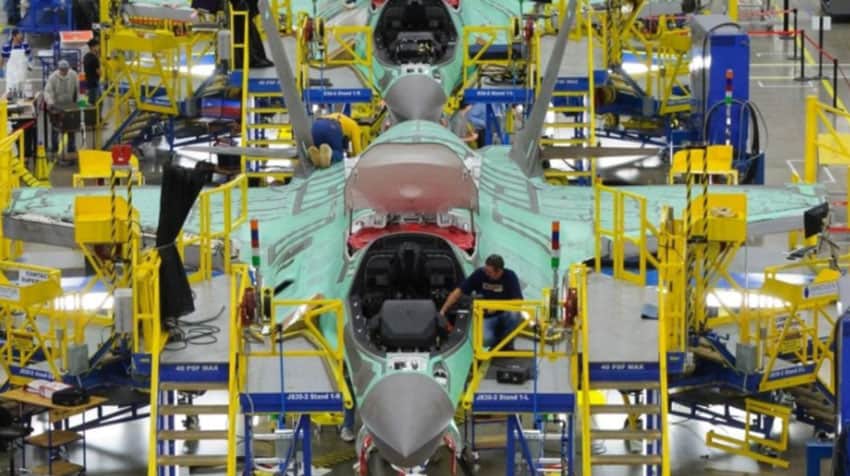
Non value added activities are actions that don't add value to the finished product. While it may be useful or necessary, it does not directly increase the product's value. To cut lumber to the correct size, you need to sharpen the saw. However, sharpening the saw does not enhance the value of the finished product.
To understand non value added activities, you must first define what value is. Value is what customers pay for a product, or service. It can vary depending on what type of service or product is being offered. A business' success depends on its ability to add value. It is not possible for a business to succeed if it does not offer value through its products and services. A business can also lose customers.
When determining whether an action is a value-added activity, ask yourself, "Does the action add value to the product or service?" There are three possible answers. First, consider the relationship between the action and the final product's value. You can also evaluate the impact of the action on customer satisfaction. Finally, there is the question, "Does the action contribute to the overall customer experience?"
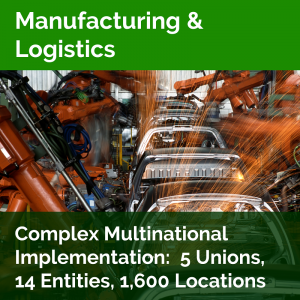
A value-added activity can be defined as one that produces a positive return. Selling merchandise, for instance, is a valuable activity. Selling merchandise is a valuable activity because it gives a company a profit. It also helps companies recover the manufacturing costs, making it a worthwhile business activity.
Although it is important that you identify a value-added business activity, this does not guarantee its success. The process that produces the value-added activity must be designed to meet customer expectations. The best process will ensure that products or services are delivered on time and with high quality. The wrong process can lead to delays and quality problems.
In order to identify a value-added activity, you must understand what a non-valued activity is. Non-valued activities are tasks that do not change the form or function of the product or service. Examples of non-valued activities include checking, inspecting, processing, and billing.
Activities that are not valued by customers or contribute to customer satisfaction are called non-valued. They can also be costly and consume resources. By identifying and eliminating wastes from your process, you can increase speed, quality, as well as service levels. Your cash flow and competitiveness will improve if you take steps to eliminate the waste.
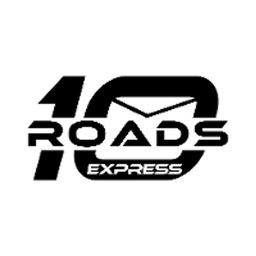
It is easy to waste your time doing non-value-added activities. You can waste your time on activities that are not valuable, such as waiting or performing inspections. Moving raw materials, copying documents and filing paperwork are all activities that add no value to the finished product.
A list of processes that add to the product or service can help you determine if your current process has potential to maximize your potential. You can save time, money and resources by breaking down the process.
FAQ
How can I find out more about manufacturing?
You can learn the most about manufacturing by getting involved in it. You can also read educational videos or take classes if this isn't possible.
What is the job of a logistics manger?
Logistics managers make sure all goods are delivered on schedule and without damage. This is accomplished by using the experience and knowledge gained from working with company products. He/she also needs to ensure adequate stock to meet demand.
What is the difference between Production Planning and Scheduling?
Production Planning (PP), also known as forecasting and identifying production capacities, is the process that determines what product needs to be produced at any particular time. This is done through forecasting demand and identifying production capacities.
Scheduling refers to the process of allocating specific dates to tasks in order that they can be completed within a specified timeframe.
What are the main products of logistics?
Logistics involves the transportation of goods from point A and point B.
They include all aspects of transport, including packaging, loading, transporting, unloading, storing, warehousing, inventory management, customer service, distribution, returns, and recycling.
Logisticians ensure that products reach the right destination at the right moment and under safe conditions. They help companies manage their supply chain efficiency by providing information on demand forecasts, stock levels, production schedules, and availability of raw materials.
They keep track and monitor the transit of shipments, maintain quality standards, order replenishment and inventories, coordinate with suppliers, vendors, and provide support for sales and marketing.
What are the responsibilities of a production planner
Production planners ensure that all project aspects are completed on time, within budget and within the scope. A production planner ensures that the service and product meet the client's expectations.
Statistics
- In the United States, for example, manufacturing makes up 15% of the economic output. (twi-global.com)
- Many factories witnessed a 30% increase in output due to the shift to electric motors. (en.wikipedia.org)
- [54][55] These are the top 50 countries by the total value of manufacturing output in US dollars for its noted year according to World Bank.[56] (en.wikipedia.org)
- Job #1 is delivering the ordered product according to specifications: color, size, brand, and quantity. (netsuite.com)
- According to the United Nations Industrial Development Organization (UNIDO), China is the top manufacturer worldwide by 2019 output, producing 28.7% of the total global manufacturing output, followed by the United States, Japan, Germany, and India.[52][53] (en.wikipedia.org)
External Links
How To
How to Use Lean Manufacturing for the Production of Goods
Lean manufacturing is a management system that aims at increasing efficiency and reducing waste. It was developed in Japan between 1970 and 1980 by Taiichi Ohno. TPS founder Kanji Tyoda gave him the Toyota Production System, or TPS award. The first book published on lean manufacturing was titled "The Machine That Changed the World" written by Michael L. Watkins and published in 1990.
Lean manufacturing refers to a set of principles that improve the quality, speed and costs of products and services. It emphasizes eliminating waste and defects throughout the value stream. Lean manufacturing is called just-in-time (JIT), zero defect, total productive maintenance (TPM), or 5S. Lean manufacturing is about eliminating activities that do not add value, such as inspection, rework, and waiting.
Lean manufacturing improves product quality and costs. It also helps companies reach their goals quicker and decreases employee turnover. Lean Manufacturing is one of the most efficient ways to manage the entire value chains, including suppliers and customers as well distributors and retailers. Lean manufacturing is widely practiced in many industries around the world. Toyota's philosophy has been a key driver of success in many industries, including automobiles and electronics.
Five basic principles of Lean Manufacturing are included in lean manufacturing
-
Define Value: Identify the social value of your business and what sets you apart.
-
Reduce Waste – Eliminate all activities that don't add value throughout the supply chain.
-
Create Flow - Ensure work moves smoothly through the process without interruption.
-
Standardize and simplify - Make your processes as consistent as possible.
-
Develop Relationships: Establish personal relationships both with internal and external stakeholders.
Lean manufacturing, although not new, has seen renewed interest in the economic sector since 2008. Many companies have adopted lean manufacturing methods to increase their marketability. According to some economists, lean manufacturing could be a significant factor in the economic recovery.
Lean manufacturing, which has many benefits, is now a standard practice in the automotive industry. These include higher customer satisfaction levels, reduced inventory levels as well as lower operating costs.
Any aspect of an enterprise can benefit from Lean manufacturing. Because it makes sure that all value chains are efficient and effectively managed, Lean Manufacturing is particularly helpful for organizations.
There are three main types in lean manufacturing
-
Just-in Time Manufacturing (JIT), also known as "pull system": This form of lean manufacturing is often referred to simply as "pull". JIT is a method in which components are assembled right at the moment of use, rather than being manufactured ahead of time. This approach aims to reduce lead times, increase the availability of parts, and reduce inventory.
-
Zero Defects Manufacturing (ZDM),: ZDM is a system that ensures no defective units are left the manufacturing facility. You should repair any part that needs to be repaired during an assembly line. This applies to finished goods that may require minor repairs before shipment.
-
Continuous Improvement (CI: Continuous improvement aims to increase the efficiency of operations by constantly identifying and making improvements to reduce or eliminate waste. It involves continuous improvement of processes, people, and tools.