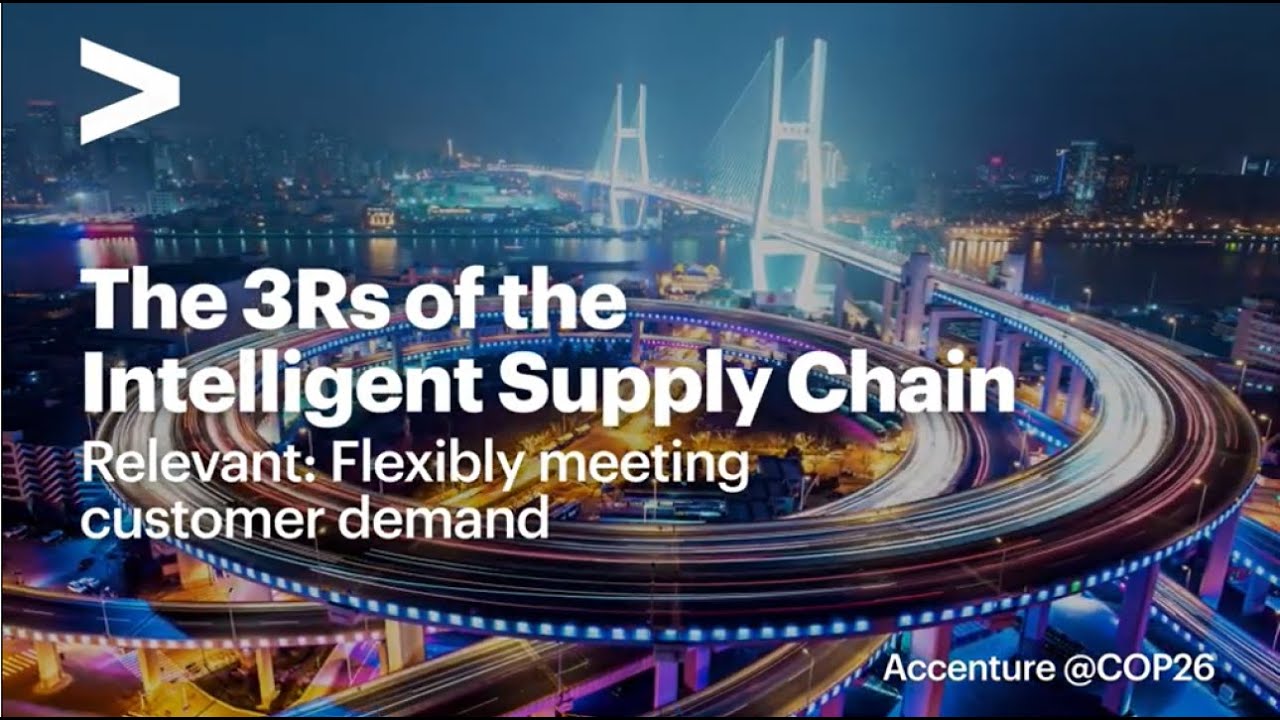
OSHA compliance and experience are equally important for food manufacturers. When choosing a company who will automate your production, there are three important things to remember:
Food manufacturers need to have experience
A high level of industry experience is often required for a position in a food manufacturer. There are still opportunities for those who have no experience. Many food producers prefer to hire within their own ranks. It is important to have a high school diploma, but it is not required. As assistants to more skilled workers, entry-level employees begin as such. Then, they learn on the job. Some entry-level tasks are easy and can be completed in as little as a couple of days. You may find entry-level work in common areas such as operating bread slicers or washing vegetables before they are processed, transporting carcasses and packaging bottles as they leave the production line. Food manufacturing requires a lot of experience.
Conformance to OSHA regulations
OSHA regulations for food manufacturing companies are enforced with an inspection. The inspection can be either initiated by an incident, complaint, and/or a "programmed inspection". OSHA enforcement visits at yogurt manufacturing plants are usually triggered by a report and preceded with a planned inspector. In many cases, the citations include multiple violations of the process safety management standard, as well as standards on hazard communication, guarding machinery, stairs and platforms, emergency egress, forklift operation, hearing protection, and more.
Develop a plan that will prevent food safety hazards
While federal regulations govern most companies, some businesses are exempt from certain requirements. While it's impossible to foresee every potential food safety issue, there is a way to reduce and manage the risks in food manufacturing. Food safety can have serious consequences for businesses as well as the health of consumers. Recalls can have a negative impact on both direct operations as well as other members of the supply chain. Recalls can occur for many reasons including adulteration (misbranding) or violation of products. A food manufacturer can face costly recalls if they have to recall food due to health concerns.
Automation costs
As utilities costs rise, automation is becoming more expensive for food manufacturers. Therefore, some regions have to import raw materials to keep up with local producers. Suppliers face declining profits as they pass the costs on to consumers. However, automation can help lower these costs and increase production efficiency. This article will explain how automation can improve food manufacturing's overall efficiency. You can also access our expertise in the industry.
Competing with established food companies presents challenges
To maintain their market dominance and prevent unwelcome competition, dominant food companies employ three strategies. The strategies are about acquiring and developing valuable assets, as well as enforcing marketing and production efficiencies and controlling the supply chains. In essence, these strategies create barriers to entry. These are the top challenges for emerging food and beverage businesses. Let's take a closer look at each strategy.
FAQ
What is the job of a production plan?
A production planner ensures all aspects of the project are delivered on time, within budget, and within scope. They also ensure that the product/service meets the client’s needs.
Can some manufacturing processes be automated?
Yes! Yes. Automation has been around since ancient time. The Egyptians invented the wheel thousands of years ago. Nowadays, we use robots for assembly lines.
There are many uses of robotics today in manufacturing. These include:
-
Assembly line robots
-
Robot welding
-
Robot painting
-
Robotics inspection
-
Robots that make products
Manufacturing can also be automated in many other ways. 3D printing, for example, allows us to create custom products without waiting for them to be made.
How can manufacturing excess production be decreased?
The key to reducing overproduction lies in developing better ways to manage inventory. This would decrease the time that is spent on inefficient activities like purchasing, storing, or maintaining excess stock. This will allow us to free up resources for more productive tasks.
One way to do this is to adopt a Kanban system. A Kanbanboard is a visual tool that allows you to keep track of the work being done. In a Kanban system, work items move through a sequence of states until they reach their final destination. Each state represents an individual priority level.
If work is moving from one stage to the other, then the current task can be completed and moved on to the next. However, if a task is still at the beginning stages, it will remain so until it reaches the end of the process.
This allows work to move forward and ensures that no work is missed. Managers can see how much work has been done and the status of each task at any time with a Kanban Board. This information allows managers to adjust their workflow based off real-time data.
Lean manufacturing is another way to manage inventory levels. Lean manufacturing emphasizes eliminating waste in all phases of production. Any product that isn't adding value can be considered waste. There are several types of waste that you might encounter:
-
Overproduction
-
Inventory
-
Packaging that is not necessary
-
Materials in excess
By implementing these ideas, manufacturers can improve efficiency and cut costs.
Statistics
- According to the United Nations Industrial Development Organization (UNIDO), China is the top manufacturer worldwide by 2019 output, producing 28.7% of the total global manufacturing output, followed by the United States, Japan, Germany, and India.[52][53] (en.wikipedia.org)
- According to a Statista study, U.S. businesses spent $1.63 trillion on logistics in 2019, moving goods from origin to end user through various supply chain network segments. (netsuite.com)
- It's estimated that 10.8% of the U.S. GDP in 2020 was contributed to manufacturing. (investopedia.com)
- In the United States, for example, manufacturing makes up 15% of the economic output. (twi-global.com)
- Job #1 is delivering the ordered product according to specifications: color, size, brand, and quantity. (netsuite.com)
External Links
How To
How to Use 5S to Increase Productivity in Manufacturing
5S stands to stand for "Sort", “Set In Order", “Standardize", and "Store". Toyota Motor Corporation developed the 5S method in 1954. It assists companies in improving their work environments and achieving higher efficiency.
This method has the basic goal of standardizing production processes to make them repeatable. This means that every day tasks such cleaning, sorting/storing, packing, and labeling can be performed. This knowledge allows workers to be more efficient in their work because they are aware of what to expect.
Five steps are required to implement 5S: Sort, Set In Order, Standardize. Separate. Each step requires a different action, which increases efficiency. If you sort items, it makes them easier to find later. You arrange items by placing them in an order. After you have divided your inventory into groups you can store them in easy-to-reach containers. Finally, when you label your containers, you ensure everything is labeled correctly.
This process requires employees to think critically about how they do their job. Employees must be able to see why they do what they do and find a way to achieve them without having to rely on their old methods. In order to use the 5S system effectively, they must be able to learn new skills.
The 5S method increases efficiency and morale among employees. As they begin to see improvements, they feel motivated to continue working towards the goal of achieving higher levels of efficiency.