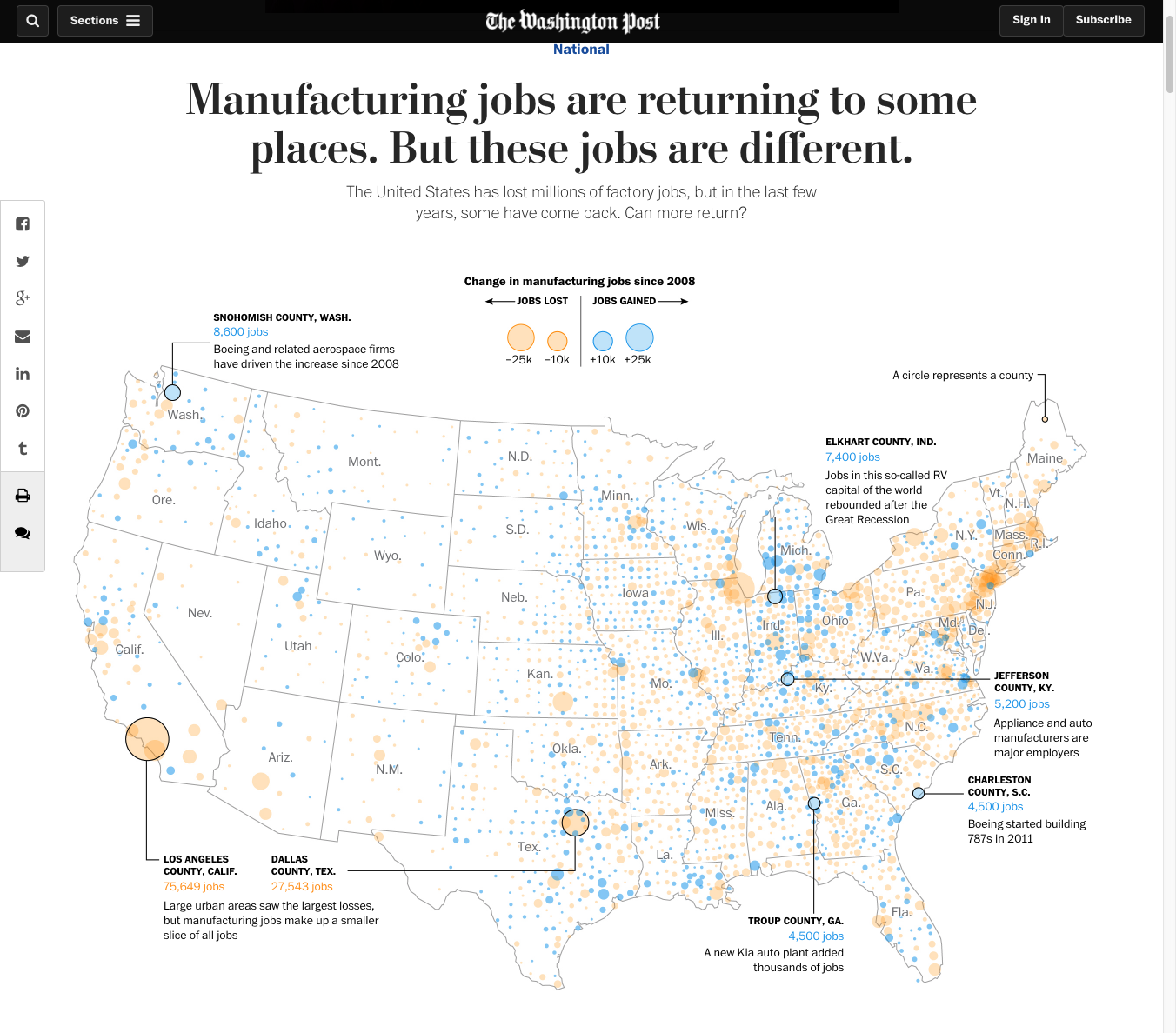
Technicians are responsible for the maintenance and analysis of various equipment and machines involved in testing and producing nuclear energy. A nuclear technician usually works for a nuclear power plant and can advance to higher levels of responsibility as they gain experience. They can conduct radiation tests, troubleshoot and collect data to help determine the quality of a system.
An associate's/bachelor's in nuclear technology is necessary to be a qualified nuclear technician. In addition, you'll need to complete training. Most employers require two years of specialized training to qualify for a nuclear technician job. Upon completion, you can apply for nuclear technician positions with a power plant, laboratory, or other organization. You can also study nuclear waste management to become a certified nuclear engineer.
A nuclear technician typically works with scientists in nuclear energy research or production. They may also monitor or record radiation levels in reactors. A nuclear technician may also operate specialized equipment such as remote-control panels. They can also instruct staff about radiation safety procedures.
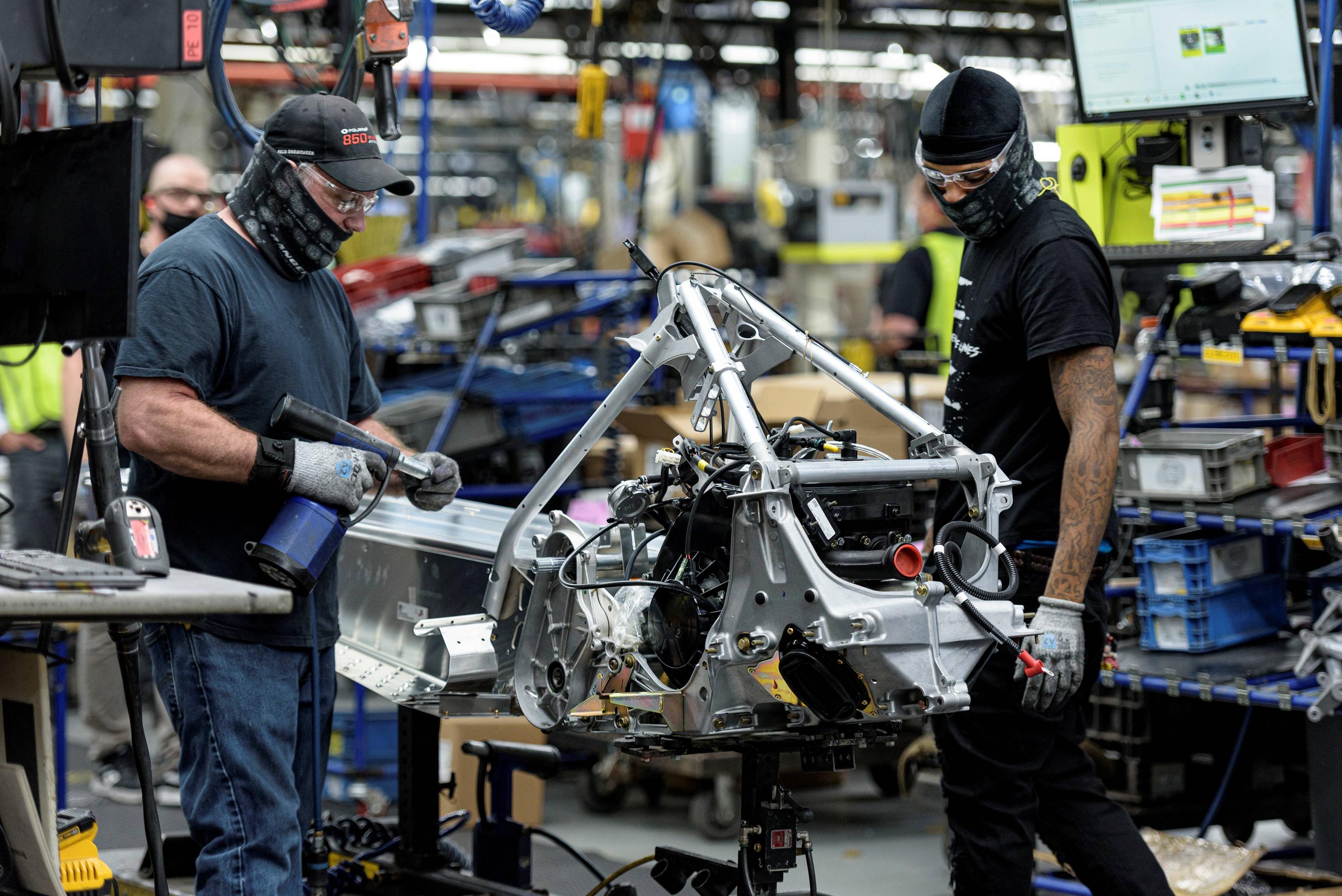
Nuclear technicians can specialize in radio protection, waste management or nuclear engineering. Nuclear technicians can work on restricted projects that require security clearance, advanced math and science courses.
Government agencies may also consider nuclear technicians. These jobs typically involve working with ideas, searching for facts, and mentally delving into complicated situations. The average hourly salary for a nuclear technician may be $38,10, but this is not the case.
You can also become a technician, a supervisor, an instructor, or a nuclear engineer. Higher levels of responsibility may allow them to earn higher salaries. This is a career that can offer good pay in many fields.
According to your level of education or experience, the salary for nuclear technicians can vary. You can expect to earn $31,000 an year as an entry-level technician. On the other hand, nuclear technicians who have been with an organization for many years may earn a salary of $115,500 per year. This field is expected grow at a rapid rate over the next ten years. This field should have approximately 1,400 job openings.
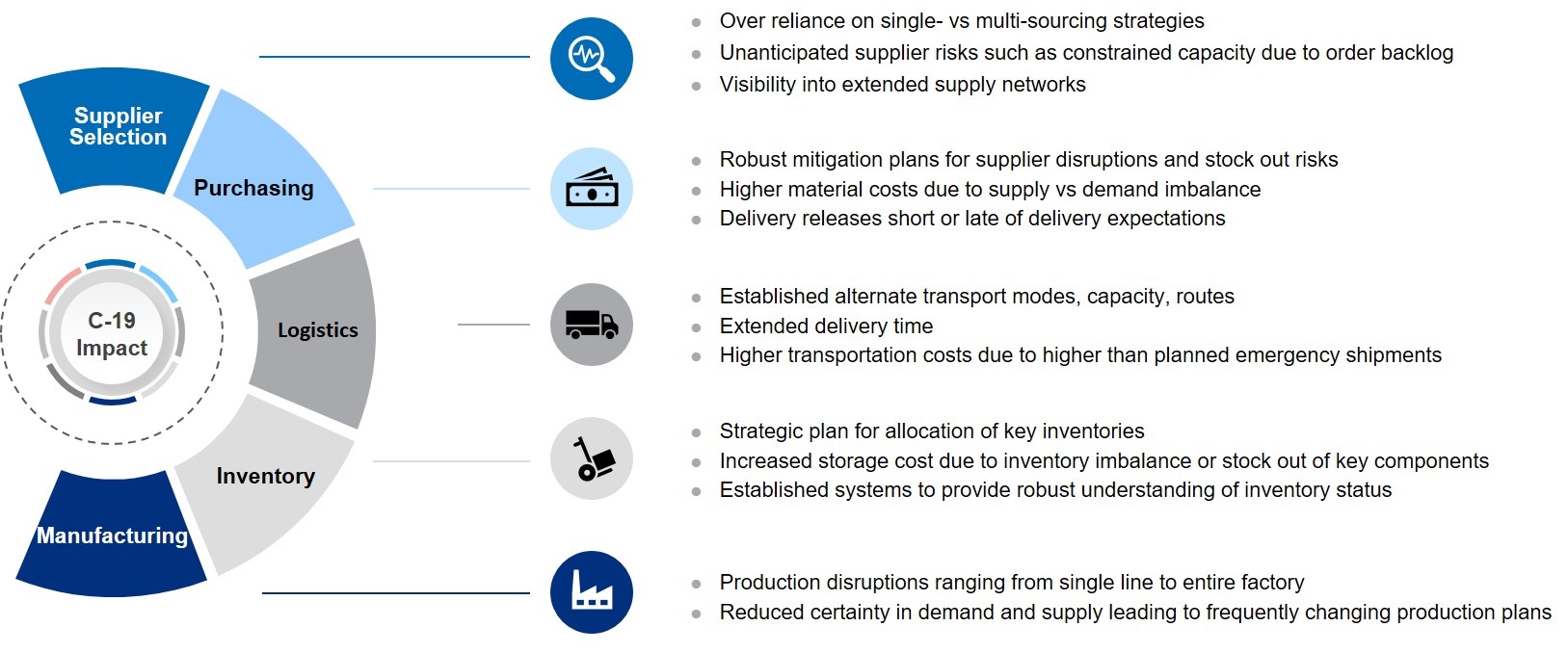
There may be a wide range of salaries for nuclear technicians. For instance, the average Illinois salary is $121,020 annually. California has the highest average salary for a Nuclear Technician. Although it can vary from state-to-state, the national average is $126,000. Higher salaries might be offered to those who hold advanced degrees or have a degree as a nuclear technician.
Although the salary for a Nuclear Technician is high, this does not necessarily mean that it is the most lucrative. A passion for science and the ability think critically are essential. Also, you'll need to know how to operate specialized machinery. Many nuclear technicians pursue further education to obtain certifications in this field.
FAQ
What do we need to know about Manufacturing Processes in order to learn more about Logistics?
No. You don't have to know about manufacturing processes before learning about logistics. But, being familiar with manufacturing processes will give you a better understanding about how logistics works.
Why should you automate your warehouse?
Modern warehouses are increasingly dependent on automation. Increased demand for efficient and faster delivery has resulted in a rise in e-commerce.
Warehouses must adapt quickly to meet changing customer needs. Technology is essential for warehouses to be able to adapt quickly to changing needs. Automating warehouses is a great way to save money. These are some of the benefits that automation can bring to warehouses:
-
Increases throughput/productivity
-
Reduces errors
-
Increases accuracy
-
Safety enhancements
-
Eliminates bottlenecks
-
Allows companies to scale more easily
-
It makes workers more efficient
-
Provides visibility into everything that happens in the warehouse
-
Enhances customer experience
-
Improves employee satisfaction
-
Minimizes downtime and increases uptime
-
High quality products delivered on-time
-
Human error can be eliminated
-
Helps ensure compliance with regulations
What does manufacturing industry mean?
Manufacturing Industries are those businesses that make products for sale. Consumers are the people who purchase these products. To accomplish this goal, these companies employ a range of processes including distribution, sales, management, and production. They make goods from raw materials with machines and other equipment. This includes all types manufactured goods such as clothing, building materials, furniture, electronics, tools and machinery.
Can some manufacturing processes be automated?
Yes! Since ancient times, automation has been in existence. The Egyptians invent the wheel thousands of year ago. Robots are now used to assist us in assembly lines.
Actually, robotics can be used in manufacturing for many purposes. These include:
-
Robots for assembly line
-
Robot welding
-
Robot painting
-
Robotics inspection
-
Robots that create products
Manufacturing could also benefit from automation in other ways. 3D printing makes it possible to produce custom products in a matter of days or weeks.
What is the role and responsibility of a Production Planner?
A production planner makes sure all project elements are delivered on schedule, within budget, as well as within the agreed scope. They make sure that the product and services meet client expectations.
How can I find out more about manufacturing?
Hands-on experience is the best way to learn more about manufacturing. If that is not possible, you could always read books or view educational videos.
How can manufacturing reduce production bottlenecks?
The key to avoiding bottlenecks in production is to keep all processes running smoothly throughout the entire production cycle, from the time you receive an order until the time when the product ships.
This includes planning for capacity requirements as well as quality control measures.
This can be done by using continuous improvement techniques, such as Six Sigma.
Six Sigma is a management method that helps to improve quality and reduce waste.
It seeks to eliminate variation and create consistency in your work.
Statistics
- In 2021, an estimated 12.1 million Americans work in the manufacturing sector.6 (investopedia.com)
- According to a Statista study, U.S. businesses spent $1.63 trillion on logistics in 2019, moving goods from origin to end user through various supply chain network segments. (netsuite.com)
- (2:04) MTO is a production technique wherein products are customized according to customer specifications, and production only starts after an order is received. (oracle.com)
- Many factories witnessed a 30% increase in output due to the shift to electric motors. (en.wikipedia.org)
- It's estimated that 10.8% of the U.S. GDP in 2020 was contributed to manufacturing. (investopedia.com)
External Links
How To
How to use 5S in Manufacturing to Increase Productivity
5S stands as "Sort", Set In Order", Standardize", Separate" and "Store". Toyota Motor Corporation created the 5S methodology in 1954. It allows companies to improve their work environment, thereby achieving greater efficiency.
This method aims to standardize production processes so that they are repeatable, measurable and predictable. This means that tasks such as cleaning, sorting, storing, packing, and labeling are performed daily. Because workers know what they can expect, this helps them perform their jobs more efficiently.
There are five steps to implementing 5S, including Sort, Set In Order, Standardize, Separate and Store. Each step requires a different action to increase efficiency. By sorting, for example, you make it easy to find the items later. You arrange items by placing them in an order. Once you have separated your inventory into groups and organized them, you will store these groups in easily accessible containers. You can also label your containers to ensure everything is properly labeled.
Employees need to reflect on how they do their jobs. Employees must be able to see why they do what they do and find a way to achieve them without having to rely on their old methods. They must learn new skills and techniques in order to implement the 5S system.
In addition to improving efficiency, the 5S system also increases morale and teamwork among employees. They feel more motivated to work towards achieving greater efficiency as they see the results.