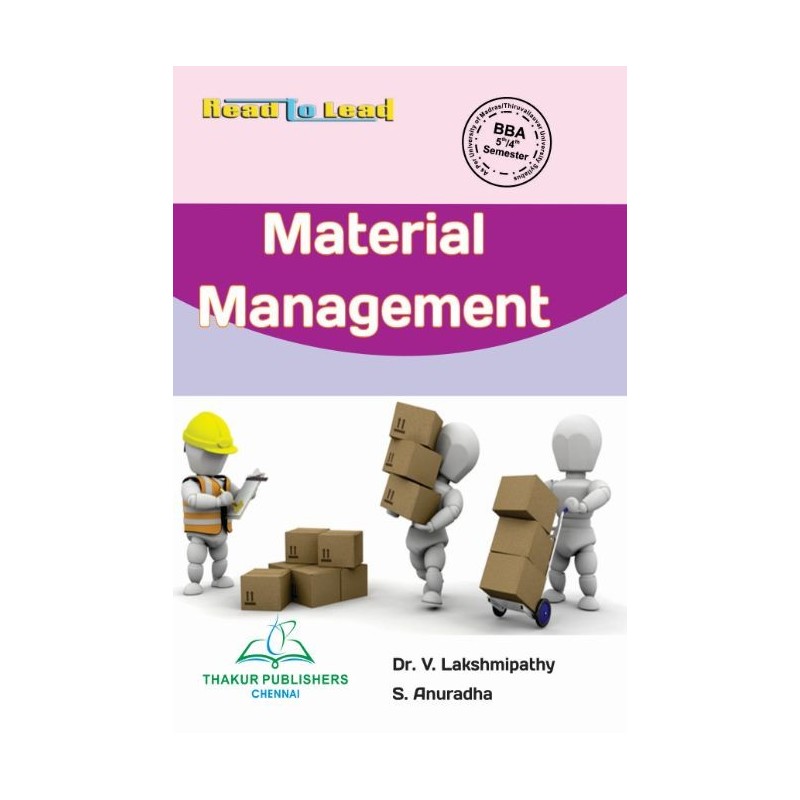
If you're a business owner looking for the latest trends in supply chain management, you should check out Supply Chain Management Review. The magazine, which is based in the U.S.A, has been publishing almost a decade. They cover issues like the changing nature and role of information technology. The publication offers an in-depth look at the industry, and is especially relevant to companies that manage a large supply chain.
The final stage in supply chain management is manufacturing
Supply chain management is a complicated process that involves five key elements. They include planning, sourcing raw ingredients, manufacturing, delivery and return, and logistics. Companies must be proficient in these areas to avoid costly bottlenecks. Manufacturing is essential for perishable goods because it requires prompt delivery.
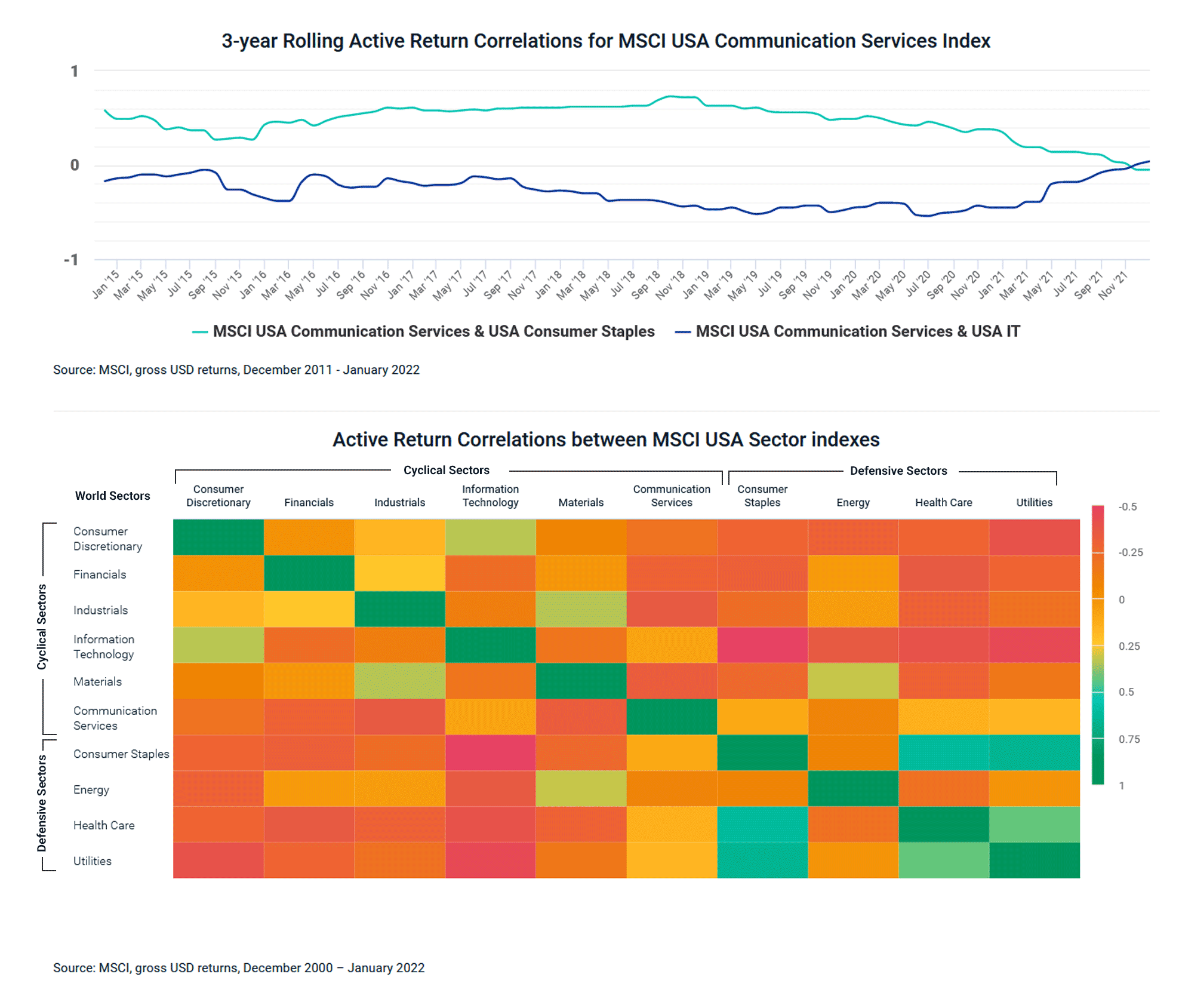
Reverse logistics
Reverse logistics management is essential to a company's bottom line. This service allows companies the opportunity to make use of existing infrastructure to cut costs and improve efficiency. This service can help improve a company's reputation by enabling them to adopt sustainable business practices. But reverse logistics can be difficult.
Flexible model
Businesses can have a flexible supply chain to meet their customers' needs when they are high or low. It relies on part segmentation, accurate stocking algorithms, and flexible planning, which includes incorporating automation on factory floors. Staples, for example, manufactures writing utensils and anticipates a surge of demand during back-to school season. It stocks up throughout the year.
Agile model
Organizations can use an Agile model to review their supply chain management. This will allow them to make major changes and ensure that they are responsive to any changes. Although delays and losses can occur due to the loss of significant manufacturing partners or logistical blocks, an agile supply system can quickly overcome these obstacles. The model also provides visibility, which enables supply chain stakeholders to continually improve the efficiency of their process. Additionally, organizations can outsource certain segments of their supply chain, which leads to lower costs. It allows businesses to plan ahead and reduce their stock levels.
Model for fast chain
This fast-chain model of supply chain management emphasizes speed, responsiveness, and is best suited for companies that frequently change product lines and compete for the same customers. This model is characterized by efficient inventory management and maximizing the use of production equipment and labor. It's best suited to businesses that produce high-end items with short lives. Additionally, it is a great model for businesses that want to quickly get products on the market.
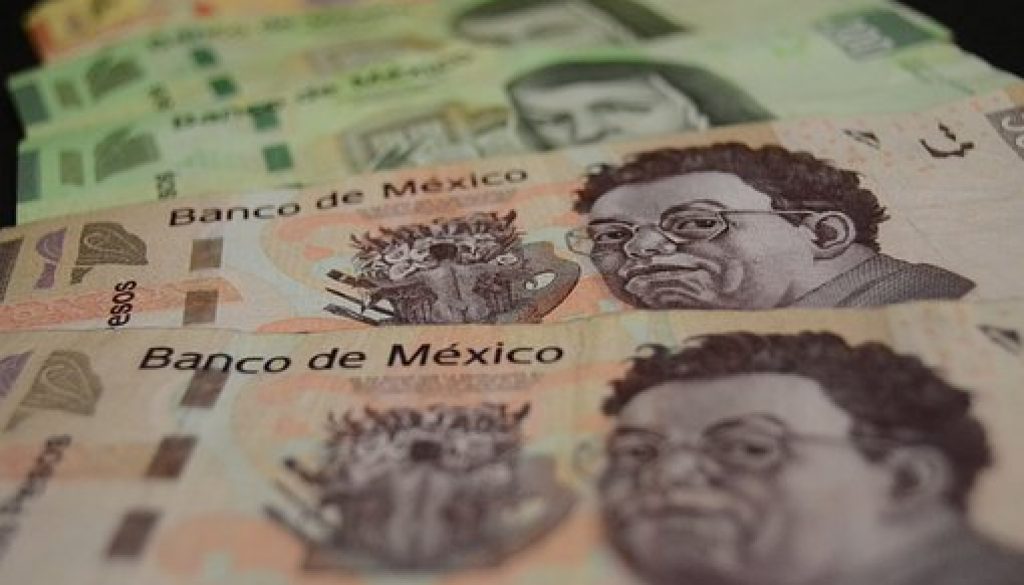
Supply chain management: Ethics
Companies must consider ethics in supply chain management as it has a significant impact on their bottom line and business performance. This issue impacts more than workers and factories: supply chain companies often face environmental, social and labor problems. A number of initiatives have been taken by organizations in order to promote ethical supply chains.
FAQ
What is production planning?
Production planning is the process of creating a plan that covers all aspects of production. This includes scheduling, budgeting and crew, location, equipment, props, and more. This document will ensure everything is in order and ready to go when you need it. It should also provide information about how best to produce the best results while on set. It should include information about shooting locations, casting lists, crew details, equipment requirements, and shooting schedules.
The first step in filming is to define what you want. You may have already chosen the location you want, or there are locations or sets you prefer. Once you have identified the scenes and locations, you can start to determine which elements are required for each scene. One example is if you are unsure of the exact model you want but decide that you require a car. This is where you can look up car models online and narrow down your options by choosing from different makes and models.
After you have chosen the right car, you will be able to begin thinking about accessories. Do you have people who need to be seated in the front seat? Maybe you need someone to move around in the back. Perhaps you would like to change the interior colour from black to white. These questions will help determine the look and feel you want for your car. Another thing you can do is think about what type of shots are desired. What type of shots will you choose? Maybe you want to show the engine and the steering wheel. This will allow you to determine the type of car you want.
Once you've determined the above, it is time to start creating a calendar. You can use a schedule to determine when and where you need it to be shot. Every day will have a time for you to arrive at the location, leave when you are leaving and return home when you are done. This way, everyone knows what they need to do and when. You can also make sure to book extra staff in advance if you have to hire them. There is no point in hiring someone who won't turn up because you didn't let him know.
Your schedule will also have to be adjusted to reflect the number of days required to film. Some projects can be completed in a matter of days or weeks. Others may take several days. You should consider whether you will need more than one shot per week when creating your schedule. Multiple takes of the same location will lead to higher costs and take more time. If you are unsure if you need multiple takes, it is better to err on the side of caution and shoot fewer takes rather than risk wasting money.
Budgeting is another crucial aspect of production plan. As it will allow you and your team to work within your financial means, setting a realistic budget is crucial. If you have to reduce your budget due to unexpected circumstances, you can always lower it later. It is important to not overestimate how much you will spend. If you underestimate how much something costs, you'll have less money to pay for other items.
Planning production is a tedious process. Once you have a good understanding of how everything works together, planning future projects becomes easy.
What are the 7 Rs of logistics?
The acronym 7Rs of Logistics refers to the seven core principles of logistics management. It was developed by the International Association of Business Logisticians (IABL) and published in 2004 as part of its "Seven Principles of Logistics Management" series.
The following letters make up the acronym:
-
Responsible - to ensure that all actions are within the legal requirements and are not detrimental to others.
-
Reliable – have faith in your ability and capability to keep promises.
-
Use resources effectively and sparingly.
-
Realistic – consider all aspects of operations, from cost-effectiveness to environmental impact.
-
Respectful - show respect and treat others fairly and fairly
-
You are resourceful and look for ways to save money while increasing productivity.
-
Recognizable provides value-added products and services to customers
What does manufacturing industry mean?
Manufacturing Industries are those businesses that make products for sale. Consumers are those who purchase these products. These companies employ many processes to achieve this purpose, such as production and distribution, retailing, management and so on. They create goods from raw materials, using machines and various other equipment. This includes all types if manufactured goods.
How can manufacturing overproduction be reduced?
The key to reducing overproduction lies in developing better ways to manage inventory. This would reduce the time spent on unproductive activities like purchasing, storing and maintaining excess stock. This will allow us to free up resources for more productive tasks.
You can do this by adopting a Kanban method. A Kanbanboard is a visual tool that allows you to keep track of the work being done. A Kanban system allows work items to move through several states before reaching their final destination. Each state has a different priority level.
As an example, if work is progressing from one stage of the process to another, then the current task is complete and can be transferred to the next. But if a task remains in the beginning stages it will stay that way until it reaches its end.
This allows for work to continue moving forward, while also ensuring that there is no work left behind. Managers can see how much work has been done and the status of each task at any time with a Kanban Board. This information allows managers to adjust their workflow based off real-time data.
Lean manufacturing can also be used to reduce inventory levels. Lean manufacturing seeks to eliminate waste from every step of the production cycle. Anything that doesn't add value to the product is considered waste. The following are examples of common waste types:
-
Overproduction
-
Inventory
-
Unnecessary packaging
-
Exceed materials
By implementing these ideas, manufacturers can improve efficiency and cut costs.
Statistics
- [54][55] These are the top 50 countries by the total value of manufacturing output in US dollars for its noted year according to World Bank.[56] (en.wikipedia.org)
- (2:04) MTO is a production technique wherein products are customized according to customer specifications, and production only starts after an order is received. (oracle.com)
- It's estimated that 10.8% of the U.S. GDP in 2020 was contributed to manufacturing. (investopedia.com)
- In 2021, an estimated 12.1 million Americans work in the manufacturing sector.6 (investopedia.com)
- According to a Statista study, U.S. businesses spent $1.63 trillion on logistics in 2019, moving goods from origin to end user through various supply chain network segments. (netsuite.com)
External Links
How To
How to Use Six Sigma in Manufacturing
Six Sigma is "the application statistical process control (SPC), techniques for continuous improvement." Motorola's Quality Improvement Department developed it at their Tokyo plant in Japan in 1986. The basic idea behind Six Sigma is to improve quality by improving processes through standardization and eliminating defects. Many companies have adopted Six Sigma in recent years because they believe that there are no perfect products and services. The main goal of Six Sigma is to reduce variation from the mean value of production. This means that if you take a sample of your product, then measure its performance against the average, you can find out what percentage of the time the process deviates from the norm. If the deviation is excessive, it's likely that something needs to be fixed.
Understanding how variability works in your company is the first step to Six Sigma. Once you understand this, you can then identify the causes of variation. These variations can also be classified as random or systematic. Random variations are caused when people make mistakes. While systematic variations are caused outside of the process, they can occur. For example, if you're making widgets, and some of them fall off the assembly line, those would be considered random variations. If however, you notice that each time you assemble a widget it falls apart in exactly the same spot, that is a problem.
Once you've identified the problem areas you need to find solutions. You might need to change the way you work or completely redesign the process. Once you have implemented the changes, it is important to test them again to ensure they work. If they didn't work, then you'll need to go back to the drawing board and come up with another plan.