from start-to-finish and make sure you have the resources necessary to address any issues. If you anticipate that there might be problems, you'll have enough people and equipment to fix them. This way, you won't end up paying extra money for things that weren't really necessary.
There are several types of JIT techniques:
-
Demand-driven JIT: This is a JIT that allows you to regularly order the parts/materials necessary for your project. This will allow for you to track the material that you have left after using it. This will allow you to calculate how long it will take to make more.
-
Inventory-based: This type allows you to stock the materials needed for your projects ahead of time. This allows you to forecast how much you will sell.
-
Project-driven : This is a method where you make sure that enough money is set aside to pay the project's cost. You will be able to purchase the right amount of materials if you know what you need.
-
Resource-based JIT: This is the most popular form of JIT. You allocate resources based on the demand. You will, for example, assign more staff to deal with large orders. If there aren't many orders, you will assign fewer people.
-
Cost-based: This is the same as resource-based except that you don't care how many people there are but how much each one of them costs.
-
Price-based: This is very similar to cost-based, except that instead of looking at how much each individual worker costs, you look at the overall price of the company.
-
Material-based is an alternative to cost-based. Instead of looking at the total cost in the company, this method focuses on the average amount of raw materials that you consume.
-
Time-based JIT is another form of resource-based JIT. Instead of focusing on how much each employee costs, you focus on how long it takes to complete the project.
-
Quality-based: This is yet another variation of resource-based JIT. Instead of focusing on the cost of each worker or how long it takes, think about how high quality your product is.
-
Value-based JIT: This is the latest form of JIT. This is where you don't care about how the products perform or whether they meet customers' expectations. Instead, you're focused on how much value you add to the market.
-
Stock-based: This stock-based method focuses on the actual quantity of products being made at any given time. This method is useful when you want to increase production while decreasing inventory.
-
Just-intime planning (JIT), is a combination JIT/sales chain management. It is the process that schedules the delivery of components within a short time of their order. It's important because it reduces lead times and increases throughput.