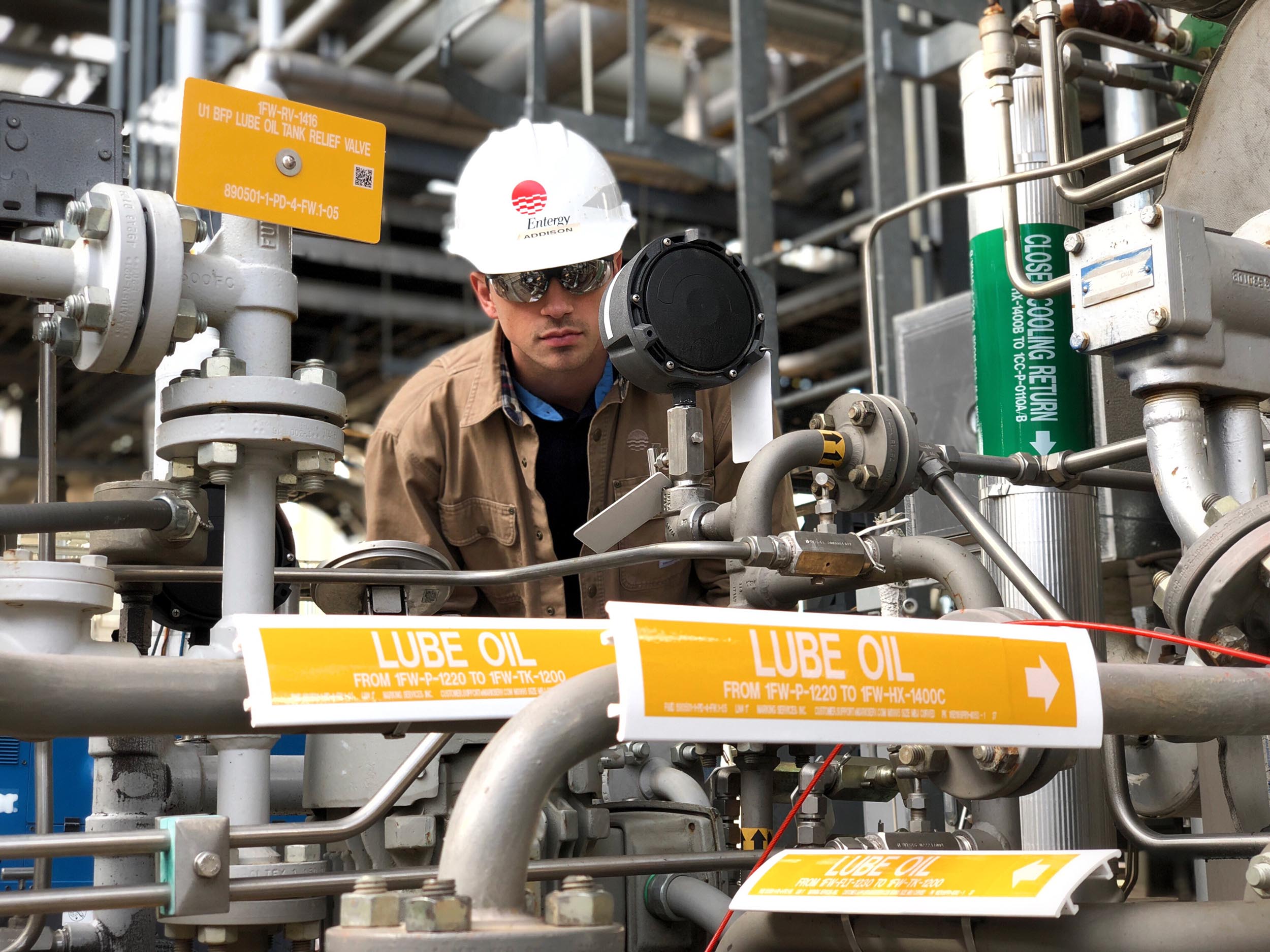
It is important that you include all the duties in the job description to attract the best people for transport and logistic jobs. These duties can include filling company paperwork and ordering raw materials. These duties can be omitted from job descriptions to make the job more appealing. However, this could lead to hiring the wrong person. This can cause problems for your business and customers. It also means that you have to spend time and money training the new employee.
Job description
Many industries employ transport and logistics professionals to move people or goods from one point to another. Some professionals work in shipping. Others may be involved with road maintenance. The job includes monitoring traffic congestion and safety. Those who work in this field are often required to adapt to changing business needs and work in various locations.
A job description that is effective focuses on the skills and training required for the job. It also reflects the company's culture, values, and culture. It should state whether the job is permanent or temporary.
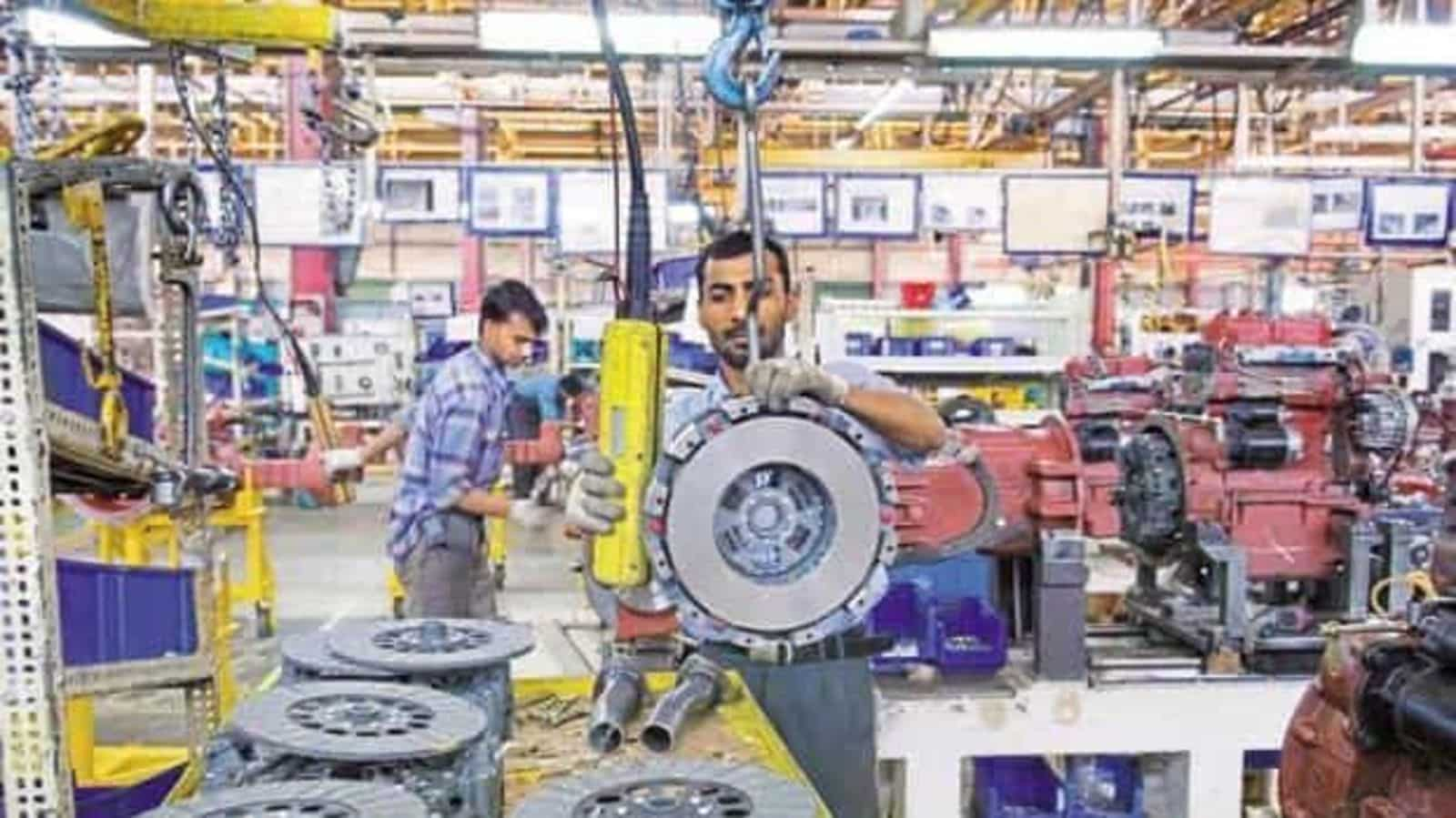
Salary
Many opportunities exist in transport and logistics jobs. These range from entry-level roles to more senior positions. Based on your industry and experience, the level of salary you earn will vary. Entry-level positions typically start at around $40,000 per a year. There is still room for advancement, though, as these salaries can increase.
Transportation and logistics careers offer a wide range of salaries, with some being more lucrative than others. Entry-level salaries may be lower than those of other fields, but if you're an experienced worker, you may earn considerably more. Some companies offer training on-site or pay for graduate level education.
Requirements
Many industries are looking for skilled transportation and logistics workers. The primary goal of these jobs is to ensure that goods are delivered on time and at the lowest cost. Employers must hire the right personnel with the correct skills. Even though junior staff don't need to have any previous training, anyone who wants to be a Supply Chain Practitioner Advanced Apprenticeship should have the relevant qualifications.
A good degree is a must if you're interested in a career as a transport and logistics professional. There are many courses that will help you expand your knowledge and improve your skills. The Chartered Institute of Logistics and Transport UK has a Level 2 Certificate for Transport and Logistics. This course is great for those just starting out in this field. You can also gain valuable work experience by undertaking a graduate recruitment scheme, which is offered by many large logistics companies.
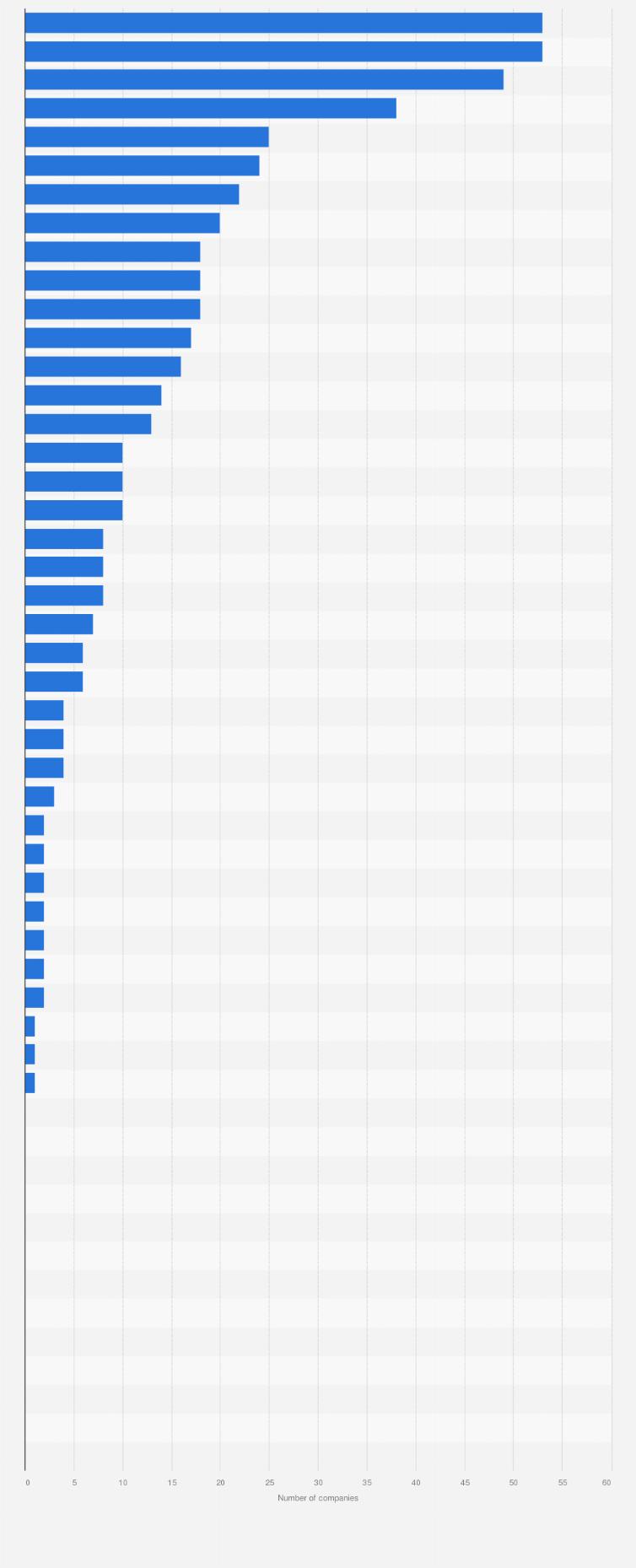
Localities
There are many career options in logistics and transport. These careers often require you to plan and assess different distribution methods. These jobs require analytical thinking and the ability of managing complex data. Excellent communication skills are essential. Some jobs require you travel to remote places. There are many graduate training programs in logistics and transport that will equip you with the skills necessary to be successful in this field. Some of these programmes will also provide you with paid internships.
Transport and logistics occupations are in great demand. They are expected to increase by 3% from 2019-2029, the same as the national median. However, some occupations are expected to grow faster than average such as those that require commercial pilots or airline pilots. This sector also includes driver/sales workers as well as delivery truck drivers.
FAQ
How can manufacturing overproduction be reduced?
Improved inventory management is the key to reducing overproduction. This would decrease the time that is spent on inefficient activities like purchasing, storing, or maintaining excess stock. This will allow us to free up resources for more productive tasks.
Kanban systems are one way to achieve this. A Kanbanboard is a visual tool that allows you to keep track of the work being done. In a Kanban system, work items move through a sequence of states until they reach their final destination. Each state has a different priority level.
If work is moving from one stage to the other, then the current task can be completed and moved on to the next. A task that is still in the initial stages of a process will be considered complete until it moves on to the next stage.
This keeps work moving and ensures no work is lost. Managers can see how much work has been done and the status of each task at any time with a Kanban Board. This data allows them adjust their workflow based upon real-time data.
Lean manufacturing is another option to control inventory levels. Lean manufacturing focuses on eliminating waste throughout the entire production chain. Any product that isn't adding value can be considered waste. There are several types of waste that you might encounter:
-
Overproduction
-
Inventory
-
Unnecessary packaging
-
Exceed materials
By implementing these ideas, manufacturers can improve efficiency and cut costs.
What is the role of a production manager?
Production planners ensure all aspects of the project are delivered within time and budget. They also ensure the quality of the product and service meets the client's requirements.
What are manufacturing and logistics?
Manufacturing is the act of producing goods from raw materials using machines and processes. Logistics is the management of all aspects of supply chain activities, including procurement, production planning, distribution, warehousing, inventory control, transportation, and customer service. Sometimes manufacturing and logistics are combined to refer to a wider term that includes both the process of creating products as well as their delivery to customers.
Statistics
- (2:04) MTO is a production technique wherein products are customized according to customer specifications, and production only starts after an order is received. (oracle.com)
- It's estimated that 10.8% of the U.S. GDP in 2020 was contributed to manufacturing. (investopedia.com)
- You can multiply the result by 100 to get the total percent of monthly overhead. (investopedia.com)
- In 2021, an estimated 12.1 million Americans work in the manufacturing sector.6 (investopedia.com)
- [54][55] These are the top 50 countries by the total value of manufacturing output in US dollars for its noted year according to World Bank.[56] (en.wikipedia.org)
External Links
How To
How to Use Just-In-Time Production
Just-intime (JIT), a method used to lower costs and improve efficiency in business processes, is called just-in-time. It's the process of obtaining the right amount and timing of resources when you need them. This means that your only pay for the resources you actually use. The term was first coined by Frederick Taylor, who developed his theory while working as a foreman in the early 1900s. He observed how workers were paid overtime if there were delays in their work. He realized that workers should have enough time to complete their jobs before they begin work. This would help increase productivity.
JIT is a way to plan ahead and make sure you don't waste any money. Also, you should look at the whole project from start-to-finish and make sure you have the resources necessary to address any issues. You'll be prepared to handle any potential problems if you know in advance. This will ensure that you don't spend more money on things that aren't necessary.
There are many types of JIT methods.
-
Demand-driven JIT: You order the parts and materials you need for your project every other day. This will allow you to track how much material you have left over after using it. You'll also be able to estimate how long it will take to produce more.
-
Inventory-based : You can stock the materials you need in advance. This allows you to predict how much you can expect to sell.
-
Project-driven: This means that you have enough money to pay for your project. When you know how much you need, you'll purchase the appropriate amount of materials.
-
Resource-based JIT: This is the most popular form of JIT. You allocate resources based on the demand. You might assign more people to help with orders if there are many. If you don't receive many orders, then you'll assign fewer employees to handle the load.
-
Cost-based: This is the same as resource-based except that you don't care how many people there are but how much each one of them costs.
-
Price-based: This approach is very similar to the cost-based method except that you don't look at individual workers costs but the total cost of the company.
-
Material-based: This is very similar to cost-based but instead of looking at total costs of the company you are concerned with how many raw materials you use on an average.
-
Time-based: This is another variation of resource-based JIT. Instead of focusing only on how much each employee is costing, you should focus on how long it takes to complete your project.
-
Quality-based JIT - This is another form of resource-based JIT. Instead of looking at the labor costs and time it takes to make a product, think about its quality.
-
Value-based JIT: One of the most recent forms of JIT. In this case, you're not concerned with how well the products perform or whether they meet customer expectations. Instead, you're focused on how much value you add to the market.
-
Stock-based: This is an inventory-based method that focuses on the actual number of items being produced at any given time. It's useful when you want maximum production and minimal inventory.
-
Just-intime planning (JIT), is a combination JIT/sales chain management. It is the process that schedules the delivery of components within a short time of their order. This is important as it reduces lead time and increases throughput.