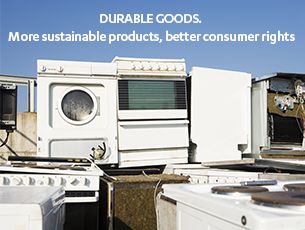
The Industrial Products & Services segment of the industrial manufacturing business is seeing increased global competition. It also faces a shortage for skilled workers. Combined with increased supply chain volatility, the industrial manufacturing industry faces a challenging landscape in the 2020s. The Industrial Products & Services sector requires a comprehensive culture of innovation to ensure optimisation of growth in established markets, while also optimising for growth opportunities in new markets.
According to a Deloitte and Manufacturing Institute report, the US manufacturing industry will face the largest shortage of skilled workers in its history. Over the next decade, 2 million jobs will remain vacant. As the industry prepares to face the future, manufacturers will need to decide how they will innovate and develop their digital capabilities. The Industrial Manufacturing team from Deloitte can help manufacturers navigate the industry landscape.
The fourth industrial revolution is continuing to disrupt the manufacturing industry. Industry must prepare workers for a future that involves networking within the "internet of things" and digital transformation. The Industrial Manufacturing team is experienced in establishing innovation management models that are grounded in industry-specific expertise and deep knowledge of the industry. It also provides a wide range of digital transformation services that can help manufacturers to thrive in a world of digital disruption.
The Deloitte research is based on extensive secondary analysis of labor supply and interviews with executives of manufacturing companies of all sizes. Economic projections are also included in the research. Findings also emphasize the importance of diverse workforces. Half of respondents identified adaptability to company values being a key aspect of their job satisfaction. Over a third of respondents said that employees need to have a purpose to feel satisfied at their jobs. Additionally, executives think that millennials recognize the importance environmental awareness. They also believe that Generation Z workers have a greater interest in climate issues.
Deloitte's Oxford Economic Model predicts that the manufacturing GDP will rise at a moderate pace of 1.3 per cent in 2020. However, the study indicates that this rate of growth is likely to be less than half what it was in the past few year. Companies will need to reconsider their approach to supply chain security. Businesses will need to focus their efforts on other management initiatives such a greater resilience in operations. According to Deloitte's study, manufacturers will be making decisions regarding work environments and work practices.
In order to prepare for the future, manufacturing companies need to develop pathways for careers and develop an inclusive culture. It is possible to improve manufacturing efficiency by increasing resilience and reduce waste. Combining lean principles and digital technologies can also reduce manufacturing variability.
Deloitte's new report, "Beyond Reskilling," examines diversity in the manufacturing sector as the US industry evolves. Deloitte's "Beyond Reskilling" report discusses how diversity is essential to manufacturing's future, and it highlights the benefits of having a diverse workforce.
FAQ
What are the responsibilities for a manufacturing manager
A manufacturing manager has to ensure that all manufacturing processes work efficiently and effectively. They should be aware of any issues within the company and respond accordingly.
They should also know how to communicate with other departments such as sales and marketing.
They should be informed about industry trends and be able make use of this information to improve their productivity and efficiency.
What are the four types of manufacturing?
Manufacturing is the process by which raw materials are transformed into useful products through machines and processes. Manufacturing involves many activities, including designing, building, testing and packaging, shipping, selling, service, and so on.
What are the responsibilities of a logistic manager?
A logistics manager makes sure that all goods are delivered on-time and in good condition. This is done by using his/her experience and knowledge of the company's products. He/she should ensure that sufficient stock is available in order to meet customer demand.
What is the responsibility of a production planner?
Production planners ensure that all project aspects are completed on time, within budget and within the scope. They also ensure that the product/service meets the client’s needs.
What does it mean to be a manufacturer?
Manufacturing Industries are businesses that produce products for sale. Consumers are people who purchase these goods. These companies employ many processes to achieve this purpose, such as production and distribution, retailing, management and so on. They produce goods from raw materials by using machines and other machinery. This includes all types and varieties of manufactured goods, such as food items, clothings, building supplies, furnitures, toys, electronics tools, machinery vehicles, pharmaceuticals medical devices, chemicals, among others.
How can manufacturing overproduction be reduced?
Better inventory management is key to reducing excess production. This would reduce the time needed to manage inventory. By doing this, we could free up resources for other productive tasks.
A Kanban system is one way to achieve this. A Kanban board is a visual display used to track work in progress. In a Kanban system, work items move through a sequence of states until they reach their final destination. Each state has a different priority level.
As an example, if work is progressing from one stage of the process to another, then the current task is complete and can be transferred to the next. If a task is still in its beginning stages, it will continue to be so until it reaches the end.
This allows you to keep work moving along while making sure that no work gets neglected. Managers can see how much work has been done and the status of each task at any time with a Kanban Board. This information allows them to adjust their workflow based on real-time data.
Lean manufacturing is another way to manage inventory levels. Lean manufacturing works to eliminate waste throughout every stage of the production chain. Any product that isn't adding value can be considered waste. The following are examples of common waste types:
-
Overproduction
-
Inventory
-
Packaging that is not necessary
-
Materials in excess
Manufacturers can reduce their costs and improve their efficiency by using these ideas.
Statistics
- Job #1 is delivering the ordered product according to specifications: color, size, brand, and quantity. (netsuite.com)
- In the United States, for example, manufacturing makes up 15% of the economic output. (twi-global.com)
- According to a Statista study, U.S. businesses spent $1.63 trillion on logistics in 2019, moving goods from origin to end user through various supply chain network segments. (netsuite.com)
- You can multiply the result by 100 to get the total percent of monthly overhead. (investopedia.com)
- According to the United Nations Industrial Development Organization (UNIDO), China is the top manufacturer worldwide by 2019 output, producing 28.7% of the total global manufacturing output, followed by the United States, Japan, Germany, and India.[52][53] (en.wikipedia.org)
External Links
How To
How to use lean manufacturing in the production of goods
Lean manufacturing is a management style that aims to increase efficiency and reduce waste through continuous improvement. It was first developed in Japan in the 1970s/80s by Taiichi Ahno, who was awarded the Toyota Production System (TPS), award from KanjiToyoda, the founder of TPS. Michael L. Watkins published the original book on lean manufacturing, "The Machine That Changed the World," in 1990.
Lean manufacturing refers to a set of principles that improve the quality, speed and costs of products and services. It emphasizes reducing defects and eliminating waste throughout the value chain. The five-steps of Lean Manufacturing are just-in time (JIT), zero defect and total productive maintenance (TPM), as well as 5S. Lean manufacturing eliminates non-value-added tasks like inspection, rework, waiting.
Lean manufacturing can help companies improve their product quality and reduce costs. Additionally, it helps them achieve their goals more quickly and reduces employee turnover. Lean Manufacturing is one of the most efficient ways to manage the entire value chains, including suppliers and customers as well distributors and retailers. Lean manufacturing is widely used in many industries. Toyota's philosophy has been a key driver of success in many industries, including automobiles and electronics.
Lean manufacturing includes five basic principles:
-
Define value - Find out what your business contributes to society, and what makes it different from other competitors.
-
Reduce waste - Get rid of any activity that does not add value to the supply chain.
-
Create Flow – Ensure that work flows smoothly throughout the process.
-
Standardize & Simplify - Make processes as consistent and repeatable as possible.
-
Build Relationships- Develop personal relationships with both internal as well as external stakeholders.
Although lean manufacturing isn't a new concept in business, it has gained popularity due to renewed interest in the economy after the 2008 global financial crisis. To increase their competitiveness, many businesses have turned to lean manufacturing. Economists think that lean manufacturing is a crucial factor in economic recovery.
Lean manufacturing is becoming a popular practice in automotive. It has many advantages. These include improved customer satisfaction, reduced inventory levels, lower operating costs, increased productivity, and better overall safety.
Any aspect of an enterprise can benefit from Lean manufacturing. However, it is particularly useful when applied to the production side of an organization because it ensures that all steps in the value chain are efficient and effective.
There are three main types:
-
Just-in Time Manufacturing, (JIT): This kind of lean manufacturing is also commonly known as "pull-systems." JIT means that components are assembled at the time of use and not manufactured in advance. This approach aims to reduce lead times, increase the availability of parts, and reduce inventory.
-
Zero Defects Manufacturing, (ZDM): ZDM is focused on ensuring that no defective products leave the manufacturing facility. You should repair any part that needs to be repaired during an assembly line. This is also true for finished products that require minor repairs before shipping.
-
Continuous Improvement (CI), also known as Continuous Improvement, aims at improving the efficiency of operations through continuous identification and improvement to minimize or eliminate waste. Continuous Improvement (CI) involves continuous improvement in processes, people, tools, and infrastructure.