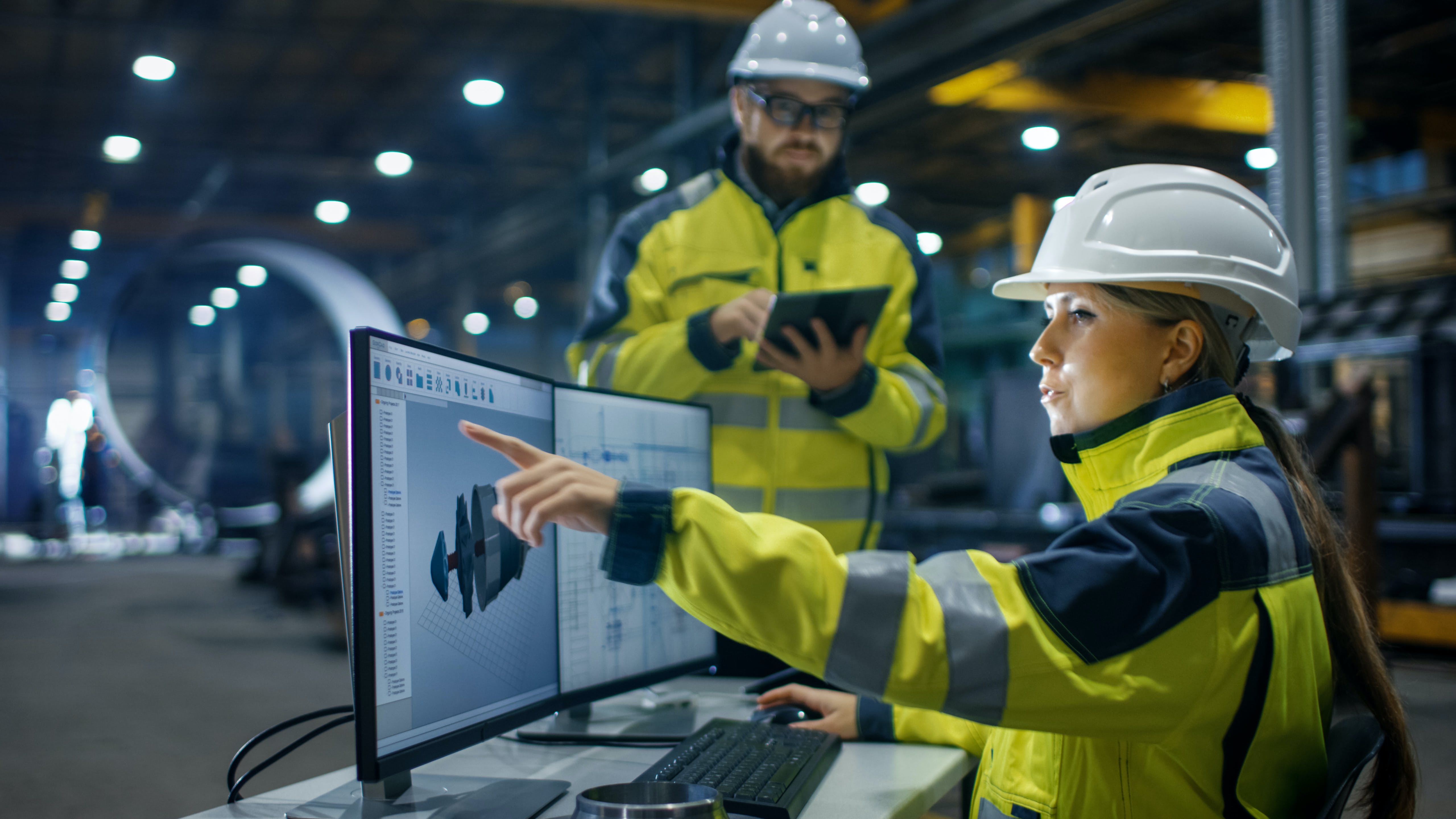
Global supply chains have seen many changes over the years. They have moved from being primarily an industrial problem to becoming a serious economic threat. It is worth keeping an eye on new developments. Global supply chains are complex systems that interact in many ways.
Global value chains contain a combination of capital, intangibles, flows, and other resources. They are the result of economies, specialization, long-standing relationships, scale, and relationships. While some value chains are highly capital-intensive, other value chains are more regionalized.
Global supply chains are dynamic, multi-dimensional, and increasingly complex. They are an essential component of global trade and the functioning of economies. They are also susceptible to disruptions. These disruptions are either short-term or long-lasting. Building a resilient, flexible, and diversified supply chain is the best way to combat these disruptions. This requires a holistic approach that includes structural reform and strategic initiatives as well as prudent risk management. The first step to building a supply system that can withstand the next storm, is identifying the biggest problems and evaluating the solutions.
Along with assessing the risk of disruptions in supply chains, companies must also take into account the risks associated to manufacturing, labor and materials. They should also simulate extreme supply/demand disruptions in an effort to gauge their impact. They should also assess their inventories for critical materials and ensure that there is enough supply to meet demand. You need to take a strategic approach to building a resilient supply channel. This might include shifting production to more flexible areas, improving supply chain tech, and implementing assured sources of supply.
The COVID-19 pandemic caused major disruptions in global supply chains. While some countries placed tariffs on one another, others imposed penalties against the other. These tariffs, as well as other sanctions, have increased trade frictions. They made it difficult for the United States of America to sell certain goods to China and other nations. These disruptions have led to an increase in price inflation. These disruptions have led to increased price inflation, but they have also made companies aware of the fragility in their supply chains. They have forced them into a rethink on the design and implementation their supply chains.
The COVID-19 epidemic caused severe disruption in global supply chain operations, but the effects of the pandemic are still being felt. For example the Suez Canal blockage caused disruptions in supply chain for up to six weeks. This has caused a sharp rise in freight cost. In the UK, annual inflation has reached 9%.
It's difficult to ignore the fact the United States and China are engaged in a trade conflict. Supply chain leaders have to question the logic of relying so heavily on outsourced networks. They need to consider the risks of labor shortages resulting from economic shocks. Supply chain leaders should also consider the benefits of new forms of cross-border finance and regulation, which can expand global integration.
Despite the turbulence, the world remains a deeply interconnected place. If firms are open to a more holistic approach in their supply chains, global integration will bring benefits.
FAQ
What can I do to learn more about manufacturing?
Experience is the best way for you to learn about manufacturing. You can read books, or watch instructional videos if you don't have the opportunity to do so.
How can manufacturing efficiency improved?
First, we need to identify which factors are most critical in affecting production times. Next, we must find ways to improve those factors. If you don’t know how to start, look at which factors have the greatest impact upon production time. Once you identify them, look for solutions.
What are the essential elements of running a logistics firm?
You need to have a lot of knowledge and skills to manage a successful logistic business. Good communication skills are essential to effectively communicate with your suppliers and clients. You will need to know how to interpret data and draw conclusions. You will need to be able handle pressure well and work in stressful situations. You need to be innovative and creative to come up with new ways to increase efficiency. Strong leadership qualities are essential to motivate your team and help them achieve their organizational goals.
It is also important to be efficient and well organized in order meet deadlines.
What are manufacturing and logistic?
Manufacturing refers to the process of making goods using raw materials and machines. Logistics covers all aspects involved in managing supply chains, including procurement and production planning. As a broad term, manufacturing and logistics often refer to both the creation and delivery of products.
What types of jobs can you find in logistics
There are many types of jobs in logistics. Here are some:
-
Warehouse workers: They load and unload trucks, pallets, and other cargo.
-
Transport drivers - These are people who drive trucks and trailers to transport goods or perform pick-ups.
-
Freight handlers are people who sort and pack freight into warehouses.
-
Inventory managers – They manage the inventory in warehouses.
-
Sales representatives - They sell products.
-
Logistics coordinators - They plan and organize logistics operations.
-
Purchasing agents: They are responsible for purchasing goods and services to support company operations.
-
Customer service representatives - Answer calls and email from customers.
-
Shipping clerks – They process shipping orders, and issue bills.
-
Order fillers are people who fill orders based only on what was ordered.
-
Quality control inspectors are responsible for inspecting incoming and outgoing products looking for defects.
-
Others - There are many types of jobs in logistics such as transport supervisors and cargo specialists.
Are there any Manufacturing Processes that we should know before we can learn about Logistics?
No. You don't have to know about manufacturing processes before learning about logistics. But, being familiar with manufacturing processes will give you a better understanding about how logistics works.
Statistics
- According to a Statista study, U.S. businesses spent $1.63 trillion on logistics in 2019, moving goods from origin to end user through various supply chain network segments. (netsuite.com)
- You can multiply the result by 100 to get the total percent of monthly overhead. (investopedia.com)
- Many factories witnessed a 30% increase in output due to the shift to electric motors. (en.wikipedia.org)
- In 2021, an estimated 12.1 million Americans work in the manufacturing sector.6 (investopedia.com)
- According to the United Nations Industrial Development Organization (UNIDO), China is the top manufacturer worldwide by 2019 output, producing 28.7% of the total global manufacturing output, followed by the United States, Japan, Germany, and India.[52][53] (en.wikipedia.org)
External Links
How To
Six Sigma and Manufacturing
Six Sigma is defined by "the application SPC (statistical process control) techniques to achieve continuous improvements." Motorola's Quality Improvement Department, Tokyo, Japan, developed it in 1986. The basic idea behind Six Sigma is to improve quality by improving processes through standardization and eliminating defects. In recent years, many companies have adopted this method because they believe there is no such thing as perfect products or services. Six Sigma seeks to reduce variation between the mean production value. It is possible to measure the performance of your product against an average and find the percentage of time that it differs from the norm. If the deviation is excessive, it's likely that something needs to be fixed.
Understanding the dynamics of variability within your business is the first step in Six Sigma. Once you understand this, you can then identify the causes of variation. You'll also want to determine whether these variations are random or systematic. Random variations occur when people do mistakes. Symmetrical variations are caused due to factors beyond the process. For example, if you're making widgets, and some of them fall off the assembly line, those would be considered random variations. You might notice that your widgets always fall apart at the same place every time you put them together.
Once you've identified the problem areas you need to find solutions. It might mean changing the way you do business or redesigning it entirely. Once you have implemented the changes, it is important to test them again to ensure they work. If they don't work, you will need to go back to the drawing boards and create a new plan.