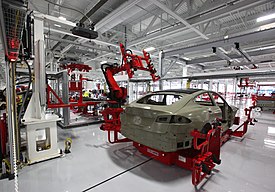
Typically, tool and die makers work in machine shops. They operate lathes, milling machines, and other types of machine tools. They may also repair tools or dies for machinists. They might also design tools for customers.
Tool and die makers are required to maintain high standards of quality and precision in their work. They check the quality of their work and inspect the finished product. Tool and die makers may work with engineers to improve processes. To see the tool in action, they may visit a customer's facility. They are expected also to keep their work area tidy and organized. They might wear protective gear. They might suggest new tools that make the process easier.
Tool and die makers typically work 40 hours a week. They may also be expected moderately to heavy lifting. A solid educational background is required. Employers may prefer an associate's, bachelor's, or master's degree in a similar field. They may also get formal on-thejob training or be part of apprenticeship programs.

Four-year apprenticeship programs for tool and diemakers are typically offered by employers. They get on-the job training from an experienced worker throughout the apprenticeship program. They also participate in technical college classes at night. The program includes hands-on training, as well as classroom instruction. They may also be given the chance to program computer controlled machine tools. They may also have the opportunity to advance to supervisory or managerial positions.
Tool and die makers typically have a high school diploma or equivalent. They may also have a degree in a technical field, such as physics or engineering. They might have also had training in science, math, or both. This training is often helpful.
Tool and diemakers need good eyesight. They need to be able to concentrate and have patience. They also need physical strength to handle machinery. They must have a strong work ethic, and be able to lift heavy loads. They must be able read and understand engineering drawings and specifications. They should also possess good interpersonal skills. They must also possess strong computer skills. They might be required to maintain computer numerically managed (CNC-) machines.
Tool and die makers need to have an analytical mind. They must be able to comprehend how tools and dies function and how they can be repaired. They must also be able to solve problems and have mechanical ability. They may need to learn new techniques in machining. They need to have solid digital skills such as computer-aided designing (CAD) or computer-aided manufacturing software (CAM). They must also be able to sell. They should be able and willing to work both independently and collaboratively.
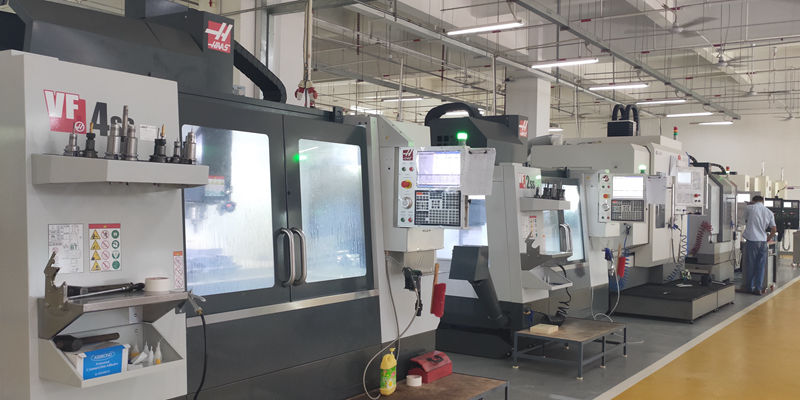
Apprentices are expected to work 40 hours a week during their apprenticeship program. They take classes in the evening and work at a job during daytime. They eventually take on more challenging assignments. Most apprenticeships require a high school diploma or equivalent. They should also take courses on science and math.
Some tool and dentists go on to obtain a bachelor's (or master's) degree. The average wage for tool- and die-makers is $56,186. However, automation is predicted to lower their chances of finding work in the future.
FAQ
What is the distinction between Production Planning or Scheduling?
Production Planning (PP), is the process of deciding what production needs to take place at any given time. Forecasting demand is one way to do this.
Scheduling refers the process by which tasks are assigned dates so that they can all be completed within the given timeframe.
What are manufacturing & logistics?
Manufacturing is the process of creating goods from raw materials by using machines and processes. Logistics encompasses the management of all aspects associated with supply chain activities such as procurement, production planning, distribution and inventory control. It also includes customer service. Logistics and manufacturing are often referred to as one thing. It encompasses both the creation of products and their delivery to customers.
How can I find out more about manufacturing?
Practical experience is the best way of learning about manufacturing. You can also read educational videos or take classes if this isn't possible.
How can efficiency in manufacturing be improved?
First, determine which factors have the greatest impact on production time. The next step is to identify the most important factors that affect production time. If you don't know where to start, then think about which factor(s) have the biggest impact on production time. Once you've identified them, try to find solutions for each of those factors.
What are the 7 R's of logistics?
The 7R's of Logistics is an acronym for the seven basic principles of logistics management. It was developed and published by the International Association of Business Logisticians in 2004 as part of the "Seven Principles of Logistics Management".
The following letters form the acronym:
-
Responsible – ensure that all actions are legal and don't cause harm to anyone else.
-
Reliable: Have faith in your ability or the ability to honor any promises made.
-
Reasonable - make sure you use your resources well and don't waste them.
-
Realistic – Consider all aspects, including cost-effectiveness as well as environmental impact.
-
Respectful: Treat others with fairness and equity
-
Responsive - Look for ways to save time and increase productivity.
-
Recognizable - provide customers with value-added services.
What type of jobs is there in logistics
There are different kinds of jobs available in logistics. Some of them are:
-
Warehouse workers – They load and unload pallets and trucks.
-
Transportation drivers - They drive trucks and trailers to deliver goods and carry out pick-ups.
-
Freight handlers – They sort and package freight at warehouses.
-
Inventory managers – They manage the inventory in warehouses.
-
Sales representatives: They sell products to customers.
-
Logistics coordinators - They organize and plan logistics operations.
-
Purchasing agents - They purchase goods and services needed for company operations.
-
Customer service agents - They answer phone calls and respond to emails.
-
Shipping clerks - They process shipping orders and issue bills.
-
Order fillers – They fill orders based upon what was ordered and shipped.
-
Quality control inspectors: They inspect outgoing and incoming products for any defects.
-
Others - There are many types of jobs in logistics such as transport supervisors and cargo specialists.
Statistics
- [54][55] These are the top 50 countries by the total value of manufacturing output in US dollars for its noted year according to World Bank.[56] (en.wikipedia.org)
- You can multiply the result by 100 to get the total percent of monthly overhead. (investopedia.com)
- In 2021, an estimated 12.1 million Americans work in the manufacturing sector.6 (investopedia.com)
- In the United States, for example, manufacturing makes up 15% of the economic output. (twi-global.com)
- It's estimated that 10.8% of the U.S. GDP in 2020 was contributed to manufacturing. (investopedia.com)
External Links
How To
How to use lean manufacturing in the production of goods
Lean manufacturing (or lean manufacturing) is a style of management that aims to increase efficiency, reduce waste and improve performance through continuous improvement. It was developed in Japan during the 1970s and 1980s by Taiichi Ohno, who received the Toyota Production System (TPS) award from TPS founder Kanji Toyoda. The first book published on lean manufacturing was titled "The Machine That Changed the World" written by Michael L. Watkins and published in 1990.
Lean manufacturing can be described as a set or principles that are used to improve quality, speed and cost of products or services. It emphasizes eliminating waste and defects throughout the value stream. Lean manufacturing is called just-in-time (JIT), zero defect, total productive maintenance (TPM), or 5S. Lean manufacturing emphasizes reducing non-value-added activities like inspection, rework and waiting.
In addition to improving product quality and reducing costs, lean manufacturing helps companies achieve their goals faster and reduces employee turnover. Lean manufacturing is a great way to manage the entire value chain including customers, suppliers, distributors and retailers as well as employees. Many industries worldwide use lean manufacturing. Toyota's philosophy is a great example of this. It has helped to create success in automobiles as well electronics, appliances and healthcare.
Five fundamental principles underlie lean manufacturing.
-
Define value - Find out what your business contributes to society, and what makes it different from other competitors.
-
Reduce Waste – Eliminate all activities that don't add value throughout the supply chain.
-
Create Flow – Ensure that work flows smoothly throughout the process.
-
Standardize and simplify - Make your processes as consistent as possible.
-
Building Relationships – Establish personal relationships with both external and internal stakeholders.
Although lean manufacturing isn't a new concept in business, it has gained popularity due to renewed interest in the economy after the 2008 global financial crisis. Many businesses have adopted lean production techniques to make them more competitive. According to some economists, lean manufacturing could be a significant factor in the economic recovery.
Lean manufacturing is now becoming a common practice in the automotive industry, with many benefits. These benefits include increased customer satisfaction, reduced inventory levels and lower operating costs.
Any aspect of an enterprise can benefit from Lean manufacturing. However, it is particularly useful when applied to the production side of an organization because it ensures that all steps in the value chain are efficient and effective.
There are three main types of lean manufacturing:
-
Just-in Time Manufacturing (JIT), also known as "pull system": This form of lean manufacturing is often referred to simply as "pull". JIT refers to a system in which components are assembled at the point of use instead of being produced ahead of time. This approach reduces lead time, increases availability and reduces inventory.
-
Zero Defects Manufacturing: ZDM ensures that no defective units leave the manufacturing plant. If a part needs to be fixed during the assembly line, it should be repaired rather than scrapped. This applies to finished goods that may require minor repairs before shipment.
-
Continuous Improvement (CI): CI aims to improve the efficiency of operations by continuously identifying problems and making changes in order to eliminate or minimize waste. Continuous improvement refers to continuous improvement of processes as well people and tools.