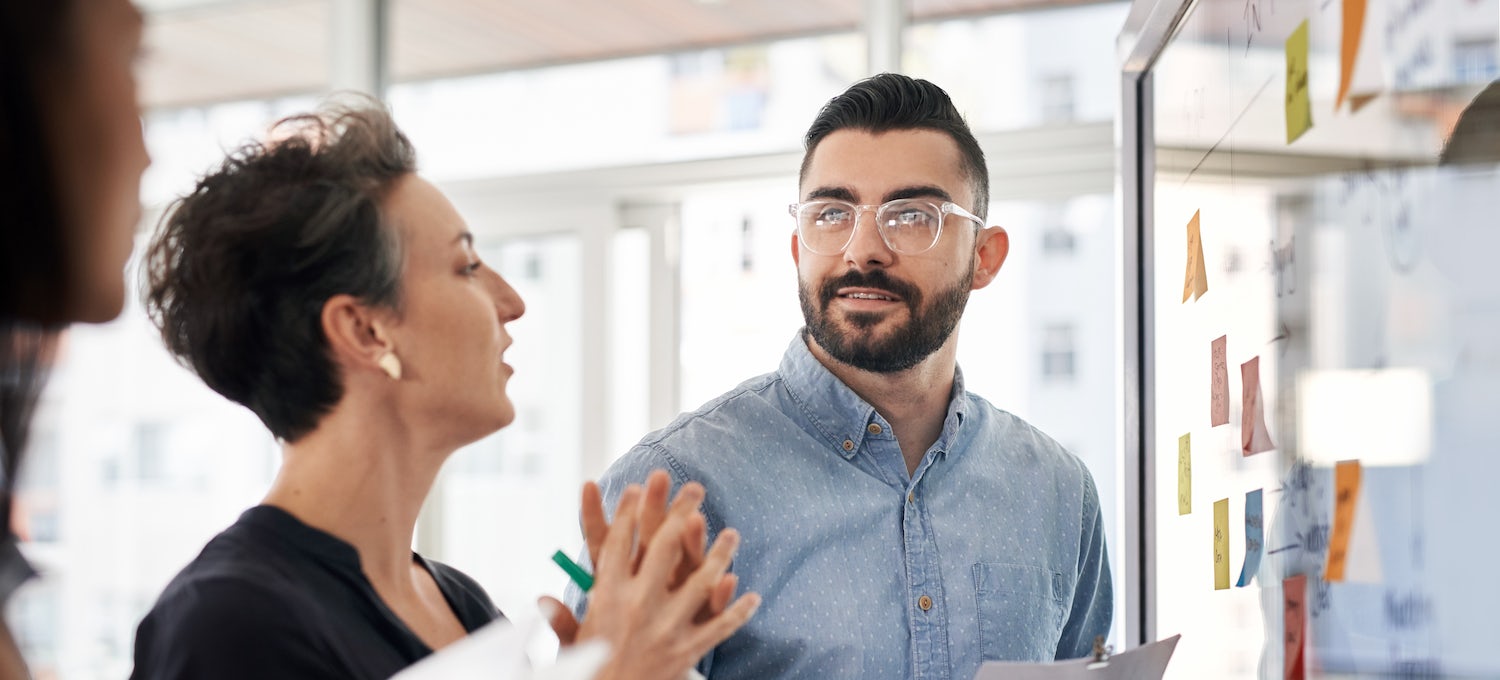
There are thousands of manufacturing jobs in Connecticut that need to be filled. There are currently 411 factories in Connecticut and 159,000 employees. Manufacturing is the largest contributor to the state’s gross state products and has a salary that is above the average for the state. The Connecticut Business and Industry Association recently released a survey of manufacturing workforce needs. The state has 13,000 unfilled manufacturing jobs, with many companies struggling for younger workers.
The Connecticut manufacturing workforce is older than average, with over a third of workers being over 55. Many companies have relocated their manufacturing facilities in order to lower labor cost. Other operations also began using new machinery or automation. Manufacturing was also considered dirty and dangerous in the past, but the reputation has changed. Companies now offer apprenticeships, internships, as well entry-level positions. Manufacturing is Connecticut's third largest employer of jobs. Its high-tech operations are a key competitive advantage.
Connecticut offers many private and public education programs to help people obtain manufacturing job skills. Manufacturing Innovation Fund supports comprehensive high schools and universities as well as vocational high schools. It also supports online training, pre-apprenticeships, career activities, and career activities, for K-12 students.
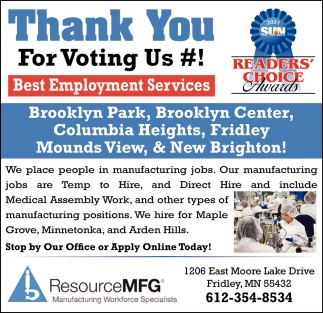
The backgrounds of advanced manufacturing workers are varied. Many people enter the industry straight out of high school. Others have worked in other fields for years before switching to manufacturing. You may have graduated from school or served in the military. Many companies will pay tuition for advanced manufacturing programs. Other programs provide wage subsidies for entry-level training.
In addition to reintroducing technical education options, the state's Comprehensive high schools have also started doing so. One example is the Grasso Tech Welding program. It will begin in fall 2019. Employers that hire through the EB are open to hiring students from Connecticut. The Eastern Connecticut Manufacturing Pipeline serves regional advanced manufacturing companies. It was inspired by the Eastern Connecticut Workforce Investment Board's Manufacturing Pipeline.
The Manufacturing Careers Program is designed to help job seekers who are interested in manufacturing careers demonstrate their readiness for entry level work. It connects pre-screened job applicants with manufacturers and other employers. The program offers a CNC Basics training course as well as a career path that is industry-focused. The Advanced Manufacturing Employer Partnership provides wage subsidies and entry-level training to those who are enrolled in this program.
The manufacturing industry may be unfamiliar to young workers entering the workforce. This lack of awareness may make it difficult for them to participate in these education programs. The state has allocated tens of millions of dollars for these programs. The programs aren't as accessible because the young don't know they exist.
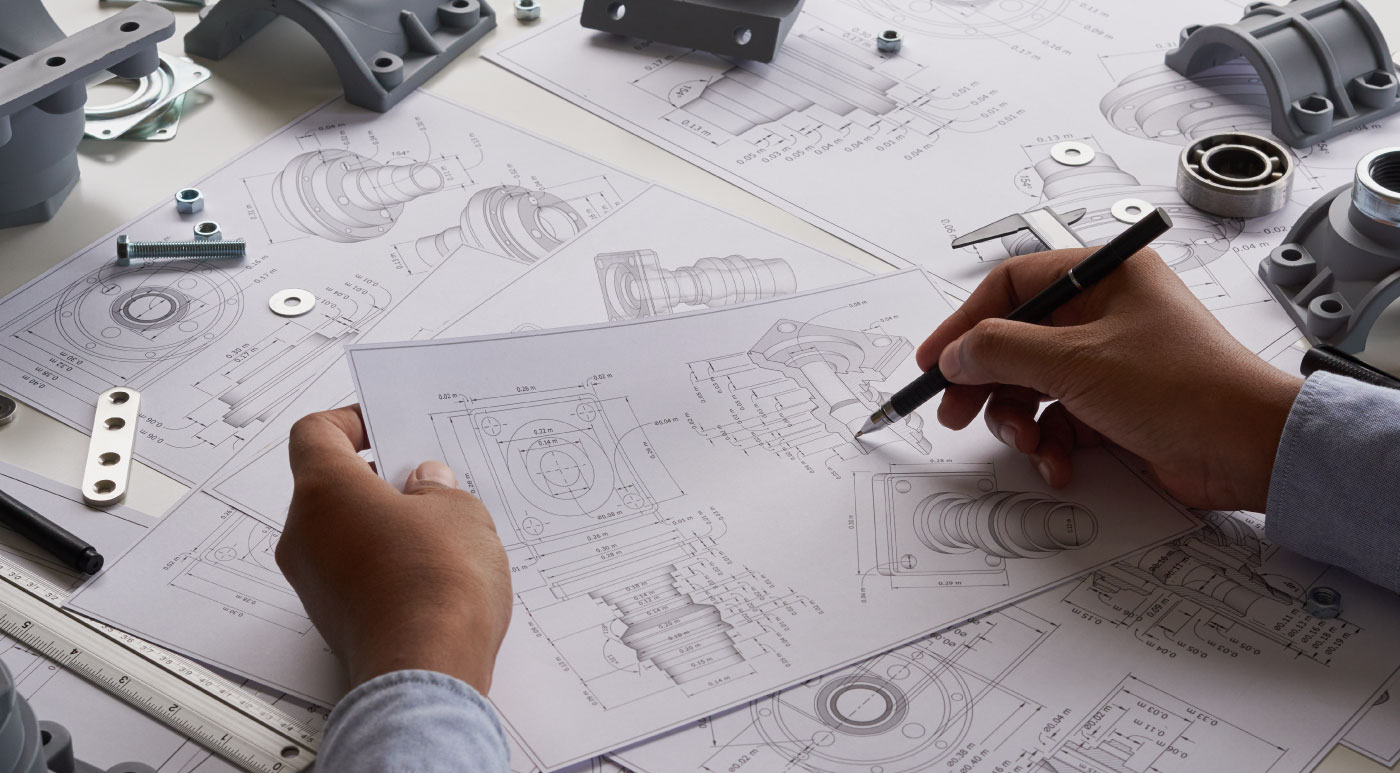
A state-wide STEM Town initiative is an innovative solution to Connecticut's manufacturing job shortage. This would include reallocating resources to improve education programs to address the needs of manufacturers.
FAQ
How can manufacturing reduce production bottlenecks?
You can avoid bottlenecks in production by making sure that everything runs smoothly throughout the production cycle, from the moment you receive an order to the moment the product is shipped.
This includes both planning for capacity and quality control.
Continuous improvement techniques such Six Sigma can help you achieve this.
Six Sigma Management System is a method to increase quality and reduce waste throughout your organization.
It's all about eliminating variation and creating consistency in work.
What is the importance of logistics in manufacturing?
Logistics are an essential part of any business. They help you achieve great results by helping you manage all aspects of product flow, from raw materials to finished goods.
Logistics plays a significant role in reducing cost and increasing efficiency.
What is the responsibility of a manufacturing manager?
A manufacturing manager has to ensure that all manufacturing processes work efficiently and effectively. They should also be aware and responsive to any company problems.
They should also be able communicate with other departments, such as sales or marketing.
They should be up to date on the latest trends and be able apply this knowledge to increase productivity and efficiency.
What are my options for learning more about manufacturing
Experience is the best way for you to learn about manufacturing. You can read books, or watch instructional videos if you don't have the opportunity to do so.
Can some manufacturing processes be automated?
Yes! Yes! Automation has existed since ancient times. The Egyptians discovered the wheel thousands and years ago. To help us build assembly lines, we now have robots.
There are many applications for robotics in manufacturing today. They include:
-
Automated assembly line robots
-
Robot welding
-
Robot painting
-
Robotics inspection
-
Robots that create products
There are many other examples of how manufacturing could benefit from automation. 3D printing is a way to make custom products quickly and without waiting weeks or months for them to be manufactured.
What jobs are available in logistics?
There are many jobs available in logistics. These are some of the jobs available in logistics:
-
Warehouse workers – They load and unload pallets and trucks.
-
Transportation drivers: They drive trucks and trailers and deliver goods and make pick-ups.
-
Freight handlers: They sort and package freight in warehouses.
-
Inventory managers - They oversee the inventory of goods in warehouses.
-
Sales reps are people who sell products to customers.
-
Logistics coordinators - They plan and organize logistics operations.
-
Purchasing agents: They are responsible for purchasing goods and services to support company operations.
-
Customer service representatives - They answer calls and emails from customers.
-
Shippers clerks - They process shipping order and issue bills.
-
Order fillers – They fill orders based upon what was ordered and shipped.
-
Quality control inspectors (QCI) - They inspect all incoming and departing products for potential defects.
-
Other - Logistics has many other job opportunities, including transportation supervisors, logistics specialists, and cargo specialists.
How does a production planner differ from a project manager?
The difference between a product planner and project manager is that a planer is typically the one who organizes and plans the entire project. A production planner, however, is mostly involved in the planning stages.
Statistics
- It's estimated that 10.8% of the U.S. GDP in 2020 was contributed to manufacturing. (investopedia.com)
- Many factories witnessed a 30% increase in output due to the shift to electric motors. (en.wikipedia.org)
- Job #1 is delivering the ordered product according to specifications: color, size, brand, and quantity. (netsuite.com)
- In 2021, an estimated 12.1 million Americans work in the manufacturing sector.6 (investopedia.com)
- [54][55] These are the top 50 countries by the total value of manufacturing output in US dollars for its noted year according to World Bank.[56] (en.wikipedia.org)
External Links
How To
How to use lean manufacturing in the production of goods
Lean manufacturing is a management system that aims at increasing efficiency and reducing waste. It was created in Japan by Taiichi Ohno during the 1970s and 80s. He received the Toyota Production System award (TPS), from Kanji Toyoda, founder of TPS. Michael L. Watkins published the "The Machine That Changed the World", the first book about lean manufacturing. It was published in 1990.
Lean manufacturing can be described as a set or principles that are used to improve quality, speed and cost of products or services. It emphasizes reducing defects and eliminating waste throughout the value chain. Lean manufacturing can be described as just-in–time (JIT), total productive maintenance, zero defect (TPM), or even 5S. Lean manufacturing is about eliminating activities that do not add value, such as inspection, rework, and waiting.
Lean manufacturing improves product quality and costs. It also helps companies reach their goals quicker and decreases employee turnover. Lean manufacturing can be used to manage all aspects of the value chain. Customers, suppliers, distributors, retailers and employees are all included. Lean manufacturing practices are widespread in many industries. Toyota's philosophy is a great example of this. It has helped to create success in automobiles as well electronics, appliances and healthcare.
Five basic principles of Lean Manufacturing are included in lean manufacturing
-
Define value - Find out what your business contributes to society, and what makes it different from other competitors.
-
Reduce Waste - Eliminate any activity that doesn't add value along the supply chain.
-
Create Flow – Ensure that work flows smoothly throughout the process.
-
Standardize and Simplify – Make processes as consistent, repeatable, and as simple as possible.
-
Building Relationships – Establish personal relationships with both external and internal stakeholders.
Lean manufacturing, although not new, has seen renewed interest in the economic sector since 2008. Many businesses have adopted lean manufacturing techniques to help them become more competitive. Many economists believe lean manufacturing will play a major role in economic recovery.
Lean manufacturing, which has many benefits, is now a standard practice in the automotive industry. These include higher customer satisfaction, lower inventory levels, lower operating expenses, greater productivity, and improved overall safety.
Any aspect of an enterprise can benefit from Lean manufacturing. However, it is particularly useful when applied to the production side of an organization because it ensures that all steps in the value chain are efficient and effective.
There are three main types in lean manufacturing
-
Just-in Time Manufacturing (JIT), also known as "pull system": This form of lean manufacturing is often referred to simply as "pull". JIT is a method in which components are assembled right at the moment of use, rather than being manufactured ahead of time. This method reduces lead times, increases availability, and decreases inventory.
-
Zero Defects Manufacturing (ZDM),: ZDM is a system that ensures no defective units are left the manufacturing facility. You should repair any part that needs to be repaired during an assembly line. This is true even for finished products that only require minor repairs prior to shipping.
-
Continuous Improvement (CI): CI aims to improve the efficiency of operations by continuously identifying problems and making changes in order to eliminate or minimize waste. Continuous Improvement involves continuous improvement of processes.