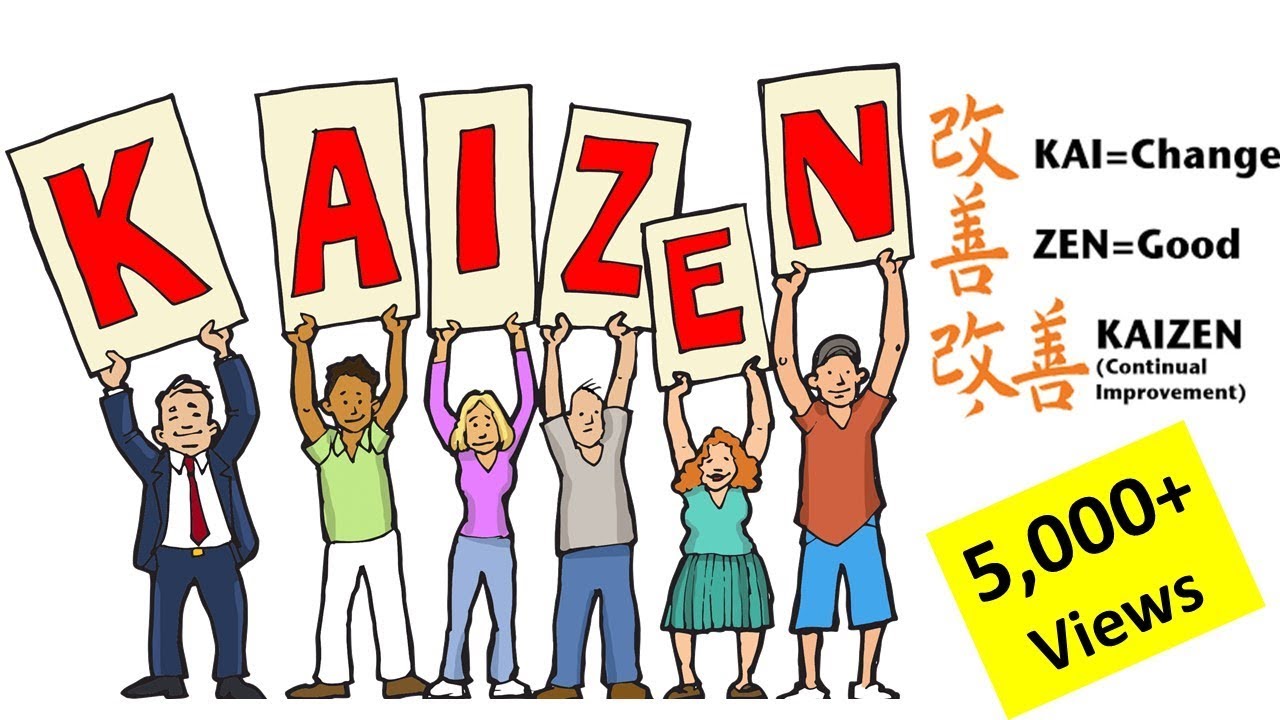
Lean thinking is a method to improve performance in an organization. It's about eliminating wastes and unvalued tasks from your process. It is also an opportunity to create a lean organization culture. A lean culture is a collection of values, principles and practices that increase employee morale and quality and improve productivity. It also helps to create a more sustainable working environment.
The first step in implementing lean thinking is to identify value for your customer. This involves understanding the entire value chain and the needs of your customers. Once you know what your customers need, you can identify which steps are involved in your processes. By identifying the steps within different processes, you can determine if your current process is inefficient. To see how your business is operating, you can also use value streaming mapping. The value stream mapping shows how your business works and the value that each process creates.
Lean thinking relies on flow. It refers to the ability quickly to change from one activity into another. This is particularly important for responding to customer demands. It also reduces the need for inventory and backlogs. It allows workers the ability to quickly switch between tasks.
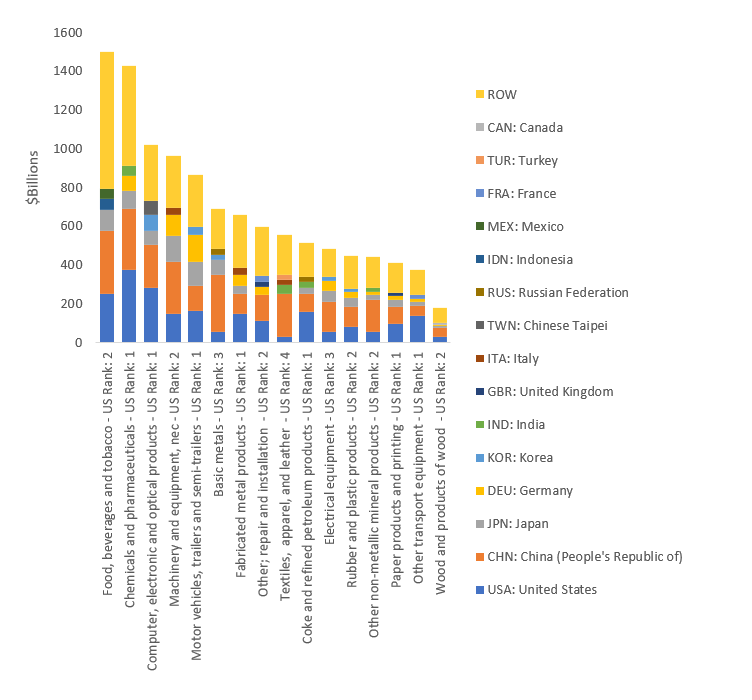
Lean organizations adopt a lean approach to managing output. They encourage collaboration and clear communication. They encourage quality assurance, and celebrate the successes. They minimize the need to overcharge suppliers and customers.
Lean thinking involves a continual process. Lean thinking can be applied to all types of work. It can be used to reduce environmental damage, waste, and increase employee morale. Although Lean thinking is most commonly applied to manufacturing businesses, it can also be applied in other areas of business.
In order to implement lean production methods, it is important to create a culture that promotes lean thinking. Culture should have a clear definition and encourage employee motivation. It must also be willing and able to take small steps in the right direction on a daily basis. This is called Kaizen.
Lean thinking requires continuous improvement. To improve the quality of your product you have to be open to small improvements each day. You can do this by making changes in the company or using standardized work. A standardized work describes a graphic description of a smooth flow of work. It has a clear location for everything. It also makes it easy to overcome any obstacles that could prevent smooth work.
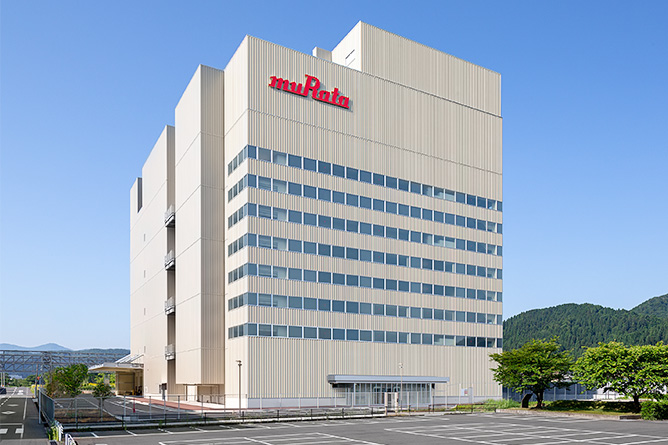
When you are implementing lean production processes, it is important that you consider other production metrics. This ratio shows how often an item is available for production. It also shows how frequently planned maintenance is needed. The quality ratio measures how well a supplier can deliver high quality products.
Importantly, you should be aware of potential dangers associated with the "Just In Time." principle. This principle ensures that supplies are delivered at the last minute. It helps you focus your mind on the task at the hand and allows you to concentrate. However, it can create problems for the industry.
FAQ
What is production planning?
Production Planning refers to the development of a plan for every aspect of production. It is important to have everything ready and planned before you start shooting. This document should also include information on how to get the best result on set. It should include information about shooting locations, casting lists, crew details, equipment requirements, and shooting schedules.
The first step is to decide what you want. You might have an idea of where you want to film, or you may have specific locations or sets in mind. Once you have identified your locations and scenes it's time to begin figuring out what elements you will need for each one. For example, you might decide that you need a car but don't know exactly what model you want. You could look online for cars to see what options are available, and then narrow down your choices by selecting between different makes or models.
After you have chosen the right car, you will be able to begin thinking about accessories. Do you need people sitting in the front seats? Maybe you need someone to move around in the back. Maybe you want to change the interior color from black to white? These questions will help you determine the exact look and feel of your car. Also, think about what kind of shots you would like to capture. Will you be filming close-ups or wide angles? Maybe you want to show the engine and the steering wheel. These details will help identify the exact car you wish to film.
Once you have determined all of the above, you can move on to creating a schedule. A schedule will tell you when you need to start shooting and when you need to finish. Each day will include the time when you need to arrive at the location, when you need to leave and when you need to return home. This way, everyone knows what they need to do and when. You can also make sure to book extra staff in advance if you have to hire them. It's not worth paying someone to show up if you haven't told him.
You will need to factor in the days that you have to film when creating your schedule. Some projects take only a few days while others can last several weeks. You should consider whether you will need more than one shot per week when creating your schedule. Multiple takes of the same location will lead to higher costs and take more time. It is better to be cautious and take fewer shots than you risk losing money if you are not sure if multiple takes are necessary.
Budget setting is an important part of production planning. As it will allow you and your team to work within your financial means, setting a realistic budget is crucial. You can always lower the budget if you encounter unexpected problems. You shouldn't underestimate the amount you'll spend. If you underestimate how much something costs, you'll have less money to pay for other items.
Production planning is a detailed process. But, once you understand the workings of everything, it becomes easier for future projects to be planned.
How does a Production Planner differ from a Project Manager?
The primary difference between a producer planner and a manager of a project is that the manager usually plans and organizes the whole project, while a production planner is only involved in the planning stage.
Is automation important for manufacturing?
Not only is automation important for manufacturers, but it's also vital for service providers. It allows them provide faster and more efficient services. It reduces human errors and improves productivity, which in turn helps them lower their costs.
What does the term manufacturing industries mean?
Manufacturing Industries are companies that manufacture products. Consumers are people who purchase these goods. These companies use a variety processes such as distribution, retailing and management to accomplish their purpose. They create goods from raw materials, using machines and various other equipment. This includes all types and varieties of manufactured goods, such as food items, clothings, building supplies, furnitures, toys, electronics tools, machinery vehicles, pharmaceuticals medical devices, chemicals, among others.
What skills should a production planner have?
Being a production planner is not easy. You need to be organized and flexible. Effective communication with clients and colleagues is essential.
Statistics
- You can multiply the result by 100 to get the total percent of monthly overhead. (investopedia.com)
- According to the United Nations Industrial Development Organization (UNIDO), China is the top manufacturer worldwide by 2019 output, producing 28.7% of the total global manufacturing output, followed by the United States, Japan, Germany, and India.[52][53] (en.wikipedia.org)
- It's estimated that 10.8% of the U.S. GDP in 2020 was contributed to manufacturing. (investopedia.com)
- (2:04) MTO is a production technique wherein products are customized according to customer specifications, and production only starts after an order is received. (oracle.com)
- According to a Statista study, U.S. businesses spent $1.63 trillion on logistics in 2019, moving goods from origin to end user through various supply chain network segments. (netsuite.com)
External Links
How To
Six Sigma in Manufacturing:
Six Sigma is defined as "the application of statistical process control (SPC) techniques to achieve continuous improvement." It was developed by Motorola's Quality Improvement Department at their plant in Tokyo, Japan, in 1986. Six Sigma's core idea is to improve the quality of processes by standardizing and eliminating defects. Many companies have adopted this method in recent years. They believe there is no such thing a perfect product or service. Six Sigma aims to reduce variation in the production's mean value. This means that if you take a sample of your product, then measure its performance against the average, you can find out what percentage of the time the process deviates from the norm. If you notice a large deviation, then it is time to fix it.
Understanding the dynamics of variability within your business is the first step in Six Sigma. Once you understand this, you can then identify the causes of variation. This will allow you to decide if these variations are random and systematic. Random variations occur when people do mistakes. Symmetrical variations are caused due to factors beyond the process. These are, for instance, random variations that occur when widgets are made and some fall off the production line. But if you notice that every widget you make falls apart at the exact same place each time, this would indicate that there is a problem.
Once you've identified where the problems lie, you'll want to design solutions to eliminate those problems. That solution might involve changing the way you do things or redesigning the process altogether. After implementing the new changes, you should test them again to see if they worked. If they don’t work, you’ll need to go back and rework the plan.