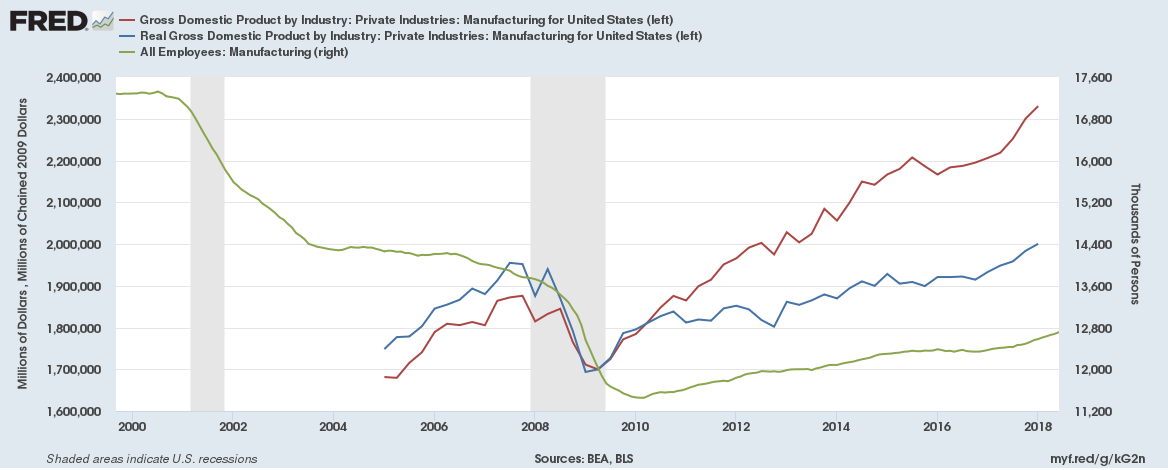
Advanced manufacturing refers to the application of advanced technology to enhance products and processes. The technology used to achieve this can be classified as "advanced," "innovative," or "cutting edge." This is because advanced manufacturing has become more common in the manufacturing industry. Below are some examples of advanced manufacturing. These are the most popular technologies in advanced manufacturing.
Continuous manufacturing
Continuous manufacturing dates back as far as the 1700s. It was used to produce pigiron in blast furnaces. The concept has since spread across various industries, including the automotive, food, oil and refining, chemicals, and pulp and paper industries. Continuous manufacturing has captured the attention of CMOs from top pharma and other big players in the biopharmaceutical market.
In a recent commentary, FDA and its collaborators discussed the benefits to continuous manufacturing when producing therapeutic proteins. The legislation will create national centers that can help advance the field and create standards for companies. This legislation is intended to improve the creation and use of medical products. It would encourage companies to use continuous production to improve and develop products. But, it is crucial to ensure that continuous production processes are safe.
Automated processes
It is hard to overstate the benefits of automation in advanced manufacturing. Automation is often the best way to maximize floor space and increase production efficiency. In order to reduce costs and increase production efficiency, manufacturers can collect data and leverage automation technologies. Automation in the process industry also helps to save time and money. Although initial investments can be costly, automation will eventually improve a company's bottom line.
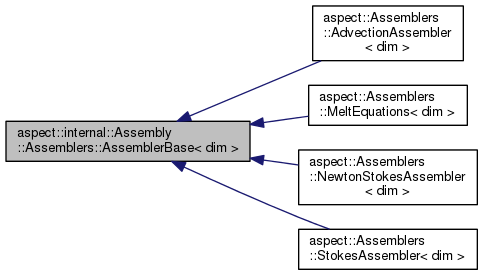
Companies are now combining automated manufacturing processes with advanced manufacturing processes. Audi is an example of a company that uses automated welding to bond its products. This allows them to cut down on production time and also saves energy and weight. Advanced manufacturing techniques, such as regenerative braking for conveyor systems are used. 3D printing, which is a major advancement in manufacturing, has only recently been adopted by mainstream companies. But what makes it so attractive to manufacturers?
Internet of Things (IoT).
Manufacturing is being transformed by the IIoT revolution. This revolution uses sensors to monitor machinery and processes. These sensors collect data in different areas of the manufacturing process to feed into a central hub. This data can then be analyzed to help optimize processes and eliminate waste. Advanced manufacturers use IIoT to monitor production processes and optimize their output. The IIoT is the industrial version of connected key fobs.
To deploy IIoT effectively and efficiently, you need a roadmap and the development capabilities to create use cases. An automaker has provided the following roadmap:
Cost-effectiveness
Advanced manufacturing costs are not always comparable to conventional production systems. The traditional cost-benefit analysis, however, is not sufficient to evaluate economic benefits. A holistic model that incorporates both benefits and costs can be used to identify new advantages and speed decision-making. Munker and Schroer have developed a cost-benefit model that addresses key issues in AMS implementation.
Advances in information technology are rapidly changing the face of manufacturing and their costs. The production systems are becoming more intelligent and networked. Cost pressures are increasing the focus on productivity and the ability of companies to respond to customers' needs. The rapid adoption and use of advanced manufacturing technologies will increase the effectiveness of existing technologies as well their cost-effectiveness. As the industry digitizes, this will likely lead to a rapid adoption of such technologies.
Human error reduction
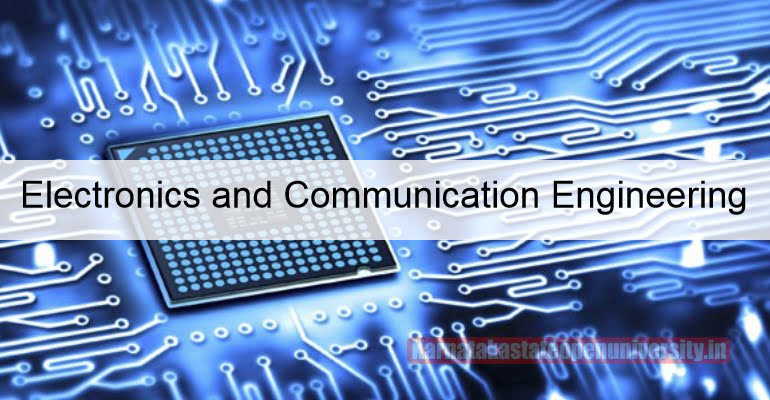
Humans make mistakes. However, the process that is used to make a product usually protects it. Human error can occur when employees fail to follow the written process or misunderstand instructions. When they make drugs, pharmaceutical laboratories for example must follow certain procedures. Sometimes, employees might believe that they have learned the process and are familiar with the precise amounts of ingredients. So they start to make the mixture, without ever consulting the written instructions.
Human error can also be reduced by effective communication between junior staff and senior managers. Employers who are treated harshly will make mistakes. Therefore, managers should avoid punishing employees who ask questions. Employees must feel comfortable asking questions. They won't take corrective measures if they don't like the way they are treated. It is important to establish a healthy relationship between senior and junior employees. Also, it is important to address communication issues in a polite and professional manner.
FAQ
What makes a production planner different from a project manger?
A production planner is more involved in the planning phase of the project than a project manger.
What are the 4 types manufacturing?
Manufacturing refers to the transformation of raw materials into useful products by using machines and processes. It involves many different activities such as designing, building, testing, packaging, shipping, selling, servicing, etc.
What is the role of a manager in manufacturing?
The manufacturing manager should ensure that every manufacturing process is efficient and effective. They should also be aware and responsive to any company problems.
They should also be able and comfortable communicating with other departments like sales and marketing.
They must also keep up-to-date with the latest trends in their field and be able use this information to improve productivity and efficiency.
Statistics
- You can multiply the result by 100 to get the total percent of monthly overhead. (investopedia.com)
- According to the United Nations Industrial Development Organization (UNIDO), China is the top manufacturer worldwide by 2019 output, producing 28.7% of the total global manufacturing output, followed by the United States, Japan, Germany, and India.[52][53] (en.wikipedia.org)
- [54][55] These are the top 50 countries by the total value of manufacturing output in US dollars for its noted year according to World Bank.[56] (en.wikipedia.org)
- It's estimated that 10.8% of the U.S. GDP in 2020 was contributed to manufacturing. (investopedia.com)
- Many factories witnessed a 30% increase in output due to the shift to electric motors. (en.wikipedia.org)
External Links
How To
How to use Lean Manufacturing in the production of goods
Lean manufacturing is a management style that aims to increase efficiency and reduce waste through continuous improvement. It was first developed in Japan in the 1970s/80s by Taiichi Ahno, who was awarded the Toyota Production System (TPS), award from KanjiToyoda, the founder of TPS. Michael L. Watkins published the "The Machine That Changed the World", the first book about lean manufacturing. It was published in 1990.
Lean manufacturing is often described as a set if principles that help improve the quality and speed of products and services. It emphasizes eliminating waste and defects throughout the value stream. Lean manufacturing is also known as just in time (JIT), zero defect total productive maintenance(TPM), and five-star (S). Lean manufacturing seeks to eliminate non-value added activities, such as inspection, work, waiting, and rework.
In addition to improving product quality and reducing costs, lean manufacturing helps companies achieve their goals faster and reduces employee turnover. Lean manufacturing is a great way to manage the entire value chain including customers, suppliers, distributors and retailers as well as employees. Lean manufacturing practices are widespread in many industries. Toyota's philosophy is the foundation of its success in automotives, electronics and appliances, healthcare, chemical engineers, aerospace, paper and food, among other industries.
Five basic principles of Lean Manufacturing are included in lean manufacturing
-
Define Value- Identify the added value your company brings to society. What makes you stand out from your competitors?
-
Reduce Waste – Eliminate all activities that don't add value throughout the supply chain.
-
Create Flow. Ensure that your work is uninterrupted and flows seamlessly.
-
Standardize & Simplify - Make processes as consistent and repeatable as possible.
-
Build Relationships - Establish personal relationships with both internal and external stakeholders.
Although lean manufacturing isn't a new concept in business, it has gained popularity due to renewed interest in the economy after the 2008 global financial crisis. Many businesses are now using lean manufacturing to improve their competitiveness. According to some economists, lean manufacturing could be a significant factor in the economic recovery.
Lean manufacturing is now becoming a common practice in the automotive industry, with many benefits. These benefits include increased customer satisfaction, reduced inventory levels and lower operating costs.
Any aspect of an enterprise can benefit from Lean manufacturing. However, it is particularly useful when applied to the production side of an organization because it ensures that all steps in the value chain are efficient and effective.
There are three types principally of lean manufacturing:
-
Just-in Time Manufacturing, (JIT): This kind of lean manufacturing is also commonly known as "pull-systems." JIT stands for a system where components are assembled on the spot rather than being made in advance. This strategy aims to decrease lead times, increase availability of parts and reduce inventory.
-
Zero Defects Manufacturing, (ZDM): ZDM is focused on ensuring that no defective products leave the manufacturing facility. If a part is required to be repaired on the assembly line, it should not be scrapped. This is also true for finished products that require minor repairs before shipping.
-
Continuous Improvement (CI: Continuous improvement aims to increase the efficiency of operations by constantly identifying and making improvements to reduce or eliminate waste. Continuous improvement involves continuous improvement of processes and people as well as tools.