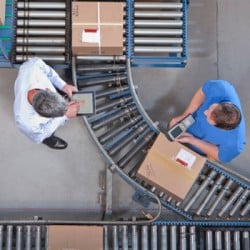
Are you seeking a job in engineering? Find out what jobs are available by reading on. This article will talk about the different types of jobs, their average salary and the educational requirements. We'll also talk about the skills needed and where to find these jobs. Apply for the job that you find most exciting. Good luck! Before you apply for an industrial engineering job in the future, be sure to read through the job description.
Job description
The job of an industrial engineer is not for the faint of heart. This job involves using engineering principles and technology in order to improve production processes and layouts within companies. This engineer creates analytics and tools to assist companies in monitoring their production costs and schedules. Before implementing new projects, he or she reviews production data and determines areas that need improvement.
An industrial engineer job requires a degree of mechanical engineering. An engineer in this field must have a good understanding of engineering principles, practices, and a flair for solving problems. An industrial engineer must combine technical knowledge with an understanding and appreciation of human capabilities. Industrial engineers must have excellent organizational skills, strong analytical skills, and good communicators. They are responsible to improve the production processes of businesses and manage warehouses and factories.
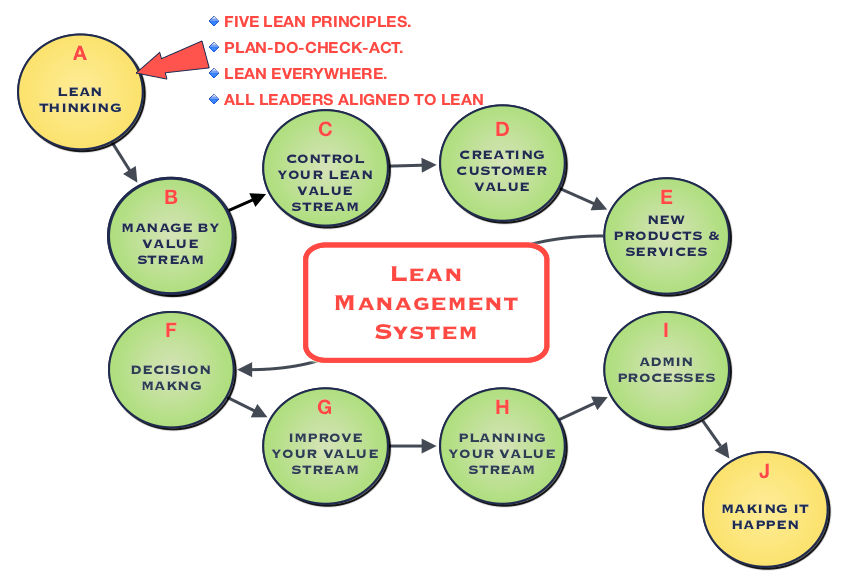
Salary range
The range of salaries for industrial engineers depends on experience. Starting salaries are around $85,000, but the amount of compensation can go up to $100,000. The following table shows the average salary for industrial engineers according to experience. Ventura, California, for example, can expect an Entry-Level Engineer to make around $86,000 per year. For an experienced Industrial Engineer, the salary range is $85,000 to $100,000 per year. A four-year degree is usually required to be hired as a Project Engineer.
The average income for an industrial engineer varies according to where you live, your industry, and your years of experience. The average salary for an industrial engineer in New York is $60,700 to $140,000 each year. Although the trend towards higher salaries is not easy to track, they have increased by more 40 percent over 10 years. Expectations are that this trend will continue. Monster's Salary tool can help you find out more about the salary ranges in your region.
Education required
Although licenses are not necessary for industrial engineers, they may be required as a condition of government contracts. For entry-level positions, industrial engineers don't require licensing. To be eligible for professional licensure, they must have relevant work experience and a degree obtained from an accredited institution. Industrial engineers can be found working in offices, factories, and labs. Many industrial engineers are employed in manufacturing aerospace products, engineering services, medical and control instrument manufacturing, and architectural and engineering.
Many industrial engineers do internships as part of their college careers. This helps them gain valuable work experience. Even though entry-level industrial engineering jobs don't typically require professional experience but you can gain additional engineering experience to give your company an edge. Internships are also a good option if you plan to work for a government agency or another organization. Industrial engineers might also need security clearance in addition to their internships.
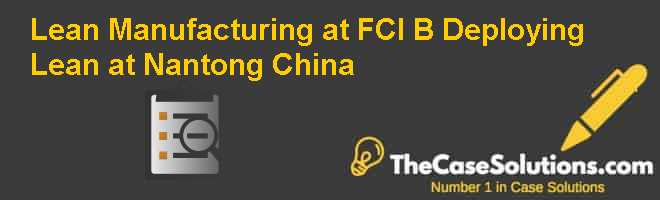
Locations
Many industrial engineering jobs are available and highly rewarding. The most common entry-level tasks in this field include completing calculations, testing and monitoring devices, and documenting results. They might also help develop budgets or track metrics. An industrial engineer's work may involve standing for extended periods of time. Industrial engineers must communicate clearly. In some cases, they work under the supervision of a more senior engineer.
Industrial engineers collaborate with companies to design efficient production processes that require the least energy and resource. Their primary objective is to maximize efficiency and reduce costs while maintaining high labor productivity. Industrial engineers work in offices, factories and other settings to improve the operational efficiency of companies. A bachelor's degree or equivalent in industrial engineering is required to be eligible for entry-level jobs in industrial engineering. According to the Bureau of Labor Statistics in 2021, industrial engineers will earn a median salary of $95,300.
FAQ
What types of jobs can you find in logistics
There are many jobs available in logistics. Here are some:
-
Warehouse workers: They load and unload trucks, pallets, and other cargo.
-
Transportation drivers: They drive trucks and trailers and deliver goods and make pick-ups.
-
Freight handlers, - They sort out and pack freight in warehouses.
-
Inventory managers - They oversee the inventory of goods in warehouses.
-
Sales representatives - They sell products.
-
Logistics coordinators are responsible for organizing and planning logistics operations.
-
Purchasing agents – They buy goods or services necessary to run a company.
-
Customer service representatives - Answer calls and email from customers.
-
Shipping clerks - They process shipping orders and issue bills.
-
Order fillers - These people fill orders based on what has been ordered.
-
Quality control inspectors (QCI) - They inspect all incoming and departing products for potential defects.
-
Others - There are many types of jobs in logistics such as transport supervisors and cargo specialists.
How can manufacturing overproduction be reduced?
Improved inventory management is the key to reducing overproduction. This would decrease the time that is spent on inefficient activities like purchasing, storing, or maintaining excess stock. By doing this, we could free up resources for other productive tasks.
A Kanban system is one way to achieve this. A Kanban board, a visual display to show the progress of work, is called a Kanban board. In a Kanban system, work items move through a sequence of states until they reach their final destination. Each state has a different priority level.
To illustrate, work can move from one stage or another when it is complete enough for it to be moved to a new stage. A task that is still in the initial stages of a process will be considered complete until it moves on to the next stage.
This allows for work to continue moving forward, while also ensuring that there is no work left behind. With a Kanban board, managers can see exactly how much work is being done at any given moment. This information allows managers to adjust their workflow based off real-time data.
Lean manufacturing is another way to manage inventory levels. Lean manufacturing seeks to eliminate waste from every step of the production cycle. Any product that isn't adding value can be considered waste. Some common types of waste include:
-
Overproduction
-
Inventory
-
Packaging not required
-
Material surplus
Manufacturers can reduce their costs and improve their efficiency by using these ideas.
What's the difference between Production Planning & Scheduling?
Production Planning (PP), or production planning, is the process by which you determine what products are needed at any given time. This can be done by forecasting demand and identifying production capabilities.
Scheduling is the process that assigns dates to tasks so they can get completed within a given timeframe.
Statistics
- [54][55] These are the top 50 countries by the total value of manufacturing output in US dollars for its noted year according to World Bank.[56] (en.wikipedia.org)
- According to a Statista study, U.S. businesses spent $1.63 trillion on logistics in 2019, moving goods from origin to end user through various supply chain network segments. (netsuite.com)
- It's estimated that 10.8% of the U.S. GDP in 2020 was contributed to manufacturing. (investopedia.com)
- In the United States, for example, manufacturing makes up 15% of the economic output. (twi-global.com)
- In 2021, an estimated 12.1 million Americans work in the manufacturing sector.6 (investopedia.com)
External Links
How To
How to use 5S to increase Productivity in Manufacturing
5S stands as "Sort", Set In Order", Standardize", Separate" and "Store". The 5S methodology was developed at Toyota Motor Corporation in 1954. It allows companies to improve their work environment, thereby achieving greater efficiency.
The basic idea behind this method is to standardize production processes, so they become repeatable, measurable, and predictable. It means tasks like cleaning, sorting or packing, labeling, and storing are done every day. Because workers know what they can expect, this helps them perform their jobs more efficiently.
There are five steps that you need to follow in order to implement 5S. Each step requires a different action to increase efficiency. If you sort items, it makes them easier to find later. You arrange items by placing them in an order. Once you have separated your inventory into groups and organized them, you will store these groups in easily accessible containers. You can also label your containers to ensure everything is properly labeled.
Employees must be able to critically examine their work practices. Employees should understand why they do the tasks they do, and then decide if there are better ways to accomplish them. They must learn new skills and techniques in order to implement the 5S system.
In addition to increasing efficiency, the 5S method also improves morale and teamwork among employees. They will feel motivated to strive for higher levels of efficiency once they start to see results.